Prosessien ja työkoneiden säätäminen ja asettaminen on vaativa tehtävä, jolla on erittäin suuri vaikutus laatuun ja virheellisten tuotteiden määrään. Sama koskee myös hallinto- ja palveluprosesseja vaikka harvoin näin mielletään. Ei ole sama, syntyykö 1-5 % viallisia tuotteita vai 10-40 % tai onko läpimenoaika 2-3 päivää vai 3-5 viikkoa. Ongelma on usein puutteellisesta prosessin asettamisesta ja säätämisestä.
Yllättävää on, että vain ani harva prosessin omistaja, insinööri tai ammattimies/-nainen tietää menetelmän tai menetelmiä, millä säännöillä asetus, prosessin keskiarvo, tulisi optimaalisesti tapahtua, jotta virheet/läpimenoajat ovat minimissä ja asiakastyytyväisyys maksimissa.
Artikkelisarjassa esitetään lukuisia systemaattisia menetelmiä ja sääntöjä siitä, kuinka prosessin voi asettaa ja säätää ideaalitilaan.
OSA I: Ensimmäinen artikkeli käsittelee tilannetta, jossa on yksi tunnettu tekijä, säätäjä, jolla on suoraan vaikutus prosessin keskiarvoon. Lisäksi mittaustuloksia, näytteitä, voidaan saada useita ”samassa ajanjaksossa”. Prosessin läpimenoaika on lyhyt.
OSA II: Toisessa artikkelissa käsitellään perättäistä ”sekvenssi”-säätötapahtumaa, joka sopii erityisesti raskaiden prosessien ja rikkoutuvia tuotteita tuottavien prosessien säätöön, jossa on käytettävissä vain yksi mittaustulos tietyin aikavälein esim. 1kpl/tunti tai vuoro. Prosessin läpimenoaika on pitkä. Artikkelissa käsitellään myös nopeaa prosessin suorituskykytestausta ja siihen liittyvää esivalvontakorttia (Pre-Control).
OSA III: Kolmannessa artikkelissa käsitellään tilannetta, jossa ei ole tunnettua selkeää säätävää/ohjaavaa tekijää tai tekijöitä on lukuisia, joiden avulla prosessia ”säädetään”. Tyypillisesti tilanne esiintyy palveluprosesseissa ja monimutkaisissa tuotantoprosesseissa, joiden tuotteet edustavat korkeaa teknologista tasoa. Asentajakoe mahdollistaa nopean ja tehokkaan tavan. Säädön sijaan käytetään usein termiä prosessin kyvykkyys ja sen parantaminen. Six Sigma tai Lean Six Sigma edustavat menetelmiä, joilla asetus ja säätö voidaan toteuttaa tai vaihtoehtoisesti suorituskykyä voidaan nostaa.
Prosessin ideaalitila ja sen ylläpito
Ideaalitila kaikille prosesseille ja työkoneille on, että ne tuottavat palveluja, tuotteita, osia, jatkuvasti 0-virheellä ja maksimitehokkuudella/-nopeudella ja minimi läpimenoajalla. Millä ehdoilla nämä on saavutettavissa?
Professori Don Wheeler/1/ kutsuu tätä tilaa ideaaliseksi tilanteeksi, joka on saavutettavissa toteuttamalla neljä ehtoa:
1. Prosessin on oltava luontaisesti kyvykäs tuottamaan yhdenmukaisia tuloksia. Toisin sanoen prosessin on oltava stabiili yli ajan.
2. Valmistajan on toimittava prosessissa stabiilisti ja yhdenmukaisella tavalla. Operaation – prosessin tai koneen – olosuhteita ei voi valita tai muuttaa mielivaltaisesti!
3. Prosessin keskiarvo on asetettava ja ylläpidettävä sopivalla tasolla.
4. Prosessin luonnolliset toleranssit on oltava pienemmät kuin tuotteen/palvelun spesifioidut toleranssit. Prosessin on oltava kyvykäs suhteessa asetettuihin vaatimuksiin/toleransseihin.
Kun nämä neljä ehtoa on täytetty, palvelun tuottaja tai valmistaja voi olla vakuuttunut, että yhtään virheellistä palvelua tai tuotetta ei synny. Jos yksikin näistä ehdoista ei ole täytetty, syntyy virheellisiä tai viallisia palveluja tai tuotteita/osia.
Kuinka voi tietää ja varmistaa, että nämä neljä ehtoa on voimassa? Onko prosessi luontaisesti stabiili (1)? Ohjauskortit kertovat stabiilisuuden.
Toimitaanko prosessin käsittelyssä stabiilisti (2) ja onko prosessin keskiarvo asetettu sopivalle tasolle (3)? Tähänkin antaa vastauksen ohjauskortit.
Ovatko prosessin luonnolliset toleranssit spesifisoitujen toleranssien sisäpuolella (4)? Tähänkin antaa vastauksen ohjauskortit.
Ohjauskortit kertovat tilan, jossa ollaan, mutta ei sitä, kuinka tilaan päästään. Vaaditaan siis aktiviteetti – prosessin keskiarvon asettaminen ja säätäminen!
P.S. Ohjaus-/valvontakorteista (SPC) olemme kirjoittaneet useita artikkeleita!/3,4,5,6,7/
Prosessin keskiarvon asettaminen
Ideaalitilan yksi ehto neljästä on keskiarvon asettaminen ja ylläpitäminen sopivalla tasolla.
