Laatutaulu: kehitysvaiheet III-VI – teoriasta käytäntöön
Tässä osassa jatketaan uudempaan laatutaulun kehitysjaksoon vuosina 1987-2017, jossa käyn läpi viiden yrityksen laatutaulutietä. Näissä viidessä ”caseissa” korostuvat taulujen laajempi käyttö hallintoprosesseihin, tilastolliset rajat, käytettävyys, hienosäätö ja siirtymistä selainpohjaisiin ohjelmistoihin. Edellisissä osissa 1 ja 2 käsittelin laatutaulun ”virheiden ja hukkien laatuteoriaa” ja ”taulun historiaa” kahden yrityksen, FinnValco Oy ja Kemppi Oy, osalta vuosina 1976-1986.
Laatutaulu on keskeinen ennaltaehkäisyn ja parantamisen työkalu, joka pohjautuu tilastolliseen prosessinohjaukseen (SPC, Statistical Process Control (4)). Laatutaulu sopii tapauksiin, joissa prosessista ei saada suoraa mitattua dataa. Tyypillisiä prosesseja ovat tuotanto-, kokoonpano- ja asennuslinjat, palveluprosessit, yritysten hallintoprosessit kuten markkinointi, myynti, laskutus, hankinta, lähetys jne. Epäsuora tilastollinen data saadaan henkilöstön havaitsemista ja luokittelemista poikkeamien – virheiden, vikojen ja hukkien – esiintymisdatasta, joka stabiilissa tilanteessa noudattaa Poisson-jakaumaa. (Katso artikkeli: Laatutaulu: virheet ja hukka). Poisson-jakauma muodostaa vertailukohdan (ohjausrajat, C-raja), mikä mahdollistaa prosessin ennaltaehkäisyn ja parantamisen.
Mikä on laatutaulu:
Laatutaulu on julkinen isokokoinen taulupari, johon on koottuna valmistusprosessin aikana päivittäin, viikoittain tai kuukausittain havaitut luokitellut poikkeamat. Poikkeamat analysoidaan, diagnostisoidaan ja jaetaan tilastollisesti ohjausrajojen (C-raja) avulla erityissyihin ja satunnaissyihin. Erityissyyperusteisten poikkeamien (ilmenemismuotojen) juurisyyt selvitetään vastuuhenkilön toimesta erityissyytaululla ja tehdään korjaus, ohjaus tai parannustoimenpide. Toimenpide merkitään taululle ja valmistumishetki. Kaikki tämä julkisesti kaikkien koko henkilöstön nähden.
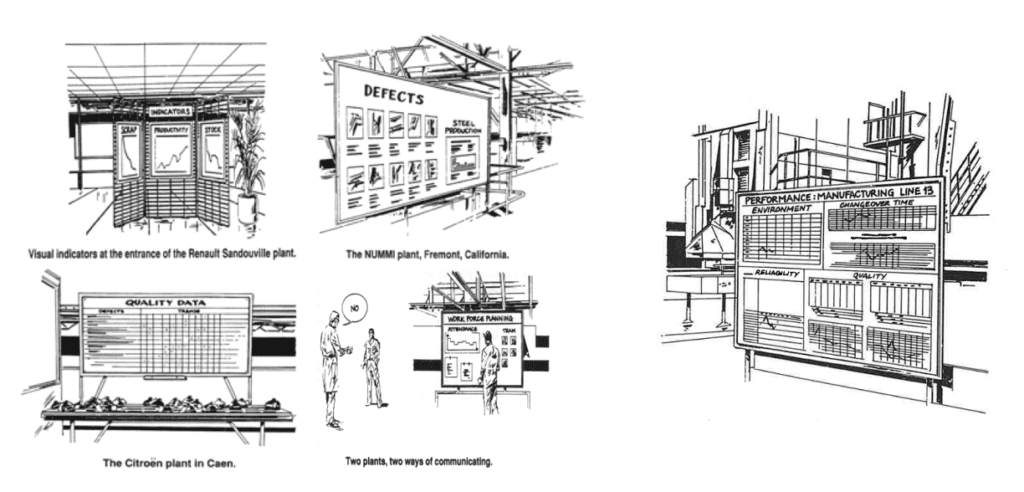
Keskeinen ajatukseni laatutauluista oli tehostaa entisestään yrityksen tuotannon ja hallinnon laaduntuottokykyä ja parantaa tilastollista stabiilisuutta ja erityissyiden poistamista ja reagoida käytännön laatu- ja organisaatiohukkiin.
Valmistuksen laadun rinnalle tuli 1990-luvulla toiminnan laatu -käsite, joka koski markkinointia, myyntiä, hankintaa ja muuta hallintoa. Yllätys oli, että hallinnossa on ”näkymättömiä” virheitä paljon, paljon enemmän kuin tuotannossa ja niitä myös siedetään ja korjaillaan paljon. Yrityksissä ei yleensä ole mitään järjestelmää toiminnan prosessien virheiden keräämiseen ja hallintaan. Ihmetellään vain, miksi talousluvut, tuotantoluvut ja saldot jne. eivät ”täsmää” tai antavat virheellisen kuvan yrityksen tilasta. Vastasin tähän haasteeseen uusilla laatutaulusovellutuksilla.
Vähämerkityksellisyyttä ei myöskään ollut 1980-luvulla laatuyhteisöön levinnyt Armand Vall Feigenbaumin kehittämä TQM-malli (Total Quality Management (6)), jossa koko henkilöstö hallintoa myöten pyritään ottamaan mukaan laatuvastuuseen ja laadun tekemiseen. Puhutaan isosta Q:sta. TQM:n vastakohta oli ollut tuotantoa valvova, tuotannosta riippumaton, itsenäinen, itsetietoinen ja ”kapea” laatunäkemys, pieni q (quality).
Kerroin osassa 2, kuinka yritysjohdolle suunnatuista laaturaporteista muodostui jo FinnValcolla työntekijöitä informoiva prosessitaulu. Varsinainen laatutaulu ja siihen liittyvä organisointi ja vastuut muodostuivat Kempillä 1981-1986. Taululla ohjattiin toimintaa. Nämä ”käskyt” ja säännöt kirjoitettiin Kempin laatupolitiikkaan ja niiden soveltamisohjeisiin.
Laatuteoria, käytäntö ja kokemukset on koottu myös kirjaamme Laatutaulu – Tehokas menetelmä laadunohjauksen ja parantamiseen, 2024 (7). Laatutauluilla on voitettu Laatupalkinto vuosina 1986, 1990, 1991, 2000 (Kemppi Oy, 2 x Stala Oy, Salpausselän kirjapaino Oy). Laatutaulut ja eri versiot ovat käytössä sadoissa yrityksissä ympäri Suomea. Tauluista on tehty myös selainpohjaisia tietokoneversioita erityisesti niissä tapauksissa, joissa syntyy mitattua dataa (multi SPC).
Sisältö:
Johdanto
1. Laatutaulun historiasta
I. Kehitysvaihe 1976-1980 Valco/FinnValco Oy
II. Kehitysvaihe 1981-1986 Kemppi Oy
III. Kehitysvaihe 1986 – 2009 Stala Oy
IV. Kehitysvaihe 1990 – 1995 Halton Oy
V. Kehitysvaihe 1990 – 2004 Eimo Oy/Foxcon Oy ja Metsä Botnia Oy
VI. Kehitysvaihe 2010 – 2017 Lahden Autokori Oy/ SOE Busproduction Finland Oy (Scania)
2. Yhteenveto
Lähteet
Johdanto
Laatutaulu oli jo saanut merkittävää jalansijaa 1980-luvun loppupuolella eikä yksin siitä syystä, että Kemppi Oy oli saanut laatupalkinnon vuonna 1986 laatutaulujen ansiosta vaan myös siksi, että esittelin sitä useissa koulutustilaisuuksissa.
Suuri osa Kempillä pitämistäni lukuisista kursseista ja niiden sisällöistä siirtyi suoraan Laatuyhdistyksen kursseiksi, joita pidimme Pekka Salmisen kanssa. Kempin ”case” oli usean laadun ammattilaisen tiedossa. Myös ensimmäinen Laatutauluopas syntyi tällöin.
1. Laatutaulun historiasta 1986-
Seuraavat kehitysaskeleet otettiin yrityksissä:
- Kehitysvaihe 1986 – 2009 Stala Oy
- Kehitysvaihe 1990 – 1995 Halton Oy
- Kehitysvaihe 1990 – 2004 Eimo Oy/Foxcon Oy ja Metsä Botnia Oy
- Kehitysvaihe 2010 – 2017 Lahden Autokori Oy/ SOE Busproduction Finland Oy (Scania)
III. Kehitysvaihe 1986-1987 Stala Oy
Kolmas laatutaulujen kehitysvaihe käynnistyi, kun Kempin tyyppiset laatutaulut ja hyvät kokemukset otettiin käyttöön Stala Oy:ssä Lahdessa vuonna 1987. Vuoden 1986 lokakuussa perustimme DI Pekka Salmisen kanssa Suomen ensimmäisen laatuun keskittyvän koulutus- ja konsultointiyrityksen, Laatutieto Oy:n, jota QKK nyt jatkaa. Stala oli ensimmäisiä asiakkaitani.
Stala oli perheyritys, joka on perustettu 1972. Vuonna 2020 Stala yhdistyi Slovenialaisen Alvenus-konserniin säilyttäen Stala-brändin ja pesupöytätuotannon Lahdessa.
