Tuottavuuden parantaminen on kaikkien huulilla, etenkin näin alhaisen ja laskevan kysynnän aikana. Lääkkeeksi tarjotaan leikkauksia, säästöjä. Toinen suunta ja samalla mielenkiintoinen eli tuotoksen kasvattaminen jää vähemmälle huomiolle. Tuottavuudesta on tullut liki synonyymi säästämiselle. Tuottavuuden parantaminen ei ole säästämistä, vaan tuotoksien ja panoksien suhteen parantamista/1/.

Tuotoksen lisää (kasvua) voi hakea joko…
- kehittämällä uusia tuotteita, joista asiakas on valmis maksamaan enemmän kuin nykyisistä tuotteista ja huomioiden samalla, että tuotteen tai palvelun toteuttamisen tehokkuus pysyy samana tai ei ainakaan laske tai
- kasvattamalla tuotoksen määrää, joka saadaan aikaan samoilla resursseilla. Eli ei hankita lisää varastoja, henkilökuntaa, koneita tms.
Tässä kirjoituksessa keskitytään jälkimmäiseen vaihtoehtoon. Tämän voi toteuttaa useilla eri keinoilla, mutta nyt keskitytään aikaan. Aikaan, joka kuluu tuotteen tai palvelun toteuttamiseen. Tällä ajalla ei tarkoiteta jaksoaikaa eikä läpimenoaikaa, jotka kuvaavat aikaa, joka kuluu tuotteen tai palvelun kulkemiseen prosessin läpi.
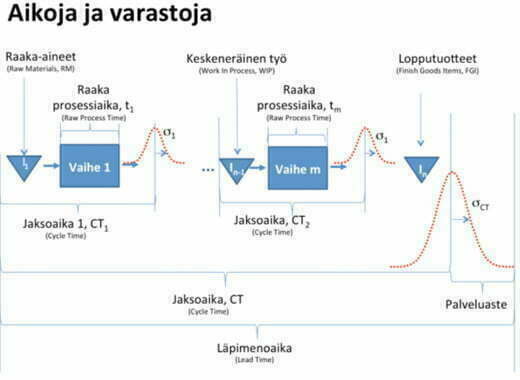
Aika on äärimmäisen mielenkiintoinen ja vaikeasti käsiteltävä asia. Aika kuluu ja sitä tulee lisää koko ajan. Sen käsittely, määrittely ja sen vaikutuksen ymmärtäminen eri asianyhteyksissä on yksi osa tuottavuuden kehittämistä. Erilaisten menetelmien yhteydessä se usein yksinkertaistetaan. Tämä trivialisoi ajatuksen seuraavasti: aina ajan lyhentäminen on tärkeää ja oikea suunta, joka automaattisesti tuo parannusta ja tuottavuuden kasvua. Jossain tilanteissa ajan pidentäminen voi olla keino kasvattaa tuottavuutta. Ajan kuluminen on seuraus, se ei ole syy. Jotain täytyy muuttua, jotta aika lyhenee, sitä ei voi lyhentää.
Jatkuvasti kuulee, että läpimenoaikoja, jaksoaikoja, tulee lyhentää tuottavuuden parantamiseksi. Tämä on väärin! Jos tehdään oikeansuuntaisia toimenpiteitä, jaksoaika lyhenee ja läpimenoaikaa voidaan lyhentää ilman tuottavuuden laskua tai lisäämällä resursseja. On muistettava, että läpimenoaikaa ei lyhennetä liikaa, muuten menetetään tuottavuuden kasvattamispotentiaalia. Tästä tuonnempana lisää. Seuraavana käsitellään asian selventämiseksi tuotteen tai palvelun valmistamista, laadun ja ajan välisiä yhteyttä.
Organisaatiot ovat olemassa siksi, että ne tuottavat asiakkaille joko tuotteita tai palveluita. Ominaispiirre tarkoittaa tuotteessa tai palvelussa olevaa ominaisuutta, josta asiakas on valmis maksamaan ja se on yritykselle kilpailutekijä./2/
Aikaa, joka kuluu ominaispiirteen tuottamisen, kutsutaan teholliseksi ajaksi (te). Tämä aika pitää sisällään erinäiset häiriöt, jotka ovat luonnollinen osa tuotantoa (myös palvelutuotantoa). Tehollinen aika on mielenkiintoinen, koska siinä yhdistyy asiakkaan tarpeen tyydyttäminen ja tuottamiseen kuluvat resurssit. Jos tämä aika on lyhyt, valmistusnopeus kasvaa tai päinvastoin (HUOM! tämä ei ole jakso- eikä läpimenoaika). Keskimääräinen valmistusnopeus (TH, throughput) on kääntäen verrannollinen ominaispiirteen tuottamiseen kuluvasta ajasta (TH=1/te).