Jos prosessin tavoite ei ole oikea, seurauksena on kaikki seuraukset, jotka tulevat palvelun, tuotteen, osan vaikeammasta käytettävyydestä ja korkeammista kustannuksista aina virheellisiin ja viallisiin palveluihin, reklamaatioihin ja kustannuksiin saakka.
Yleisesti on vallalla kaksi näkemystä ”sopivalle tasolle”. Vanha perinteinen speksien eli toleransseihin perustuva eksakti näkemys hävikistä, jota syntyy vain virheistä. Näkemys hyvästä on luonteeltaan mustavalkoinen, jossa ei ole huomioitu prosessia ja sen tilastollista luonnetta. On riittävää, että toleranssit täytetään (conformance)! Vain toleranssin ylitys/alitus on hävikkiä ja hukkaa. Onnistumista mitataan virheprosentin avulla. Mitä pienempi virheprosentti sen parempi! Puhutaan usein tuotevalvonnasta/tarkastuksesta.
Toisessa tilanteessa tavoite/nominaali on tärkein tavoite ja toleranssit (LSL, ULS) toissijaiset. Kun tavoitteesta poiketaan, syntyy kasvavassa määrin hävikkiä, joka muodostuu vaikeammasta käytettävyydestä, heikommasta luotettavuudesta aina hylkäys ja romutuskustannuksiin saakka. Tätä heikkenemistä voidaan kuvata Taguchin hävikkifunktiolla L= k(y-T)2 = k(σ2+(yav-T)2).
Prosessin tilastollinen luonne ”keskiarvo, yav” ja luonnollinen ”hajonta, σ” (sigma) on aina huomioitava asettamisessa. Prosessin hajonta on saatava niin pieneksi kuin mahdollista ja keskiarvo olisi asetettava/säädettävä nominaaliin T, jolloin hävikki on L= 0.
Länsimaissa käytetään taloudellisen rahassa ilmaistun hävikkifunktion sijaan suorituskykyindeksejä, jotka kuvaavat luontaisen kyvykkyyden ja osuuksia indekseillä. Taguchin hävikkifunktio voidaankin esittää suorituskykyindeksillä Cpk= Cp(1-k). Asetuksessa ja säädössä pyritään ”k” saamaan niin pieneksi kuin mahdollista. Indekseihin palataan tarkemmin OSA II:ssa tai artikkelissa/3-7/.
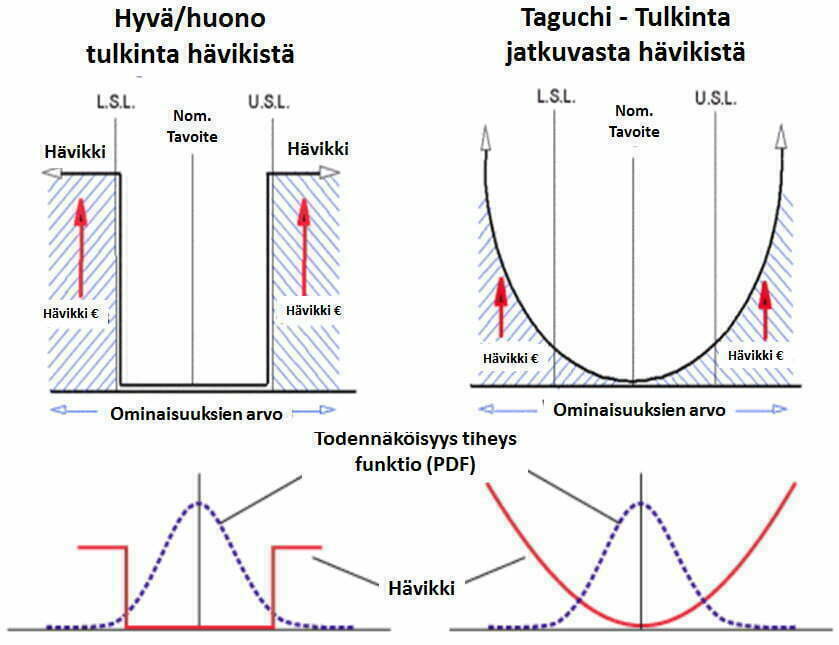
Yrityksissä vallitsee asettamisen suhteen usein epätietoisuutta näiden kahden ajattelutavan yhdistämisestä erityisesti silloin, jos toleranssin sisällä olevaa hävikkiä ei arvosteta/huomioida. Eikö riitä, että asetamme koneet toleranssien mukaan ja minimoidaan tuotevirheet!
Valitettavasti tämä ei onnistu – ei ole koskaan onnistunut yli 200 vuoden aikana toleranssien keksimisen jälkeen. Luonto käyttäytyy tilastollisesti. Meillä on vääjäämätön suurempi tai pienempi satunnainen vaihtelu, sigma, jokaisessa prosessissa. Vaihtelu on satunnaista, mutta samalla ennustettavaa, joka estää pelkästään toleranssien käytön asettamisessa!
Asettamisen oletukset: Oletetaan, että tuotteen ominaisuuden keskiarvo on pidettävä lähellä jotain arvoa (tavoite T, nominaali). Lisäksi oletetaan, että on mahdollista muuttaa prosessin keskiarvoa säätämällä prosessin asetuksia esim. lämpötilasäädintä, painetta, CNC-koneen asetusmittaa, palveluprosessissa keskeneräinen työ WIP, palvelupisteiden miehitystila, palveluaika jne.
Tavanomainen menettely on ottaa muutama tuotemitta (näyte) ja käyttää näitä mittoja asetuksesta/säädöstä päättämiseen. Onko asetus oikein, onko säädetty tarpeeksi – olisiko lisättävä vai vähennettävä säätimen, ”nupin”arvoa tai ”näppäiltävä” ohjelmaan uusi arvo tai tehtävä jokin muu muutos palveluprosessiin.