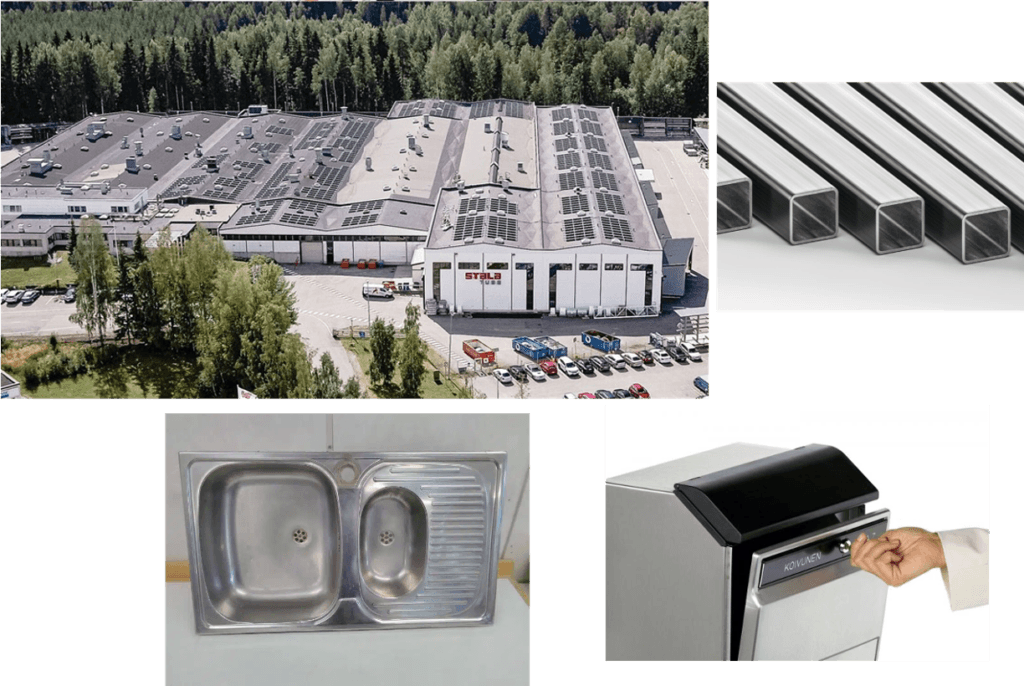
Stala Oy valmistaa pesupöytiä, ”tiskipöytä” ja postilaatikoita (Katso artikkeli: Asiakaslähtöinen tuotekehitys (QFD)) (8) sarjatuotantona. Tuotanto oli varastotuotantoa. Tuotteet lähetettiin varastosta edelleen asiakkaille. Malleja oli kymmeniä. Yritys valmisti myös laitoskalusteita, joissa käytettiin ruostumattomia putkia runkorakenteena. Tämä osavalmistus laajeni ja syntyi erillinen putkituotanto. Ruostumattomien putkien tuotanto eriytettiin erilliseksi yhtiöksi, Stalatube Oy:ksi vuonna 2000. Putkituotannossa oli laatutaulut samoin kuin pesupöytälinjalla. Tuotannon henkilömäärä pesupöydässä oli vuonna 1987 noin 40-50 henkilöä ja putkipuolella 3-4 linjaa ja työntekijöitä 10-20.
Toimin Stalassa laatukouluttajan ja konsultin roolissa vuodesta 1987 lähtien 25 vuotta. Vierailin yrityksessä 1-2 kk välein muun muassa laatujohtoryhmän tilaisuuksissa. Stalan laatupäällikkönä toimi Esko Vainio. Sain häneltä kaiken laatuun liittyvän datan ja hän toimeenpani laadun kehityshankkeet. Hänen kanssaan tehtiin myös ISO 9001 laatujärjestelmä 80-luvun lopussa. Suosittelen vastaavaa järjestelyä. Usein laatupäällikkö tai vastaava jää yksin pyörittämään ”sitä samaa” ilman teorian, käytännön ja koulutuksen antamaa pohjaa. Uusien laatu- ja tuottavuusideoiden tuominen talon sisältä on vaikeaa.
Kuvassa 3 keskeiset laadun kehittämisen hankkeet 1986 – 2006. Huomaa, kaikki alkoi laatutaulusta, SPC:stä, jolla luotiin stabiili perusta muiden laatutyökalujen käytölle. Sitten QFD:tä ja Taguchia jne. Katso ensimmäisen artikkelin kuva Laatu ja Lean talot (9).
Ensin stabiloidaan ja sitten kehitetään! Näitä hankkeita juhlistettiin talon tapaan 20-vuotisjuhlilla, johon Aimo Kokkola oli tehnyt ”Viisun”. Kuuntele kappale tästä.

Laatu oli Stalalla paljon muutakin kuin Laatutaulut, esim. vuonna 1996 käynnistynyt kasvun strategia, jonka seurauksena putkituotantoa kasvatettiin yli 400 % ja syntyi itsenäinen Stalatube Oy, jonka liikevaihto oli vuonna 2023 n. 100,3 miljoonaa euroa, mutta nyt laatutauluista. Monta koulutusta ja saarnaa monesta aiheesta tuli pidettyä!
a) Laatutaulu ja tilastollisuus
Laatutaulut tulivat Stalalle alkuvuodesta 1987. Toiminta oli samankaltaista kuin Kempillä. Tuotantolinja ja tuotteet olivat erilaisia. Kempin linjat olivat osavalmistusta ja kokoonpanolinjoja, kun taas pesupöydän valmistus on enemmän prosessimaista. Sopisiko laatutaulut tähän prosessiin? Yhtään laatumittaria ei ollut muuta kuin romulava ja asiakasreklamaatioita! Kuinka mitata laatu prosessin sisältä – onnistuminen tai epäonnistuminen? Vastaus: laatutaulut.
Kemppiin verrattuna tauluja kehitin edelleen tilastolliseen ja tehokkaampaan suuntaan ja erityisesti paransin niihin liittyvää koulutusta ja informointia. Yritin kertoa tarkemmin laatuteoriaa ja jakoa erityissyyperusteisiin virheisiin ja satunnaissyyperusteisiin virheisiin, miksi jako on äärimmäisen tärkeä ja kuinka parannus saadaan aikaan. Vaikeaa oli!
Miten voi sama virheen ilmenemismuoto olla samanaikaisesti erityissyyn ja satunnaissyyn aiheuttama? Eikö kaikki virheet pidä tutkia? Kysymyksiä ja epäilyjä oli enemmän kuin ehdin vastata. Yritin kertoa, jos jollakin tavalla. Käytin säätötekniikan kaavoja, demoja ja esimerkkejä. Käytin lääketieteen veriarvojen viitearvoja, diagnostiikkaa; jos yskit, yskän syy voi olla flunssa tai astma tai sydän, mutta yhä kaikki yskit. Jos ”parannat” flunssalääkkeellä sydänperäistä yskimistä, kuolet (ehkä) ja päinvastoin (ehkä). Flunssaan on erityissyyn, ulkopuolisen syyn aiheuttama, virus tai bakteeri (akuutti sairaus). Astma tai sydän on krooninen systeemivika. Mitä sitten, jos flunssaisella sydänvikaisella on yskä! Upposiko? Tiedä häntä. Laatu (ja Lean) ei ole eikä voi olla irrallinen muista ”opeista”, haluat tai et! Laadussa ei ole mitään erikoista. Akuutista ja kroonisesta sairaudenaiheuttajasta käytetään vain eri nimeä – erityissyyperäinen ja satunnaissyyperäinen poikkeama (virhe, vika, hukka).
Ensisijainen analyysityökalu Stalalla oli aluksi Pareto-kaavio ja tilastolliset analyysit (7 laatutyökalua, Seven Tools) (1987-89), jotka kuitenkaan eivät tuottaneet niin hyviä tuloksiakuin odotin. Nämä menetelmät olivat ns. laatupiirien (Quality Circle, https://en.wikipedia.org/wiki/Quality_circle ) (10) käyttämiä ja ”muodissa”. Japanilainen laatupiiri-innostus laantui 80-luvun lopulla. Miksi?
Syy on, että ei eroteltu erityissyyperäisiä ja satunnaissyyperäisiä poikkeamia toisistaan (virheitä, vikoja hukkaa). Pareto (Seven Tools) toimii erinomaisesti, jos erottelu on tehty ennen työkalujen käyttämistä. Yleisesti ottaen 7 laatumenetelmää saa käyttää vain erityissyihin eli juurisyyanalyysiin. Satunnaissyyssä ei ole juurisyytä. Toki 7 ongelmanratkaisun työkalussa on ohjauskortit (SPC). (Ps. Prof Hannu Niemi oli aikanaan myös nimennyt ohjauskortit (SPC) väärin ”valvontakorteiksi” SFS stan-dardiin 4360 (1981) (11). Mennyttä tässä ja nyt valvotaan ja tulevaisuutta ohjataan!)
Artikkelin lukuisat esimerkit osoittavat, kuinka vaihtelu, virheet ja hukat, alkavat kasvaa, jos et erottele ja sekoitat nämä kaksi syyryhmää toisiinsa.