Ajatellaan, että kokoat legoautoja. Ominaispiirre on esimerkiksi suunnitelman mukainen valmis auto. Ideaalitilassa legoauton kokoamiseen menee 60-80 sekuntia. Jos kokoamiseen kohdistuu häiriöitä ja aika kasvaa 115-205 sekuntiin, laskee keskimääräinen valmistumisnopeus 1/70 kpl/s ->1/160 kpl/s. Käytännössä tarvitaan kolminkertaiset resurssit tuottamaan asiakastarve.
Äärimmäisen harvoin, tuskin koskaan, työtä voidaan suorittaa häiriöttä. Kun työn suorittamiseen kohdistuu mikä tahansa häiriö, joka voi olla joko haluttu (suunniteltu huolto, koulutus, kokous, loma, tms.), ei-haluttu, mutta välttämätön (vaihto, Setup, vuoron vaihto, koulutus, kokous, tms.) tai ei-haluttu (laatuvika, konerikko, tietokoneen kaatumien, sairauspoissaolo, väärä lähtötieto tms.), pidentää tämä ominaispiirteen muodostumiseen käyttävää aikaa. Tätä aikaahan kutsutaan teholliseksi ajaksi (te), ja näin ollen se asettuu tuottavuuden kehityksen keskiöön.
Olen kirjoittanut kirjan Vaihtelu/3/, missä käsitellään vaihtelun vaikutusta tuottavuuteen. Itse asiassa hyvin useat asiat kiteytyvät juuri tähän teholliseen aikaan. Juuri tämän ajan muodostuminen ja hallitseminen on tärkeä osa tuottavuuden kehittämisessä, onpa kyseessä uuden tuotteen(palvelun) suunnittelu tai olemassa olevan tuotteen (palvelun) tuottavuuden parantaminen. Tehollisen ajan pituus ja vaihtelu vaikuttaa jonojen muodostumiseen ja niiden pituuden vaihteluun eri ajan hetkillä. Kingman esitti yhtälön vuonna 1961, joka auttaa luomaan ymmärrystä tähän ongelmaan. Jos tehollinen aika ja sen vaihtelu (Ce2) pienenee jonot lyhenevät (WIP laskee) ja jaksoaika lyhenee. Kingmanin yhtälö sitoo yhteen virtauksen suuntaisen ajan sekä ominaispiirteen muodostumisen ajan (kuva 3). Asiasta tarkemmin kirjoituksessa: Aikavaihtelu, 1.4.2014.

Aika tekijänä (muuttujana) on hankala, koska se tuntuu tutulta, mutta se on kuitenkin abstrakti. Usein se on vain numero. Mitä lyhyempi aika, sitä hankalampi on ymmärtää ajassa tapahtuvan muutoksen (poikkeaman, vaihtelun) vaikutus tuottavuuteen. Olen kehittänyt demonstraation, jonka avulla havainnollista häiriöiden vaikutusta tuottavuuteen. Tulokset usein demon ja sähläämisen jälkeen yllättävät.
Demonstraatiossa kootaan legoautoja osista, jossa on pieni määrä vikoja. Nämä vialliset osat estävät osien kiinnittymisen toisiinsa ja synnyttävät häiriön ”tuotantoon”. Vialliset komponentit edustavat mitä tahansa häiriötä onpa kyseessä sitten palvelu tai tuotteen toteuttaminen.
Häiriöiden määrä ei ole suuri per komponentti (muuttuja), mutta legoauto on kokonaisuus (systeemi) eikä vain kasa osia. Tästä seuraa, että ei ole ihan sama missä järjestykset osat ovat ja kuinka ne asetetaan suhteessa toisiinsa sekä onnistuuko osien kiinnittäminen. Jos osat ovat kunnossa, osat sopivat ja osien välinen keskinäisvaikutus ei hidasta kokoonpanoa eli työtä. Jos taas osassa on vika, keskinäisvaikutus osien välillä alkaa häiritä työn tekemistä, synnyttää joko korjaamisen tarpeen tai pysäyttää tekemisen. Keskinäisvaikutukset siis jarruttavat hidastavat ja aiheuttavat tehollisen ajan kasvamisen. Tämä vastaavasti aiheuttaa resurssitarpeen kasvamisen sekä muodostaa tarpeen kasvattaa keskeneräisen työn määrää, kapasiteetin tarvetta sekä pidentää jaksoaikaa ja läpimenoaikaa.