Grubbsin sääntö asetuksen tekemiseen
Arvon, muutoksen, määrittämiseksi on olemassa hyvin yksinkertainen, tieteellisesti perusteltu ns. ”Grubbsin sääntö”/2/ säätämiseen:

Grubbsin sääntö on yksinkertainen ja helppo. Jokaisen säädön jälkeen teet vain sen suuruisen muutoksen, joka on tavoitteen ja mitatun arvon ero jaettuna säätöjen määrällä.
Grubbsin säännön (optimin) todistus on kohtuullisen hankala ja johtaa varianssiin, joka on (σx2+σe2)/n. Sääntö on johdettu valitettavasti reunaehdoilla, jotka eivät aina ole voimassa – prosessi kyvykäs. Tästä seuraa, että päättely on osin tilastollisesti rajoittunut ja voi johtaa joissain tilanteissa huonompaan lopputulokseen, tampering. Tämä tapahtuu erityisesti silloin, kun kone tai prosessi on jo alkujaan tavoitteessa ja samanaikaisesti vaihtelu on suuri!/1/.
Kuinka toimitaan ”oikein” säätämisessä?
On valittava sopiva tuotemittamäärä/näyte (n) ja sopiva päätössääntö (Δσ) säädön lopettamiselle, jotta menettely, asettaminen on tehokas. Oleellinen ero Grubbsin sääntöön on, että prosessin hajonta huomioidaan ja sen perusteella määritellään säätöproseduuri, asetus suunnitelma. Jos mittausten määrä ja päätössääntö eivät ole oikeita, päädytään väärään päätökseen. Menetetään aikaa, materiaalia, tuottavuutta ja laatua.
Asetuksen onnistumiseksi tarvitaan muutama selventävä käsite:
Prosessin tavoite, jolla kuvataan niitä asetuksia, joilla prosessin ohjaukset on asetettu. Esimerkiksi säätönuppi on asetettu 9,98, keskeneräistä työtä on 24 kpl tai 10 k€. Prosessiasetus koskee kaikkia niitä toimia, jotka johtaja/päällikkö/operaattori voi tehdä määritellessään ja suorittaessaan säätöä.
Prosessin keskiarvo on tuotteen ominaisuuden keskiarvo kaikista niistä tuotteista, jotka edellä kuvatulla asetuksella tuotetaan. Esimerkiksi se voisi olla 8,87, kun ”nuppi” on asennoissa 9,98.
Tavoite- eli nominaaliarvo on haluttu tuote/palvelutavoite, joka voi olla piirustukseen merkitty keskipiste, läpimenoaika tai asiakastyytyväisyyden maksimiarvo. Tätä arvoa tavoitellaan. Esimerkiksi 10,00.
Miten nämä kolme käsitettä voi erottaa toisistaan: prosessin tavoite on se, jonka asetat, prosessin keskiarvo on se minkä saat ja tavoite- eli nominaaliarvo on se, jota haluat.
Prosessiasetuksen tavoitteena on säätää prosessin tavoitetta niin kauan, että prosessin keskiarvo on riittävän lähellä nominaaliarvoa, jolla voidaan tuottaa tuotteita riittävän pienellä virheprosentilla, riittävällä nopeudella ja tuottavuudella.
Miksi ei aseteta heti suoraan riittävän lähelle nominaalia? Miksi ei tehdä juuri sellaisia tuotteita, jotka ovat nominaaliarvossa? Yksinkertaisesti siksi, että on olemassa näytevaihtelua, joka ei mahdollista riittävän tarkkaa estimaattia – tietoa – prosessin keskiarvosta. Tästä seuraa, että koskaan ei mitään prosessia tai työkonetta voida asettaa eksaktisti nominaali eli tavoite (target, T) arvoon.
Paras mitä käytännössä voidaan tehdä, on saada prosessin keskiarvo nominaaliarvoon suurimman osan ajasta, ei koko aikaa.
Tämä voidaan saavuttaa menettelyllä, jossa kerätään riittävä määrä dataa yhdessä sopivan päätössäännön kanssa huomioiden eri vaatimukset ja totutus- ja hävikkikustannukset.
Prosessin stabiilisuus
Koko menettely, jolla säädetään prosessin keskiarvoa, voi olla hyödytön, jos prosessi itsessään luontaisesti ei ole ohjauksessa. Jos prosessi ei ole ohjauksessa, silloin prosessilla ei ole yhtä keskiarvoa vaan lukuisia eri keskiarvoja ja hajontoja, joten asettaminen ei ole mahdollista.
Jos yrität asettaa prosessin keskiarvoa epästabiiliin prosessiin, on se yksinkertaisesti hukattuja toimenpiteitä. Jos tiedetään prosessin olevan epästabiili, on tehtävä toimenpiteitä erityissyiden tunnistamiseksi ja poistamiseksi mieluimmin kuin jatkuvasti rukata ohjauksia satunnaissyiden pohjalta. Voit käyttää laatutauluja tai muita SPC-menettelyjä prosessin stabiloimiseksi tunnistamalla erityissyyt.
Seuraavia asetusohjeita ei pitäisi käyttää ennen kuin ohjauskorteilla on todettu, että prosessi on ohjauksessa, stabiili. Sopivia ohjauskortteja ovat I-MR ja XbarR -kortit, jotka löytyvät esim. Minitabista. Jos erityissyitä esiintyy, niiden syyt on tunnistettava ja poistettava.