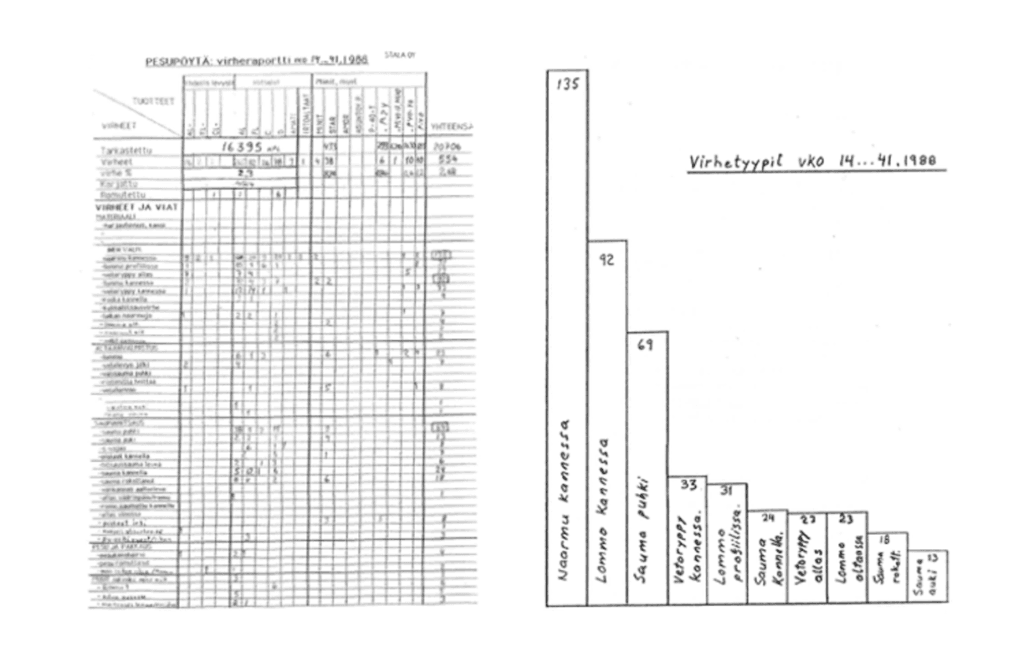
Kempillä laatutaulut olivat aluksi tuote-/linjakohtaisia. Stalalla ei ollut varsinaisia tuotelinjoja, vaan samalla linjalla tehtiin kaikkia eri malleja sarjoittain. Tuotekohtaista taulua ja analyysiä kokeiltiin Kempin tapaan (kuva 4), kunnes todettiin, että samalla linjalla tehtävät tuotteet eivät tarvitse erillisiä laatutauluja. Sama prosessi erilaisiin tuotteisiin synnyttää samanlaiset poikkeamat, virheet ja viat. Tämä samankaltaisuus näkyi esimerkiksi tuotteiden Pareto-analyyseistä. Tämä oivallus ja ”löytö” yksinkertaisti merkittävästi laatutauluja.
Vuosina 1987-89 laatutauluissa ei ollut merkittynä ohjausrajoja, mutta tulkinta ja käyttö oli kuitenkin rajojen mukaista SPC:tä. 1990-luvun alussa Stala Oy:llä otettiin käyttöön varsinainen SPC (C-ohjausrajat) ja niin sanottu erityissyytaulu (projektitaulu) laatutaulun rinnalle. Taulu oli sijoitettu keskelle tuotantotilaa työnjohtokoppia vastapäätä niin, että kaikki näkivät. Erityissyytauluun merkittiin kaikki ratkaistavat erityissyyongelmat. Samalla alettiin seurata tarkemmin takuu- ja reklamaatioiden määriä. Tähän asti reklamaatiot olivat ”yksittäistapauksia”, joita hoiti markkinointi. Kaiken lisäksi reklamaatiot ja valitukset olivat ”vanhoja”. Valmistus tapahtunut noin 1-3 vuotta ennen asiakasreklamaatiota.
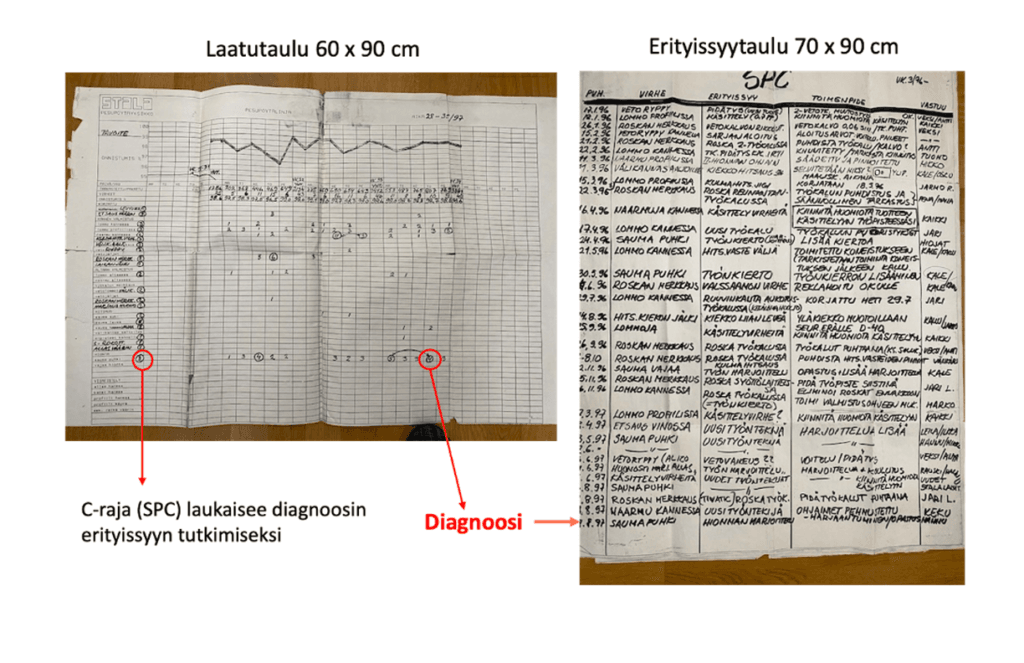
b) Tulokset Stalan laatutauluista
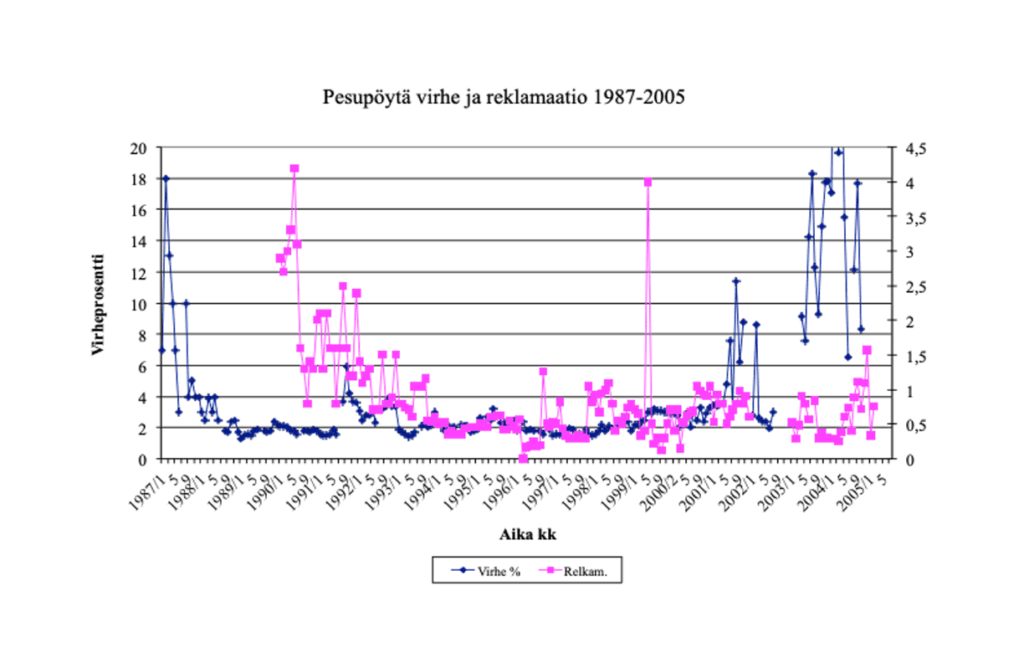
Toimenpiteet ja koulutus tehosi. Laatutaulu + erityissyytaulu toimivat mainiosti. Virheet putosivat 20-30 %:sta 2-3 %:n alueelle puolessatoista vuodessa ja samalla reklamaatiot putosivat lähes nollaan. Tähän samaan olin käyttänyt Kempillä aikaa 5 vuotta. Toki Kemppi oli 10 x suurempi yksikkö!
Reklamaatioiden tasoa ei ole tiedossa (tilastoitu) vuosilta 1987-1990. Oletus on, että taso oli 10-15 % paikkeilla. Syy tähän saattoi olla, että en ollut erityisen kiinnostunut reklamaatioista enkä halunnut huomion kohdistuvan vuosien 1985-88 virheisiin. En kysellyt lukujen perään. Noudatin säätö- ja laatutekniikan perussääntöjä: 1) Ohjaa sisäänmenoja, ei ulostuloja; 2) Vaihtelua ei voi kompensoida, säätää; 3) Eliminoi ensin vaihtelu ja säädä vasta sitten keskiarvoa; 4) Paranna systeemiä, prosessia tuotteiden sijaan.
Vuoden 1991 elokuussa määriteltiin uudet virherajat visuaaliseen tarkastukseen (herkistettiin systeemiä ja pienimmätkin asiakkaalle näkymättömät virheet rekisteröitiin lopputarkastuksessa). Samalla lisättiin merkittävästi valon intensiteettiä (lux), jolloin havaittujen virheiden määrä (input) kasvoi ja saatiin reklamaatioprosenttia painettua edelleen alaspäin kirjaamalla inputit ja analysoimalla ne SPC:llä. Stalalla linjalta löydettyjen virheiden määrä oli merkittävästi pienempi kuin Kempillä. Linja oli leikkureineen ja veto-, hitsaus- ja pesukoneineen oleellisesti erilaisempi (prosessimaisempi) kuin Kempillä. Lopputarkastus oli visuaalista tarkastusta – ”miltä näyttää?”, kun taas Kempillä se oli toiminnallista tarkastusta – ”voiko hitsauskoneella hitsata?”.