Kuvassa 4 on esitetty kahden eri kierroksen tulos. Kierroksella 1 ei ole häiriöitä (tilanne joka usein koulutuksissa esitellään, Lean-muutos ideaalitilassa) ja kierroksella 2 on häiriöitä (normaali tilanne organisaatioissa). Ohjauskortista (kuva 5) nähdään häiriöiden vaikutus teholliseen aikaan (pelidataa). Kuvan 3 taulukosta nähdään kuinka häiriöt vaikuttaa jaksoaikaan (CT) sekä läpimenoon (TH, throughput).


Vaihtelun pienentäminen eli laadun parantaminen, toisin sanoin onnistumistodennäköisyyden kasvattaminen, on tuottavuuden parantamisen keskiössä. W.E. Deming esittää tämän ketjureaktio vuosikymmeniä sitten kirjassaan Out of The Crisis/4/. Ei varmaan ole sattumaa, että Toyotalla laatu on numero yksi/5/, tämän jälkeen tulee aika, jonka jälkeen riippumaton virtaus (vrt Rotherin esittämä Lean-visio, kirjassa Toyota KATA). Nämä ovat elementtejä, jotka takaavat työtä ja taas työtä sekä hyvinvointia.
”The most important thing we learned was that quality in those companies means something different from what it means in the U.S. – that it is in fact a totally different discipline. Over the years, Japanese managers, engineers, and workers have been very successful in reducing manufacturing costs by adopting more enlightened quality thinking and by applying more technical quality methods. In other words, quality in itself has not been the primary motivation in Japan; profit is the main objective and quality (methods) is merely a means to improve profit…Of foremost importance is the new definition of ’manufacturing’ quality as minimum variation from target./6/
Olen pitänyt aiheesta yli tuhat luentoa ja puhunut yli 10 000 tuntia. Saman aikaisesti asiakkaani ovat saaneet merkittäviä tuloksia parantamalla toiminnan ja tuotteiden sekä palveluiden laatua. Vaikka jatkuvasti seuraan eri lähestymistä tuottavuuden parantamiseen, niin vakuutun edelleen laadun, eli vaihtelun hallinnan ja pienentämisen tärkeydestä. Kun laatua parannetaan ja tehollista aikaa lyhennetään, jaksoaika lyhenee ja tulee ennustettavammaksi. Tämä mahdollistaa läpimenoajan lyhentämisen joissain tapauksissa, eikä päinvastoin.
Lähteet:
- Zandin, K. B. 2001. Maynard’s Industrial Engineering Handbook, Fifth Edition. McGraw-Hill. USA.
- Taguchi, G., Chowdhury, S. & Wu, Y. 2005. Taguchi´s Quality Engineering Handbook. Wiley
- Antti Piirainen: Vaihtelu, 2014, Quality Knowhow Karjalainen Oy
- Deming, W. E. 1982. Out of the Crisis. Massachusetts Institute of Technology Central for Advanced Engineering Study. Cambridge. USA.
- Rother, M. 2010. Toyota Kata – Managing People for Improvement, Adaptiveness and Superior Results
- Bellows, B. Reflections on the fabric of the Toyota Production System. Lean Management Journal www.leanmj.com
Tilaa uutiskirje
Liity postituslistalle ja saat uusimmat artikkelit suoraan sähköpostiisi.
Tämä lomake on suojattu Google reCAPTCHA:lla. Lue tietosuojaseloste ja käyttöehdot.
Liittymällä postituslistalle hyväksyt Quality Knowhow Karjalainen Oy:n tietosuojaselosteen ja Quality Knowhow Karjalainen Oy voi lähettää sinulle ajankohtaisia artikkeleita, videoita sekä tietoa ja tarjouksia kursseista, kirjoista sekä ohjelmistoista.
Tämä lomake on suojattu Google reCAPTCHA:lla. Lue tietosuojaseloste ja käyttöehdot.