Asetuksen perusmenettely
Perusmenettely prosessin tavoitteen – säätöjen – asettamiseksi on erittäin yksinkertainen:
- Aseta prosessin tavoite (<2Δσ), tee säädöt (huom. prosessin keskiarvotavoite on eri asia kuin nominaali-tavoite T)
- Mittaa tietty määrä n osia ja laske näistä (näytteen) keskiarvo Xav
- Jos näytteen keskiarvo Xbar (X-viiva, Xav) EI OLE tietyn kriittisen etäisyyden Δσ sisällä mitattuna nominaaliarvosta, palaa kohtaan 1 ja tee lisäasetuksia/säätöjä
- Toteuta tuotantoajo, kun näytekeskiarvo Xav on vähemmin kuin Δσ mitattuna nominaaliarvosta T.
Kun operaattorille on annettu n ja Δσ , operaattori voi käyttää perusmenettelyä asettaessaan prosessin keskiarvon niin lähelle nominaalia arvoa T, kun on välttämätöntä. Hän laskee siis n suuruisen näytemäärän keskiarvon ja vertaa lukua Δσ:n. Säätöä ei saa tehdä kuitenkaan sen jälkeen, kun ollaan kriittisen välin sisällä. Tämä ei tarkenna ja pienennä keskiarvopoikkeamaa, vaan lisää epästabiilisuutta ja heikentää tulosta. Ilmiötä kutsutaan tamperoinniksi (tampering) tai paranteluksi (tweeking), joka heikentää tulosta. Tunnetaan myös Demingin suppilokokeena!

Niin kauan kuin operaattori käyttää tätä menettelyä, esimies ja operaattori voivat olla luottavaisia, että asetus on tehty oikein ja virheprosentti suunnitellun mukainen.
Mitkä ovat optimaaliset asetusarvoyhdistelmät ja niiden luotettavuusarvot?
Seuraavassa taulukossa on annettuna optimaaliset suunnitelmat A-H ja niihin liittyvät n ja Δσ yhdistelmät. Taulukossa on suunnitelman takaamat keskimääräiset ajat (määrät), jonka ajan prosessi on annetulla välillä nominaalin ympärillä.
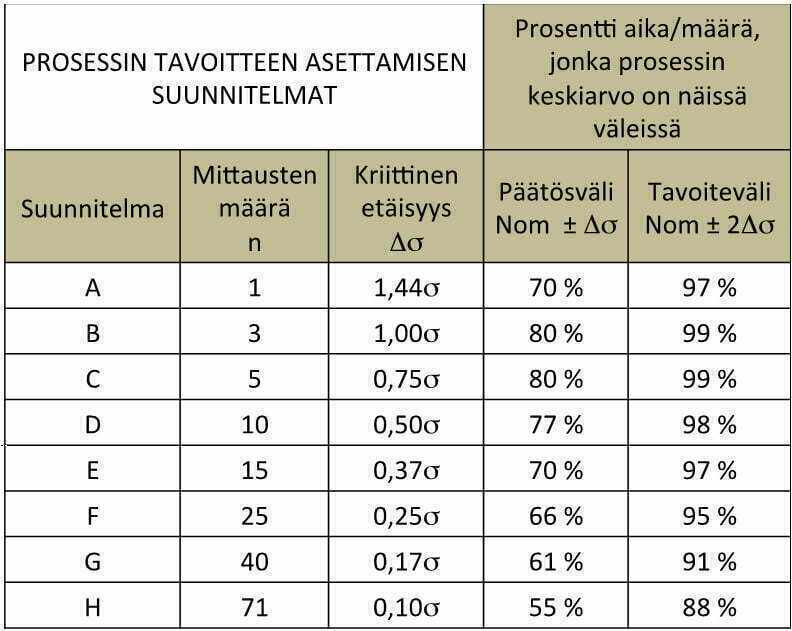
Löydät taulukon arvoja vastaavat arvot Minitabin Stat -> Basic Statisiti ->1-sample t testauksesta ja ->Power and Sample Size ->1-sample t tai Minitab Assistant Hypotesis Tests 1-sample t.
Suunnitelman valinta tavoitevälin 2 perusteella
Kuinka organisaatio (tuotantopäällikkö/insinööri tai laatupäällikkö/insinööri) määrittelee käytettävän suunnitelman tavoitevälin 2Δσ perusteella (-> näytemäärän n ja kriittisen etäisyyden Δσ nominaaliarvosta)?
Päätös suunnitelman vallinnasta voi perustua mm. seuraaviin seikkoihin:
- Prosessin keskiarvo on määritetty suunnittelu- tai asiakasvaatimuksissa erillisenä toleranssista esim. keskiarvo: nominaali ± 2,05 ja toleranssi: nominaali ±3
- Asiakasvaatimus on sidottu Cpk tai Ppk indeksiin toleranssin lisäksi. Autoteollisuuden standardi PPAP (AIAG: Production Part Approval Process) määrittelee prosessivaatimukseksi Ppk>1,67
- Asiakas vaatii tietyn minimisaannon eli virheprosentille on asetettu raja joko AQL tai LTPD-muodossa. Liittyy siis erien hyväksymistarkastukseen.
- Huonon laadun (virheellisten tuotteiden) määrälle on asetettu katto tai maksimi. Six Sigma -vaatimus <3,4 ppm.