Myöskään Stalalla ei (Kempin kokemuksen mukaisesti) tutkittu yksittäisiä reklamaatioita muutamaa poikkeusta lukuun ottamatta (1-2 kpl/vuosi) yliohjausvaaran vuoksi. Reklamaatiot kyllä tilastoitiin vuodesta 1990 lähtien, vastattiin asiakkaille asiallisesti ja joissain tapauksissa käytiin korjaamassa lähinnä kuljetusvaurioita. Vain niissä tapauksissa, joissa reklamaation SPC-ohjausraja ylittyi, reklamaatiot selvitettiin samalla tavalla kuin laatutaululla sisäiset virheet. Reklamaatioita seurattiin kuukausitasolla SPC-rajojen avulla. Kuvassa 6 näkyy keväällä 1999 paha reklamaatio, joka johtui vesilukosta. Siinä oleva kuula oli virheellisesti rautaa (ruostui), kun piti olla ruostumatonta. Alihankkijan virhe. Reklamaatioiden systeemivirheisiin puututtiin, esimerkiksi pakkausvauriot. Pesupöytien suojapakkauksia testattiin ja parannettiin.
Tätä SPC-parannusmenettelyä ei saa sotkea 1970-80-luvun ”laadunvalvontaan, tarkastukseen ja viallisten hylkäämiseen”, joka on reaktiivista korjaustoimintaa. Karsinta voi johtaa hyvään laatuun samalla kun karsinnasta johtuva tuotantomenetys kasvaa. Tämä linja oli ollut Stalalla vuoteen 1997 asti. Lopputarkastus hylkäsi suuren osan valmiista pesupöydistä. Hylättyjen pöytien (naarmujen, kolojen) korjaus oli vaikeaa ja vei paljon aikaa hiontoineen! Laatutaulujenkaan aikana loppu-tarkastuksesta ei tietysti voi luopua, mutta sen hylkäämien määrä on saatava alenemaan ennaltaehkäisyllä.
Laatutaulussakaan kaikki ei aina sujunut kuin ”Strömsössä”. Uuden käyttöpäällikön tullessa yritykseen vuoden 2001 syksyllä, toi hän mukanaan omat ”ideansa” laadun parannuksesta. Tämä tarkoitti kaikkien virheiden tutkimista. Niin loogista, mutta niin väärin. Ja mitä siitä seuraa. Kaaos. (Katso kuvat 6 ja 11 vuodesta 2001 eteenpäin) Epästabiilisuus alkaa kasvamaan; poikkeamat pesupöytä- ja putkituotannossa, josta seuraa myös asiakasreklamaatioiden kasvu.
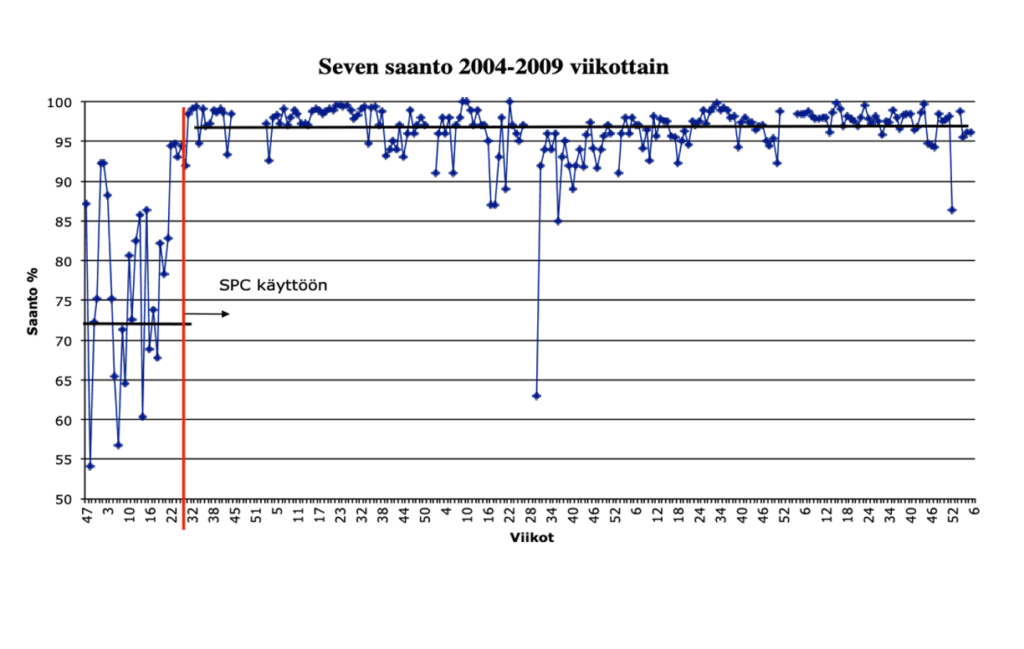
Vuoden 2004 kesään laadun johtoryhmässä katseltiin tilannetta, kunnes viikolla 20 yrityksen omistaja Reino Rajamäki ”hermostui ja määräsi” laatutaulut otettavaksi ”uudelleen” käyttöön niin kuin oli tarkoitus (SPC). Välittömästi prosessi stabiloitui ja saanto nousi 70 %:sta yli 95 %:n ja jatkoi paranemistaan. Samoin tapahtui putkituotannon ohiajon suhteen.
Alihankkija ja laatutaulu
Tuotannossa siirryttiin 2000-luvulla yhdestä ruostumattomasta syvävedetystä pesupöydästä hitsattuun rakenteeseen, jossa kansi ja allas tehtiin erillisinä ja hitsattiin alihankkijalla yhteen. Syy tähän oli syvä ja lähes neliskulmainen allas, jota ei voinut vetää yhdestä levystä riittävän syväksi samalla, kun siitä tehdään pesupöydän kansi.
Ohutsaumahitsaus ruostumattomaan teräslevyyn ”siististi” oli erittäin vaativa. Työn teki alihankkija Compusteel Oy Savonlinnassa. Stala toimitti altaan ja kannen. Alihankkija hitsasi altaan kiinni kanteen tig-hitsauksella.
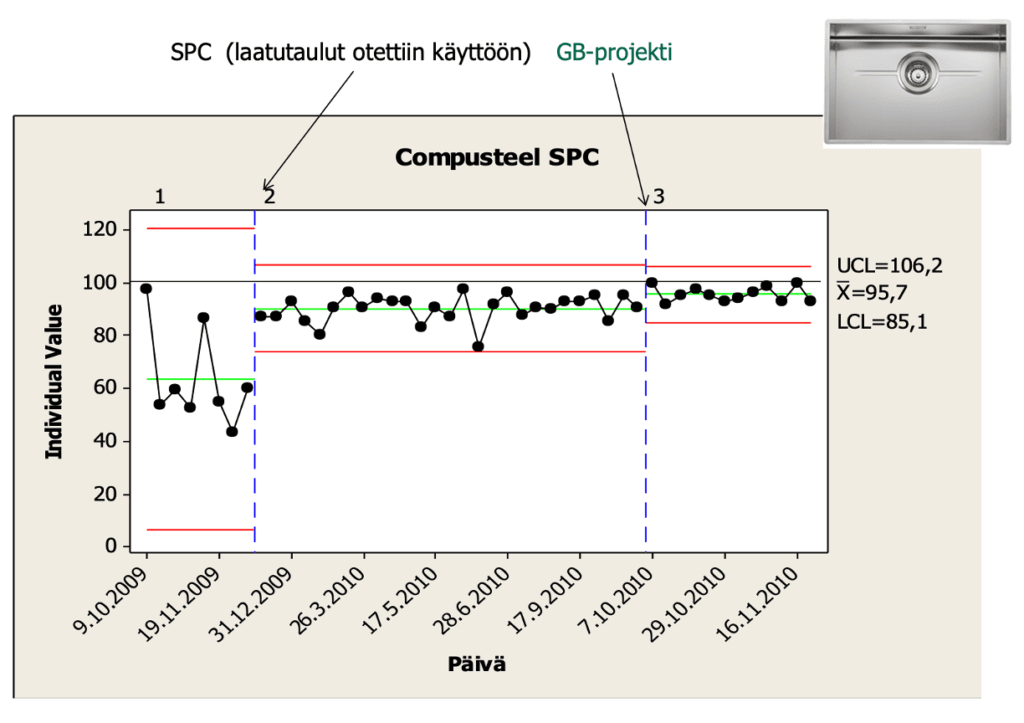
Alihankkijahitsauksesta ei hyvistä yrityksistä huolimatta tullut mitään. Puolet materiaalista tuhoutui. He eivät osanneet parannusteoriaa, laatuteoriaa, vaan tutkivat jokaisen epäonnistuneen altaanhitsauksen ja muuttivat hitsausarvoja ja jigejä jatkuvasti. Hukkamateriaalin kustannus ylitti monin kerroin työn jalostusarvon. Vaarana oli koko uuden tuotelinja kehityksen epäonnistuminen.
Alihankkija ”määrättiin” käyttämään laatutaulua (SPC). Menetelmä on sama, kuin autoteollisuuden alihankkijoilla. Heidät määrätään IATF TS 16949 -standardilla ja AIAG manuaalilla käyttämään SPC:tä. (12). Opetin taulun periaatteen ja käytön. Hitsauksessa syntyneitä erilaisia virheitä kerättiin laatutauluun ja analysoitiin tilastollisesti ja puututtiin vain erityissyihin, laatu parani dramaattisesti ja välittömästi ja samalla vaihtelu pieneni (systeemin muutos). Tämän saman voi demonstroida Demingin suppilokokeella.