- Laadun hävikkikustannus tai materiaalihävikki on saatettava tietyn tason alapuolelle esimerkiksi erilaiset ympäristöpäästöt
- Toleranssisuunnittelusta tulevat erilaiset vaatimukset
- Valitaan sopiva asetustapa suunnitelmakuvausten A-H avulla
Perusteita suunnitelman valintaan löytyy lukuisia. Oleellista on, että organisaatio tekee valinnan omien liiketoiminta ja prosessikohtaisten painotusten perusteella.
Esimerkkejä:
1. Organisaation on määritettävä, kuinka kaukana nominaaliarvoa (toleranssin keskiarvo T) prosessin keskiarvon on oltava pahimmassa tapauksessa mitattuna sigmoissa. Jotta näin voidaan toimia, on oltava ”jokin” tieto prosessin sigmasta. Parhaiten tämä tapahtuu SPC -kortilla esim Minitabin assistat I-MR -kortilla. Kuva 4. Samalla tilastollisella työkalulla voi selvittää myös prosessin stabiilisuuden.
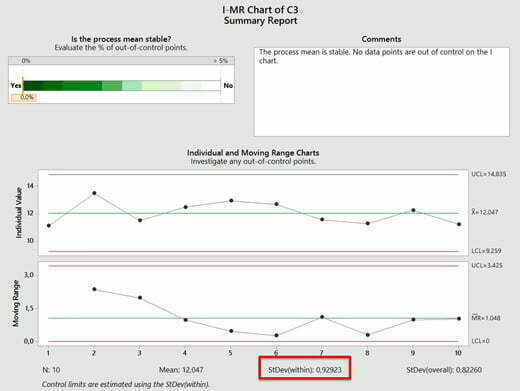
Prosessin sigman ja suorituskyvyn määrittelyyn on kuitenkin lukuisia muitakin menetelmiä. Huom. minimissä tarvitset vain 2-10 mittausta, mutta suositellaan 25-100 kpl estimointivirheen rajaamiseksi!
Toinen mahdollisuus on käyttää Minitabin suorituskyky (capability) analyysiä. Kuva 4. Oletetaan, että toleranssit on 7 ja 13 ja tavoite 10 ja mitattuja tuotteita 10 kappaletta.
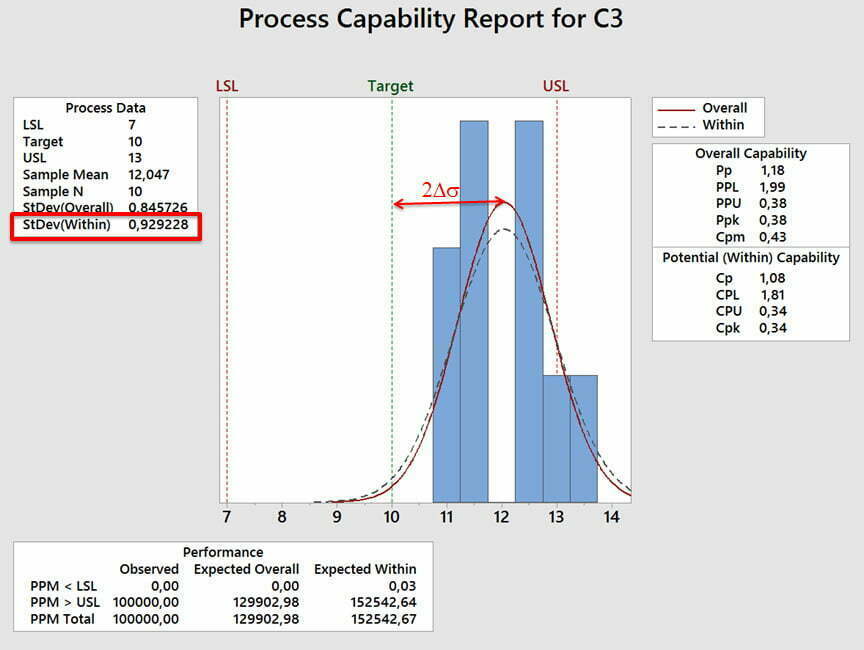
Kuvaan on merkitty sigma, joka on tietysti sama kuin I-MR -kortissa. Kuvaan on merkitty 2Δσ=(12,047-10)=2,05=2,05/0,929 *σ=2,2σ, joka tässä oletetaan maksimi sallituksi poikkeamaksi nominaaliarvosta. Tällä asetuksella syntyy maksimissaan 15 % viallisia tuotteita (expect within 152542 ppm =15,2 %). Kriittinen delta-sigma Δσ on siis 2,2/2=1,1 σ eli säätö on suoritettava väliin 1,10*0,929=> 10±1,02.
Säätösuunnitelma on siis B. Otetaan kolme kappaletta ja lasketaan näiden mittausten keskiarvo. Jos arvo on suurempi tai pienempi kuin 8,98 tai suurempi kuin 11,02 suoritetaan säätö ja otetaan uudet mittaukset uusista osista. Näin jatketaan kunnes päästään päätösvälin sisään. Huom. tuotteet ei välttämättä ole hylättäviä, jos ovat toleranssien sisällä ja eivät rikkoudu mittauksessa.