Joku voisi ajatella, että tutkittiin kaikkia virheitä tarkemmin. Todellisuudessa laatutaululla ja sen C-rajoilla estettiin satunnaissyyperäisten virheiden tutkiminen ja samalla ”oikaistiin” inhimillisen subjektiivisen virheen käsitettä. Virheistä ehkä 5-10 % tutkittiin ja 90-95 % aikaisemmin tutkituista jätettiin tutkimatta, mutta kerättiin kyllä taululle!
Tämän jälkeen laatutaulua pidettiin yllä ja puututtiin vain erityissyihin, laatutaso pysyi hallitusti samalla stabiililla tasolla. Tuotanto ja tuotteen myynti voitiin käynnistää.
Stabiilin tason parantamiseksi systeemiä eli satunnaista vaihtelua oli edelleen pienennettävä, jotta saannon keskiarvoa saa parannettua. Ruostumaton teräs on kallista! Tämä tapahtui Six Sigma -prosessilla, jonka esitestatut parannukset on otettu käyttöön 7.10.2010. Prosessin virheet puolittuivat ja saanto nousi noin 90 %:sta 95,7 %:iin. Virheiden kautta tämän tason parantaminen on jo vaikeaa. Six Sigma Green Belt -työn teki Henri Hiltunen. Kuvassa hänen projektisuunnitelmansa ja projektin yhteenveto (Lähde: QKK arkisto).
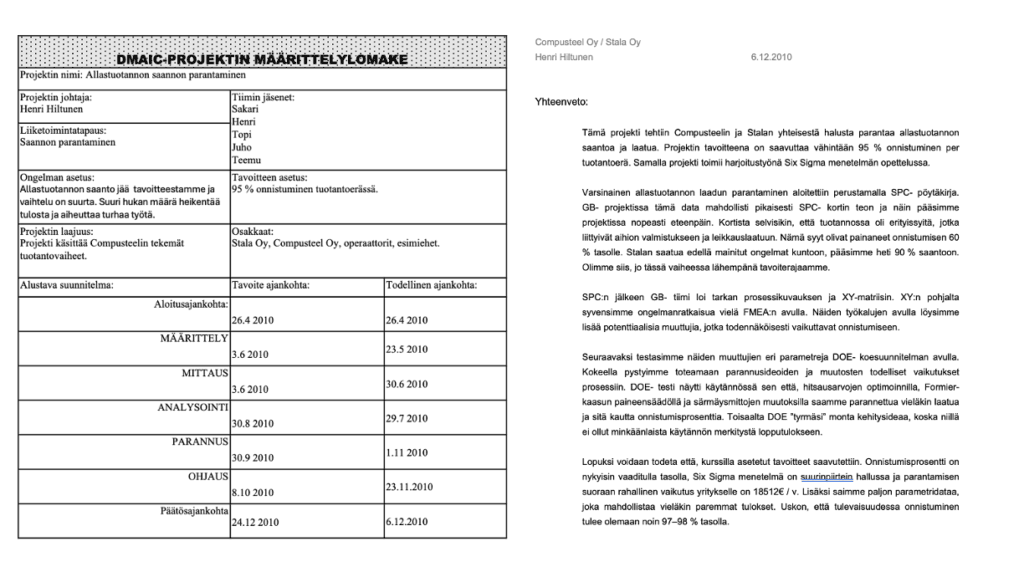
Laatutaulut ja putki-/palkkituotanto
Pesupöytälinjan rinnalla toimi samoissa tiloissa 3-4 putkikonelinjaa (1990), joissa ruostumatonta teräsnauhaa (paksuus 1-5 mm) syötetään koneeseen ja ulos tulee muokattua putkea, joka katkotaan 6000 mm pituisiksi putkiksi (palkeiksi).
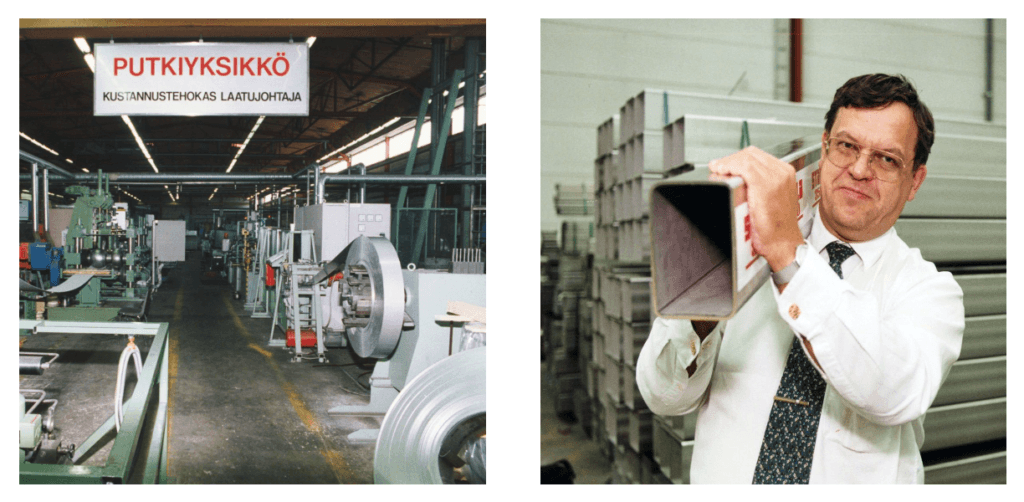
Stala Oy oli ensimmäinen yritys, jossa konelinjalla käytettiin laatutauluja. Konelinja on ”yksi” kone, jonka pituus on 20-40 m. Tulos oli erinomainen. Laatutaulu eli attribuutti SPC sopi tähänkin erinomaisesti. Kaikki kone- ja laitehäiriöt, hukat kirjattiin laatutauluun ja analysoitiin C-rajoilla. Laatutaulu ”ammuttiin” videotykillä tehdastilan takaseinään kokoon 5 X 4 m. Ei siis ollut paperinen kuten pesupöydässä. Videolla pyöritettiin PowerPoint -ohjelmaa, jossa oli myös erityissyytaulu ja muuta informaatiota. Ohjaus tapahtui etänä. Tähän päädyttiin osin kolmivuorotyön ja havaittavuuden vuoksi. Kokemus oli hyvä. Ohiajoprosentti (hylkyprosentti) putosi 7-8 %: sta 2-3 %. Tässä tapauksessa n. 2 % ohiajo (hylky) johtuu emokelojen suuruudesta. Kelan alku ja loppupäästä menee hylkyyn 3-5 m. Putkia ei voi jatkaa. (1 % yksikön muutos on miljoonia markkoja silloin ja nyt euroja!).
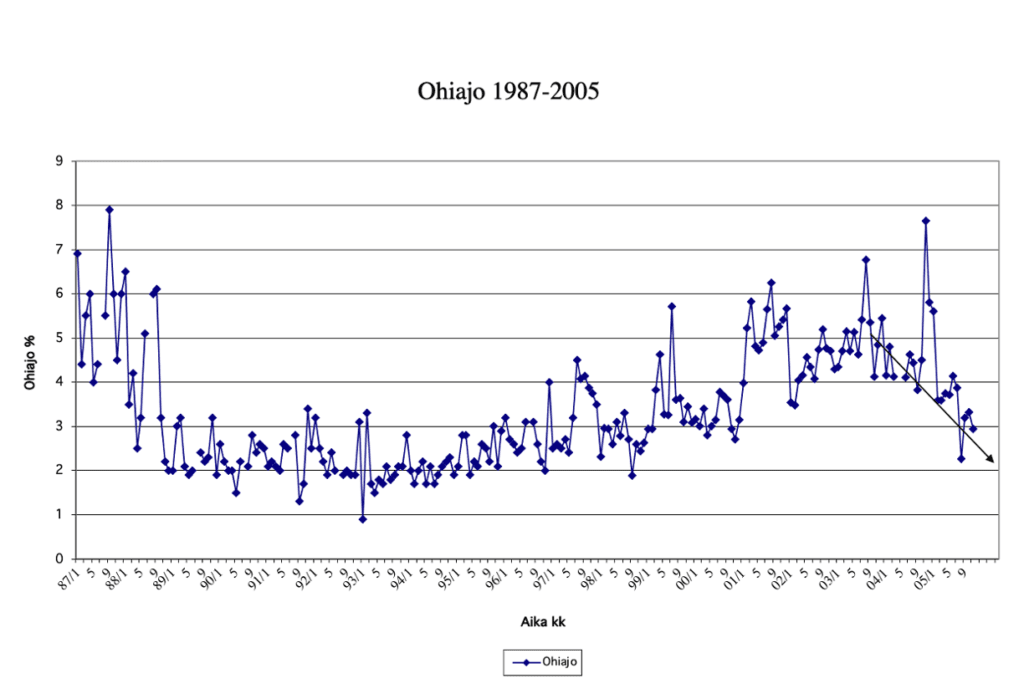
Tässäkin tapauksessa laatuteoria ja laatutaulu alkoi hiipumaan vuoden 1996 vaiheilla, kunnes 2003-2004 palattiin alkuperäiseen ideaan. Vertaa pesupöytälinjaa.
Lääketieteessä tätä ilmiötä sanotaan ”hoitoväsymiseksi” (fatigue). ”Hoitoväsymys on määritelty kyllästymiseksi jatkuvaan hoitamiseen; siitä on seurauksena hoitotauko ja sen myötä todennäköisesti oireiden paheneminen. Ei jakseta enää noudattaa hyvää ”hoito” käytäntöä”.
Laatutauluja pitkään käytettäessä olosuhde ja henkilöstö muuttuu ja unohtuu prosessin parantamisen (ennaltaehkäisyn) teoria ja korvautuu tuotteen ”tässä ja nyt” vika ja korjausteorialla. Laadun puolella tästä otteen herpaantumisesta voisi käyttää termiä laatuväsymys tai -herpaantuminen.