2. Jos prosessin keskiarvolle ei ole annettu erityistä toleranssia, mutta sen sijaan on vaadittu suorituskykyvaatimus Cpk tai Ppk, jotka itse asiassa spesifioivat toleranssivälin suhteessa sigmaan vähennettynä keskiarvon poikkeaman nominaaliarvosta jaettuna 3:lla Cpk= Cp – (T-xav)/3σ tai Ppk=Pp – (T-xav)/3σL Yhtälön jälkimmäinen osuus mittaa keskiarvo-poikkeamaa nominaalista, siis vaatimusta. Cpk ja Ppk -kaavat poikkeavat toisistaan vain sigman osalta. C:ssä sigma on ”within” ja P:ssä ”overall”. 2Δσ =3*(Cp-Cpk) tai 2Δσ =3*(Pp-Ppk). Saat siis edellä olevan laskettua myös (1,08-0,34)*3=2,22 eli keskiarvo poikkeaa 2,2 sigmaa. Jos vaadittu Cpk tai Ppk on paljon pienempi kuin Cp tai Pp, voidaan keskiarvon säätäminen tehdä suurempaan väliin ja näin pienemmällä näytemäärällä.
3-6. Jos asiakas vaatii tietyn minimisaannon esim. 95 % ja prosessissa on kyvykkyyttä tähän, voi käyttää Wheelerin käyrästöä, jossa x-akseli on keskiarvon maksimi poikkeama nominaalista ja y-akseli virheprosentti. Käyrästössä on esitetty virheet sigmatoleransseina eli kuinka monta sigmaa on toleranssiväli T+-T-. Jaat siis toleranssivälin sigmoina. Esimerkissä toleranssiväli on 6 ja sigma 0,929. Toleranssiväli on siis 6/0,929*σ=6,45σ Taulukkoon on merkitty myös vako Cp-käyrät.

Jos käytetään esimerkin tapauksessa B suunnitelmaa eli 2Δσ=2,2, siitä seuraa 15 % viallisia (nonconformance product).
95% tasoon päästään, jos 2Δσ=1,5σ Taulukon perusteella suunnitelma on C eli n=5 ja päätösväli Δσ = 0,75σ. Kuten nähdään, on pitkälti tuotanto tai laatuorganisaation vastuulla, kuinka paljon virheellisiä tuotteita tulee, jos prosessin suorituskyky kriittinen. Jos sen sijaa suorituskyky eli toleranssiväli >10 σ(Cp>10/6=1,66 – Cp= 12/6=2 ) eli Six Sigma -taso, lähes aina säätö voidaan tehdä yhden kappaleen mittauksen perusteella. Tuotanto tehostuu merkittävästi ja virheet häviävät!
7. Asetussuunnitelman voi tietysti valita myös vertailemalla eri suunnitelmien antamia piirteitä:
A. Jos prosessin keskiarvon on oltava välillä nominaaliarvo ± 2,88σ käytetään n=1 ja Δσ=1,44σ. Näillä arvoilla prosessin keskiarvo on 70 % ajasta välillä nominaali ± 1,44σ ja 27 % ajasta välillä nominaali ±(1,44σ-2,88σ). Tämä säätö on lähellä tyypillistä asentajan tekemää säätöä.
Millaisia tuloksia voi säädön seurauksena olettaa syntyvän? Käyrästöstä on määritettävissä maksimivirhemäärä, joka näin syntyy. Jos tiedetään prosessin suorituskyky. Tyypillisen suomalaisen yrityksen Cp on 0,67 => 4σ, joka ei sovi käyrästöön!
Käyrästöstä havaitset, että A-suunnitelma sopii tilanteissa, joissa prosessin suorituskyky on Cp> 1,67 (>10σ). Tässä tapauksessa virheellisten määrä pahimmassa tilanteessa on pienempi kuin 2 %. Jos Cp=1 (6s), virhemäärä pahimmassa tapauksessa on > 40 %.

B. Jos prosessin keskiarvo on oltava välillä nominaali ±2σ, käytetään B-suunnitelmaa, jossa n=3 ja kriittinen päätösväli Δσ=1σ. Tämän säädön tuloksena prosessin keskiarvo on 1 sigman sisällä nominaaliarvosta 80 % ajasta ja kahden sigman sisällä nominaalista 99 % ajasta. Tarkastellaan käyrästöllä prosessin kyvykkyyksiä Cp=0,67 => 4σ, Cp=1 => 6σ ja Six Sigma Cp=2=>12σ ja pahimman tapauksen virhemääriä. Cp=0,67 >50 % , Cp=1 15 % ja Cp=2 <0,5 %.
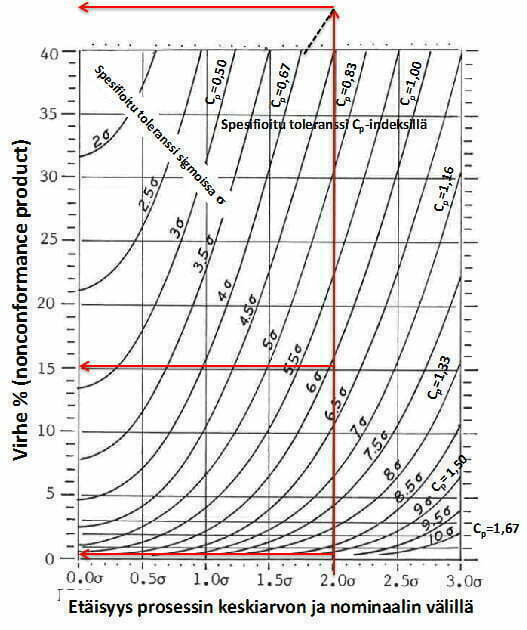
C. Jos prosessin keskiarvo on oltava välillä nominaali ±1,5σ, käytetään C-suunnitelmaa, jossa n=5 ja kriittinen päätösväli Δσ=0,75σ. Tämän säädön tuloksena prosessin keskiarvo on 0,75 sigman sisällä nominaaliarvosta 80 % ajasta ja kahden sigman sisällä nominaalista 99 % ajasta. Tarkastellaan käyrästöllä samoja prosessin kyvykkyyksiä Cp=0,67 => 4σ, Cp=1 => 6σ ja Six Sigma Cp=2=>12σ ja pahimman tapauksen virhemääriä. Cp=0,67 30 % , Cp=1 6,5 % ja Cp=2 <0,5 %.