Osasyynä voi olla, että itse taulusta ei näe kehitystä. Kehitys on nähtävissä viikko-, kuukausi- tai vuosiyhteenvedoista kuten tässä artikkelissa. Tästä syystä pidettiin yleisiä infotilaisuuksia. Kuukausi ja vuosikäyrät olivat nähtävillä tauluilla, mutta silti näin kävi. Huomaa, että muutos on hidas ja hiipivä – asioita jätetään vain tekemättä.
Varaston laatutaulu ja toimitusvarmuus
Stalassa oli myös varaston/lähettämön käytössä laatutaulut, joiden keskeinen mittari oli toimitusvarmuus. Kuvassa 12 puolen vuoden käyrä käynnistymisestä lähtien. Toimitusvarmuus oli tällöin lähetettyä yksikköä kohden 70 – 75%. Taulu oli käytössä vuosia. Toimitusvarmuus saavuttu 99 %:n tason ja säilyi vuosia.
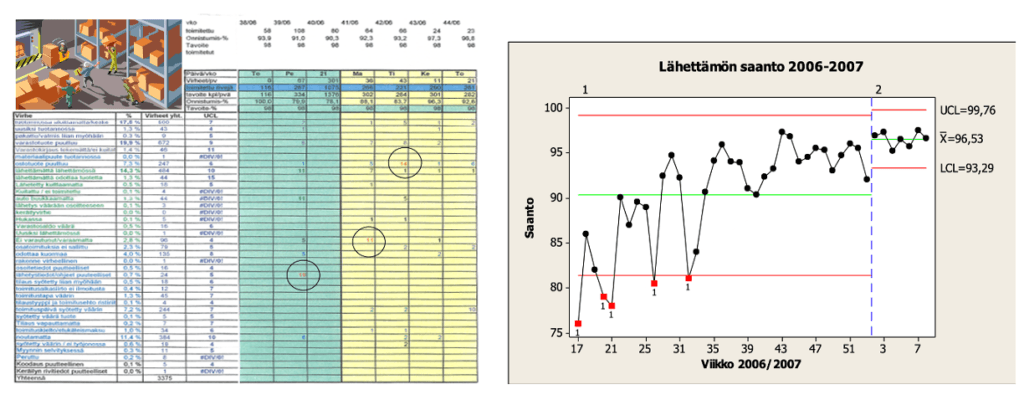
Toiminnan laadun laatutaulut
Stalassa oli lukuisia toiminnan laadun (hallinnon) laatutauluja mm. palkka ja laskutus- ja myyntiprosesseissa. Karkeasti ottaen 10-40 % tapahtumista oli virheellisiä. Laatutaulujen käytön jälkeen virheprosentit putosivat 1-2 %:iin.
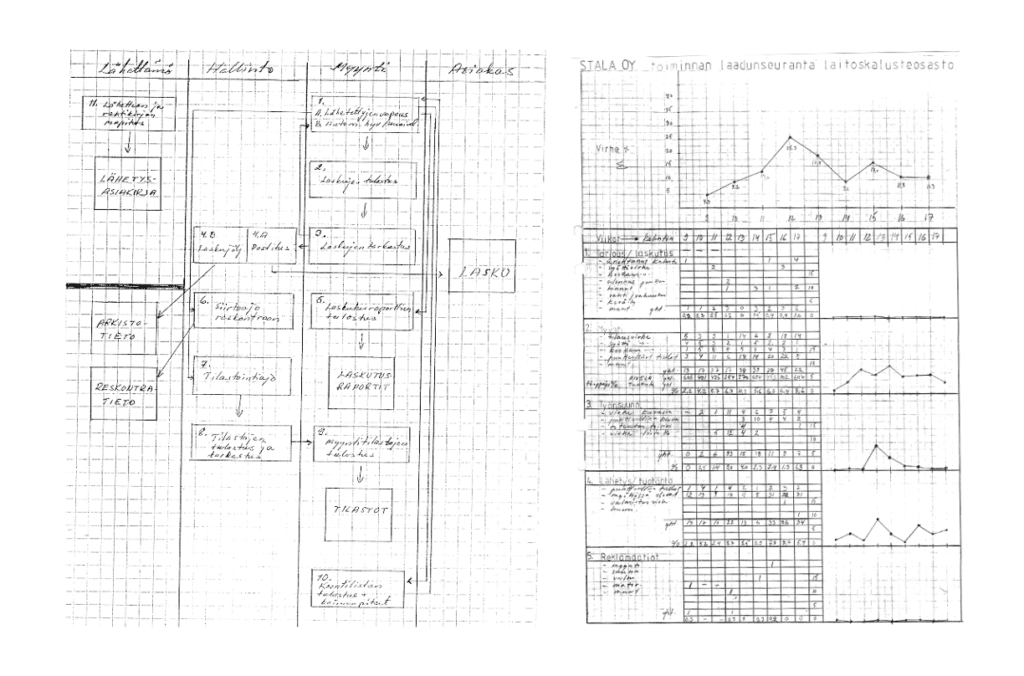
Stala Oy:n laatutietä on kuvattu kahdessa kirjassa: Prof Taina Savolainen: ”Laatujohtamisopin kehittyminen” 1997 ja Kalevi Laalo – Reino Rajamäki ”Työelämän murros” 2008.
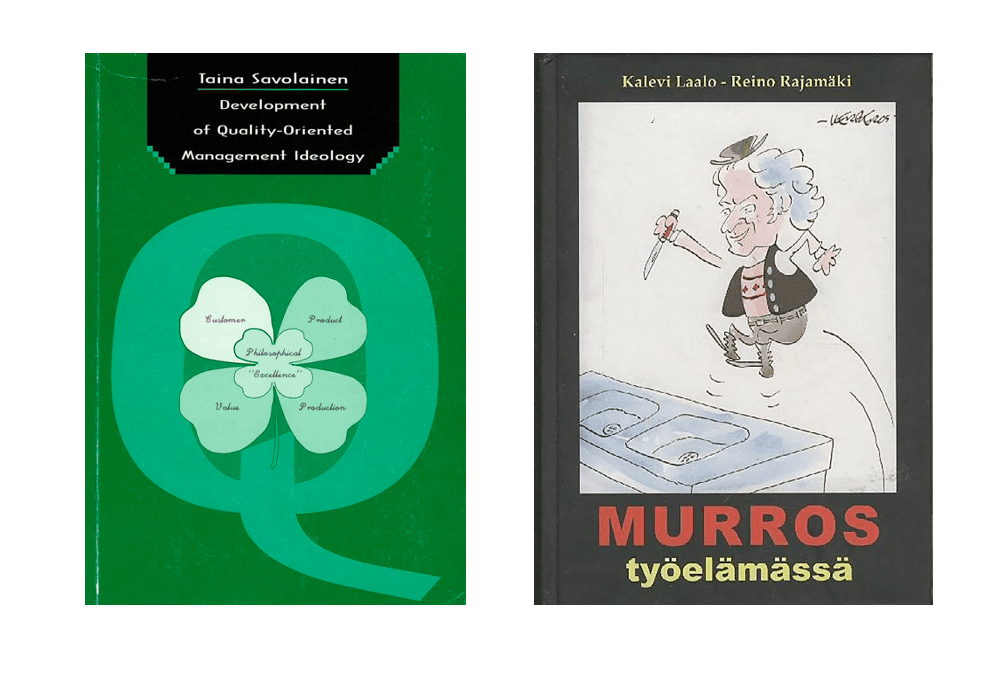
Professori Taina Savolainen teki väitöstutkimuksen ”Laatujohtamisopin kehittyminen” 1997 (Development of Quality-Oriented Management Ideology) (13), jonka yhtenä yritystapauksena oli Stala Oy. Hän toteaa väitöstutkimuksessaan mm.
”Stalassa oppia syötti ulkopuolinen viisas mies. Ylin johto suki vahvasti myötäkarvaan ja istutti laatunäkemystä kulttuurilähtöisesti, esimerkiksi käyttämällä kieltä, jota työntekijät ymmärsivät”.
Kirjassa ”Murros työelämässä” 2008 Kalevi Laalo – Reino Rajamäki kertovat tarinan Stalan laatutaulujen alkuajoista. Teollisuusneuvos Reino Rajamäki kertoo (s. 62-63):
”Käynnistimme laatutyön Stalassa 80-luvun puolivälissä. Pääluottamusmiehemme Eero Vuorisen tehtävänä oli panna tiskipöydän päälle sininen muovimassa, jonka piti suojella pintaa naarmuuntumasta rakennusaikana. Eero kun massas, se sano, että kyllä se Reino on niin, että sun on jotakin tehtävä tälle laadulle, kun tuotteissa on lommoja. Lommot meni piiloon, kun pantiin siihen se massa. Mä ajattelin, että mitä helvettiä mä voin tehdä.
Tartuin ikään kuin vanhanaikaiseen. Johtoryhmässä sovittiin: ketkä ovat Suomessa johtavia laatuguruja. Niitä löytyi viisi.
He kävivät esitelmöimässä. Siinä rumbassa tuli valittua Eero Karjalainen. Diplomi-insinööri. Hän lähti systemaattisesti kehittämään laatujärjestelmäämme. Hän oli tiukan tuntuinen kaveri, joka kuitenkin ymmärsi jätkäpojan sielunelämäämme, jota moni ei ymmärrä. Siksi hän tuli toimeen stalalaisten kanssa.
Niin meille ilmestyivät seinille ns. SPC-taulut: Statistical Production Control. Kun me sitten kierrettiin laatujohtoryhmän kanssa Suomen tehtaita, joissa oli aloitettu, niin monissa työntekijät olivat repineet ne helvettiin.