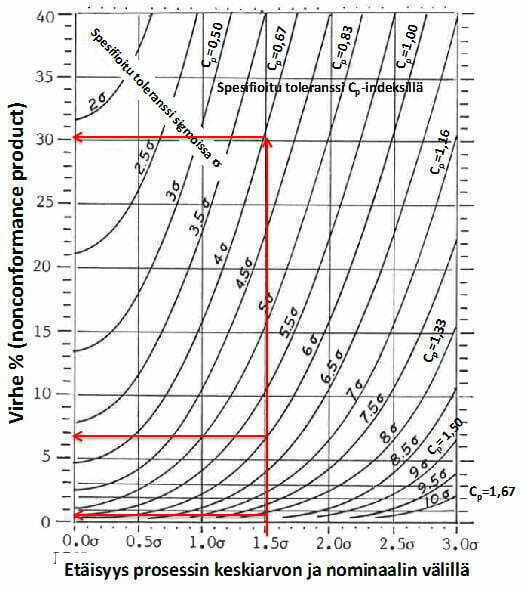
D-H. Samalla tavalla voidaan perustella käyrästön avulla muutkin suunnitelmat. Jos haluat taata stabiilin prosessin maksimi pahimman tapauksen virhemäärän, valitse pystyakselilta virheprosentti (non-conformance product) ja piirrä vaakasuora viiva kohtaan, joka kuvaa sigmoissa prosessisi kyvykkyyttä tai Cp:tä ja piirrä tästä alaspäin viiva ja lue asteikon arvo ja jaa tämä arvo kahdella, saat kriittisen päätösvälin Δσ. Etsi taulukosta lähin sopiva suunnitelma ja sen näytemäärä n.
Prosessin asettaminen Minitab Assistantin avustuksella
Jos yrityksellä ja operaattorilla on käytössä Minitab/8/, sen avulla prosessin asettaminen käy helposti käyttämällä 1-sample t-testiä.
- Aseta prosessi alustavasti nominaali eli tuotetavoitearvoon
- Kerää data (3-20) seuraavien ohjeiden mukaan
Kerää satunnaisotannalla data.
Jokainen data, jonka vedät, on yksittäinen mittaus, kuten läpimenoaika lainahakemuksessa. Kerää satunnaisotos kohteista, jotka edustavat prosessia. Esimerkiksi, jos sinulla on useita konttoreita mukana prosessin sovelluksissa, sinun ei pitäisi kerätä tietoja vain yhdestä konttorista tehdessäsi päätöksiä kaikista konttoreista.
Kerää tarpeeksi tietoa.
Näytteen tulisi olla tarpeeksi suuri määrittääksesi kohtuullisen varmasti, onko prosessin keskiarvo ja tavoitearvo huomattavasti erilaisia. Minitab määrittää, kuinka suuren eron keskiarvon ja tavoitteen välillä voit havaita näytteestä. Lisäksi, jos annat eron, joka on käytännön kannalta merkittävä omassa prosessissasi, Minitab määrittää mahdollisuuden, jolla voit todella tunnistaa tämän eron.
Syötä tiedot siinä järjestyksessä, jossa ne keräät.
Minitab piirtää tiedot samassa järjestyksessä kuin syötät ne laskentataulukkoon. Jos syötät datan siinä järjestyksessä, jossa keräät ne, voit helposti tarkistaa käyrästä trendejä ja muita kuvioita.
Prosessi pitäisi olla stabiili, kun keräät datoja.
Jos prosessi ei ole stabiili, voit ehkä havaita trendejä tai epätavallinen mittauksia, jotka voivat vaikuttaa näytteendataan ja voit saada testitulokset, jotka ovat harhaanjohtavia.
Datan ei tarvitse olla normaalisti jakautuneita kun otoskoko on vähintään 20.
Vaikka testi perustuu olettamukseen, että data on normaalisti jakautunut, tämä oletus ei ole kriittinen, kun näytteen koko on vähintään 20. Jos otoskoko on alle 20, ja data ei ole normaalijakautunut, p-arvo voi olla epätarkka, ja sinun pitäisi tulkita tuloksia varovaisesti.
Tutki epätavallinen datapisteet
Koska epätavallisilla datapisteillä voi olla suuri vaikutus tuloksiin, Minitab tunnistaa nämä kohdat sinulle. Sinun pitäisi yrittää selvittää syy näille epätavallisille pisteille ja korjata mittaus- tai syöttö virheet. Harkitse niiden datojen poistamista, jotka liittyvät erityissyihin ja tee analyysi uudelleen.
3. Syötä Minitab-assistantin lomakkeelle nominaali (tuotetavoite) ja prosessin keskiarvon maksimipoikkeama
4. Minitab analysoi, onko prosessin keskiaron luottamusvälissä ja mikä on luottamusväli 2Δσ. Minitab ilmoittaa molemmat liukupalkilla.
Pakkausprosessi
Esimerkki pakkausprosessista, jossa pakkauksen, muropaketin painon keskiarvo, prosessin keskiarvo, ei saa poiketa 365 g:sta kuin ± 2,5 g.