Niihin tauluihin merkitään joka päivä, paljonko on virheitä tullut. Ne pitää eliminoida. Näin me etenimme, kunnes Karjalainen sanoi, että nyt Stala on siinä pisteessä, että voimme hakea Suomen Laatuyhdistyksen laatupalkintoa.
Oltiin pääluottamusmiehen kanssa pokkaamassa sitä. Ei siinä ollutkaan varatoimitusjohtajaa vaan pääluottamusmies! Mietipä ajattelutapaani.”
Suomen Laatupalkinto oli jatkoa Laatuyhdistyksen palkinnolle. Sen Stala sai ensimmäisenä Suomessa vuonna 1991.
”Laatupalkinto huomattiin niin tärkeäksi, että se auktorisoitiin ja sen taakse tuli koko elinkeinoelämä valtiovallan suojeluksessa. Se sai nimekseen Suomen Laatupalkinto.
Haimme sitä ja voitimme senkin. Palkinnon ojensi Tasavallan presidentti. Tämä kaikki saavutettiin pkt-sarjassa.
Ne olivat kannustavia palkintoja ja ovat Stalan vitriinissä, sinne ne kuuluvat.
Pidimme tietysti hyvät juhlat: teltta pystyyn ja kunnon kännit! Se oli Stalan tapa ja hyvä tapa olikin.”
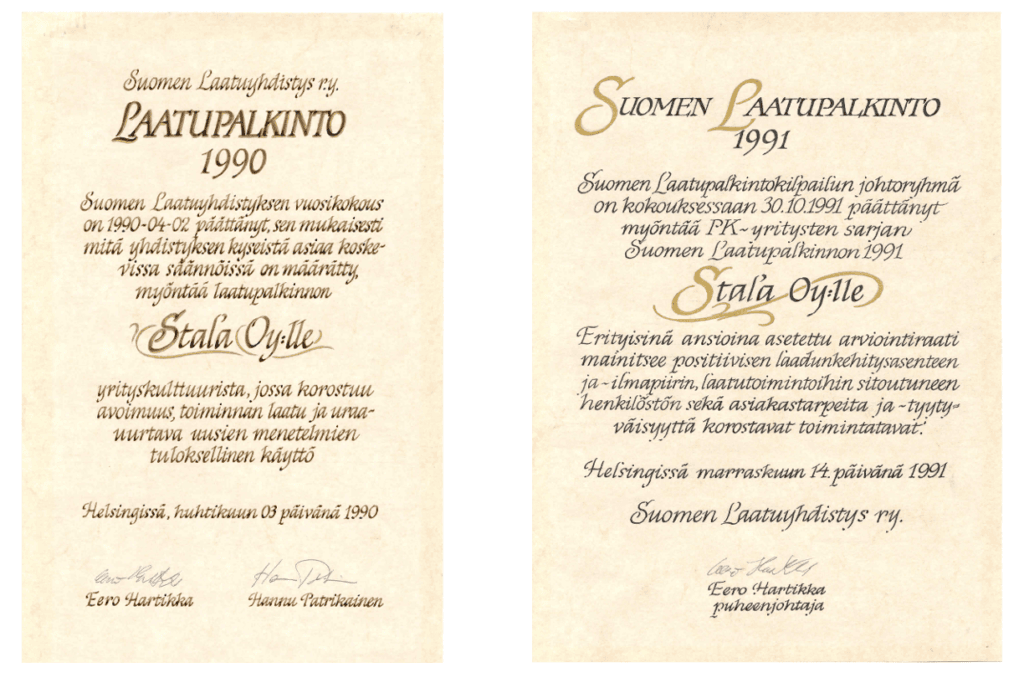
IV. Kehitysvaihe 1990-1991 Halton Oy
Neljäs kehitysvaihe käynnistyi, kun vuonna 1990 Halton Oy:ssä otettiin käyttöön SPC-laatutaulut ja erityissyytaulut samaan aikaan kuin Stala Oy:ssä.
Halton on mm. sisäilmailmalaitteita, poistoventtiilejä valmistava globaali yritys, joka päätehdas on Iitin Kausalassa lähellä Lahtea. Henkilöitä n. 1900. Yritys on perustettu 1969.
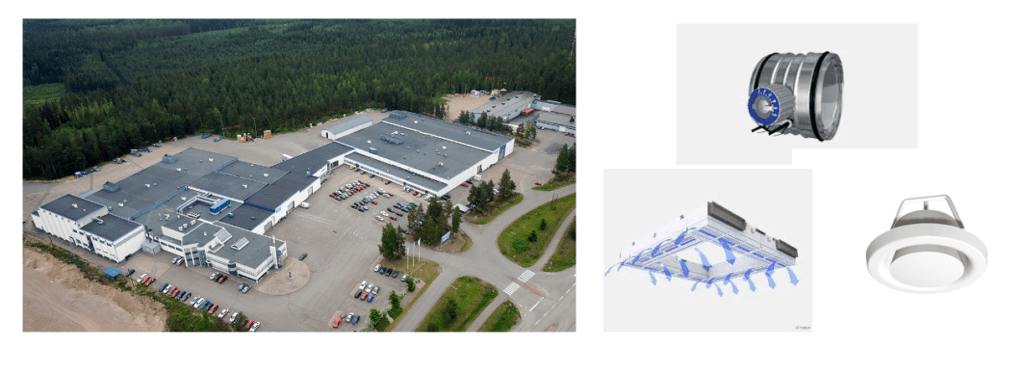
a) C-raja ja laatutaulu
Haltonin tauluihin tulivat ensimmäisen kerran selkeät SPC-rajat ja niin sanottu erityissyytaulu (vuotta ennen Stala Oy:tä). Stalaan rajat ja erityissyytaulu siirrettiin Haltonin esimerkin myötä.
SPC-rajalla määritettiin ja eroteltiin systeemin/prosessin aiheuttama satunnainen vaihtelu erityisestä syystä johtuvasta vaihtelusta (yleensä systeemin ulkopuolelta tulevasta).
Tämä parannus – rajat ja erityissyytoimenpiteet – oli seurausta sekaannuksesta ja ihmetyksestä, jonka Haltonin työntekijät esittivät silloiselle laatupäällikölle Mertsi Niemelälle.
– miksi kaikkia virheitä ei tutkittu ja tehdäänkö näille virheille yhtään mitään?
Tästä kysymyksestä nousi selkeä este taulun käytölle. Yhdessä Mertsin kanssa purimme esteen ja päädyimme laittamaan selkeät C-rajat tauluihin, erityisen toimenpidetaulun ja selittämään, miksi juuri nämä ilmenemismuodot tutkitaan. Olin koko Kempin ajan empinyt rajojen käyttöä niiden ”vaikean” kansanomaisen perusteltavuuden vuoksi.
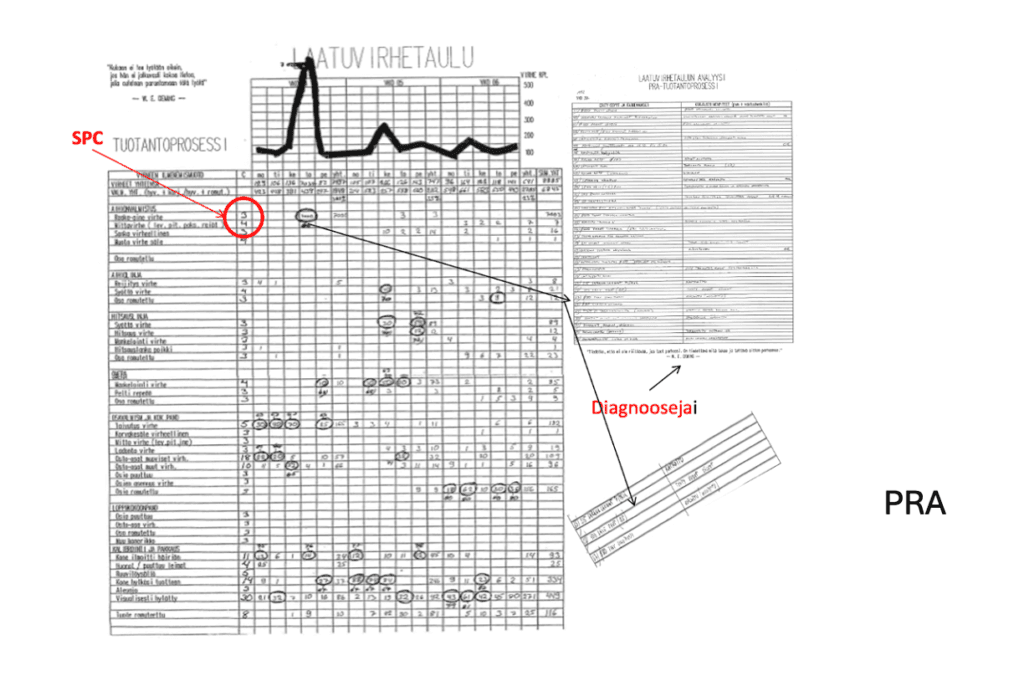
Erityisesti on huomattava, että laatutaulun vasemmassa laidassa on SPC-rajat (C) merkittynä numeroin. Nämä raja-arvot asetetaan tyhjään tauluun edellisen 3-4 viikon virhekeskiarvon tilastollisen käsittelyn perusteella. Poisson-jakaumassa virheiden keskiarvo C määrittää keskivaihtelun, varianssin eli sigman, joka on neliöjuuri keskiarvosta s=√C. SPC-ohjausrajat saadaan laskettua 3 x sigma eli C± 3√C. Katso artikkeli: Laatutaulu: virheet ja hukka (2).