Prosessista kerätä 6 pakkausta, joiden paino punnitaan ja painot viedään Minitab -sarakkeeseen ja avataan Minitab Assistant 1-sample T-test. Kerrotaan sarake, jossa data on ”BoxWeight”, Nominaati, Target 365, Is the Box Weight mean different from 365, alfa 0,05 ja keskiarvon ero tavoitteesta 2,5 g.
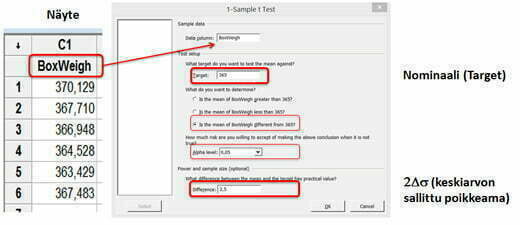
Tämän jälkeen Minitab kertoo, onko eroa olemassa tilastollisesti prosessin keskiarvon välillä ja kuinka paljon maksimissa ja kuinka paljon dataa olisi kerättävä.
Siis painamme ok.

Johtopäätös: keräämme uuden datan, jossa n=10-12. Tässä tapauksessa 12 kpl ja saamme analyysin Minitab Assistantilta.

Johtopäätös esimerkistä. Prosessin keskiarvoa on säädettävä alaspäin, jotta prosessin tavoite on asetetulla etäisyydellä nominaalista eli tuotetavoitteesta.
Huom! Jos tämä säätö olisi suoritettu asetustaulukon 1 mukaan, suunnitelmaksi olisi valittu D (2Δσ =2,5/2,4*s=1,04s) ja kriittinen etäisyys 1,25 g eli 354,75 – 366,25. Toisessa testissä, jossa oli 12 kpl, keskiarvo oli 366,64 g eli prosessia on säädettävä alaspäin kuten myös Minitabin Assistant ilmaisee.
Yhteenveto
Keskiarvon säätäminen oikein on keskeistä asetettaessa niin palvelu kuin tuoteprosesseja, niissä olevia linjoja, koneita ja jopa erilaisia menettelyjä.
Menettelyn valintaa ei kuitenkaan pitäisi jättää työntekijän/operaattorin vastuulle ja huoleksi. Asetusmenettely on mitä suurimassa määrin tuotanto/laatu-organisaation vastuulle. Valitaan sitten Gruppsin sääntö tai tilastollinen menettely (jota suosittelen), oleellista on, että valinta on perustuu syvälliseen harkintaan.
Silloin kun säätö voidaan toteuttaa yhdellä muuttujalla, säätimellä, on tiedettävä kuinka monta näytettä on otettava ja lasketusta keskiarvosta päätellä kriittisen arvon Δσ avulla, onko säätö suoritettava vai ei. Jos säädön suorittaa pienemmästä arvosta kuin taulukko osoittaa, seuraa turhaa työtä ja lisää vaihtelua. Taulukkoon on merkitty asetussuunnitelman ja prosessin suorituskyvyn Cp pahimman tapauksen virheprosentit (nonconformance product).

Punaisella merkityt yhdistelmät sisältävät merkittävän riskin tuottaa viallisia osia tai tuotteita. Riskin todennäköisyys ilmenee suunnitelmataulukosta. Keltaiset suunnitelmat ovat rajasuunnitelmia ja vihreät suunnitelmayhdistelmät sisältävät vähäisen riskin ja näin suositeltavia.
Mitä huonompi/pienempi on prosessin suorituskyky Cp , sitä vaativampaa on prosessin keskiarvon säätäminen. Tarvitaan suurempia näytemääriä, laskentaa ja työtä ja aikaa, jotta päästään erinomaiseen laatuun.
Prosessin suorituskyvyn nostaminen kannattaa aina. Vältytään monimutkaisilta ja pitkiltä asetusmenettelyiltä ja säätö on mahdollista toteuttaa jopa yhdellä kappaleella.
Lähteet:
- Frank E. Grubbs: ”An OptimumProsedure for Setting Machines or Adjusting Processes; Journal of Quality Technology,1954, 1983
- Donald J.Wheeler, Davis S. Chambers: Understanding Statistical Process Control, SPC Press, 1986
- Eero E. Karjalainen ”Unohdettu laadunohjaus”, 2016, Artikkeli
- Antti Piirainen: ”Tilastollinen prosessinohjaus vaihtelun tunnistamisessa”, 2014, Artikkeli
- Antti Piirainen: ”Laatu puhuttaa Suomessa”, 2013, Artikkeli
- Eero Karjalainen: ”Kuinka hallitsen tuotanto ja palveluprosesseja – ohjaanko toleranssirajoilla vai SPC.rajoilla”, 2013, Artikkeli
- Antti Piirainen: Mitä pitäisi ymmärtää datasta – tilastosta? Osat I-IV, 2009, Artikkeli
- Minitab 18
Lue koko artikkelisarja:
Tilaa uutiskirje
Liity postituslistalle ja saat uusimmat artikkelit suoraan sähköpostiisi.
Tämä lomake on suojattu Google reCAPTCHA:lla. Lue tietosuojaseloste ja käyttöehdot.
Liittymällä postituslistalle hyväksyt Quality Knowhow Karjalainen Oy:n tietosuojaselosteen ja Quality Knowhow Karjalainen Oy voi lähettää sinulle ajankohtaisia artikkeleita, videoita sekä tietoa ja tarjouksia kursseista, kirjoista sekä ohjelmistoista.
Tämä lomake on suojattu Google reCAPTCHA:lla. Lue tietosuojaseloste ja käyttöehdot.