Raja-arvon ylitys tarkoitti ”pakkoa” siirtää ilmenemismuodon syy erityissyytauluun ja edelleen selvittää ilmenemismuodon syy (erityissyytaulun vasen laita) ja toimenpiteet syyn poistamiseksi.
Ongelmana SPC-rajan asettamisessa on ”numerologia”, jonka taustaa, harvinaisten virheiden Poisson-jakaumaa, ei ymmärretä. Siksi vaadittiin vahva koulutus tauluihin ja niiden käyttöön työntekijöistä esimiehiin. Yleensä yksi tai kaksi henkilöä on koulutettu SPC-rajojen asettamiseen. Suora laskutoimitus ja sen tuloksen käyttö ei johda oikeisiin ja erityisesti vaikuttaviin rajoihin. Syy tähän on, että induktiiviset rajat on asetettava stabiilin prosessin mukaan, jota vielä ei ole. On siis arvioitava eli estimoitava tilannetta. Laskenta antaa osviittaa!
b) Tulokset Haltonin laatutaulusta
Laatutauluilla (+SPC) ja niihin liittyvillä erityissyytauluilla saatiin merkittävä laadun paraneminen vuosina 1991-95. Virheiden kokonaismäärä laski yli 60 %:sta alle 10 %:iin laskettuna virheitä/tuote asteikolla.
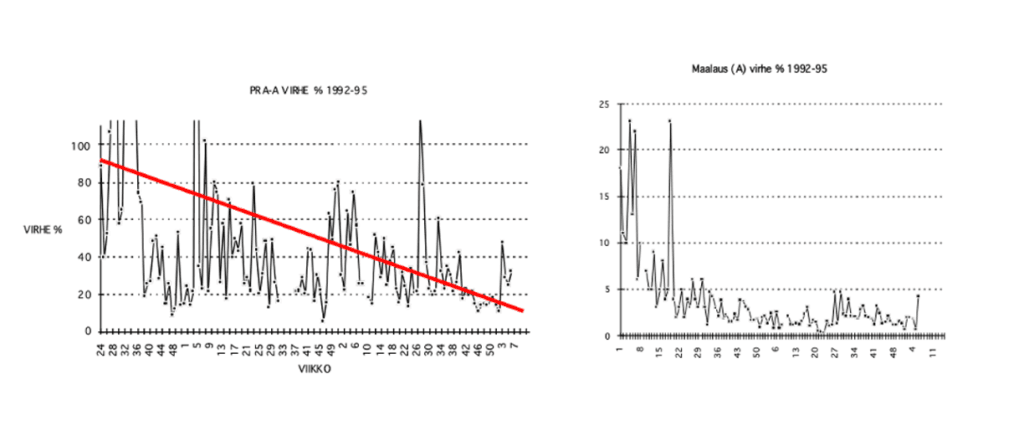
Tuotantojohto tarkisti laatutaulut ja erityisesti erityissyytaulut (toimenpidetaulut) viikoittain, että kaikki ne ilmenemismuodot, jotka ylittivät C-rajan, siirrettiin erityissyytauluun ja että analyysi, toimenpide ja vastuuhenkilö oli merkattu. Myös toimenpiteet esim. jonkin koneen laakerinvaihto, todennettiin ja tarkastettiin ja valvottiin kuukausittain paikan päällä tai henkilön koulutustapahtuma koulutettavalta itseltään. Laatua johdettiin ja valvottiin aktiivisesti!
Käytössä oli yhteensä 14 laatutaulua, joista osa konttoripuolella (palkkahallinto, ostotoiminta, tilaustenkäsittely jne.)
V. Kehitysvaihe 1990 – 2004 Eimo Oy ja Metsä Botnia Oy 2002 – 2003
Viides kehitysvaihe: Taulun siirtyminen tietojärjestelmään. Eimo Oy otti käsin tehdyt laatutaulu käyttöön vuonna 1990, hyvin pian Haltonin jälkeen. Eimo Oy on perustettu vuonna 1957. Omistajina silloin Unto Eilamo (perustaja) ja Reino Rajamäki (Stala Oy) ja Jalo Paananen (Peikko Oy). Yritys siirtyi myöhemmin Foxconnin omistukseen.
Eimo-Muovi valmisti teknisiä muovikomponentteja ja tuotteita ruiskupuristuskoneilla (Injection Molding Press). Koneita oli 90-luvun vaihteessa 10-15 kpl. Yritys laajeni voimakkaasti Nokian kännykänkuorien valmistukseen ja osin kokoonpanoon ja oli pörssiyritys. Koneita oli yli 150 kpl yrityksen siirtyessä Foxconin omistukseen.
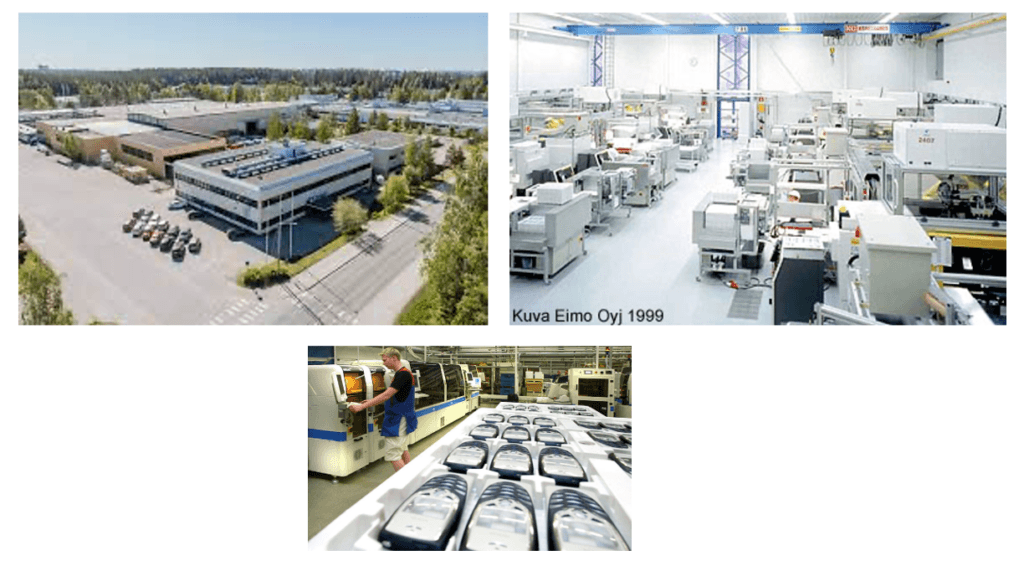
Tunsin Eimon jo 1980-luvun alusta Kempin alihankkijana. Yritys valmisti erilaisia teknisiä ruiskupuristusosia mm. vesipumpun osia Kempille. Yritys ei ollut erityisen hyvässä maineessa (huonoin Kemppi Oy:n alihankkija).
Jouduin Eimolle laatukonsultiksi Stalan omistajan Reino Rajamäen ”käskyllä”- laita mylly kuntoon. Yrityksen toimitusjohtajana toimi DI Seppo Jaakkola ja laatupäällikkönä Juhani Ranivaara. Ydinongelma taas kerran oli asiakas-reklamaatioiden voimakas kasvu ja siitä seuraava TUHO. Lopputarkastuksen virheprosentti on lähes suoraan verrannollinen reklamaatiomääriin, joskin yhteys voisi olla parempikin (4). Asiakkaat palauttivat tai ilmoittivat virheelliset kappaleet yksittäin ja erinä, josta saatiin reklamaatioprosentti. Tätä ei käytetty toiminnan suoraan arviointiin (liian hidas, 0,5- 1 vuoden viive ja epämääräinen).
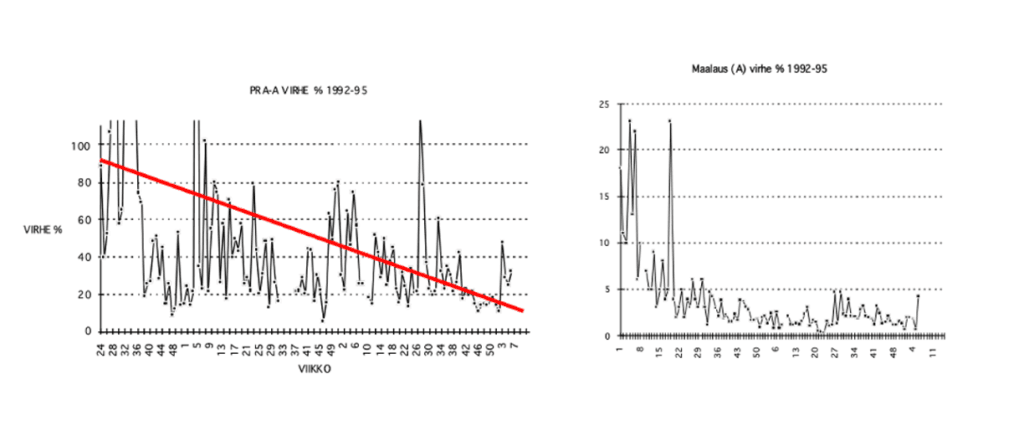
Vasemmanpuoleisessa kuvassa 20 virhemäärien kehitys ennen ja jälkeen laatutaulun käyttöönoton. Data on lopputarkastuksen hylkäysdataa. Olen tarkastellut tätä lopputarkastusta artikkelissa (4). Lopputarkastuksen suorituskyky ei riittänyt! Huomaa, kuinka ennen laatutaulua (SPC), virhemäärät kasvoivat kasvamistaan ja hajonta lisääntyi. Lisääntymisen aiheutti voimakas asiakaspaine (IBM, jolle Eimo Oy ruiskupuristi muoviosia) ja intensiivisempi virheiden tutkiminen ja toimenpiteet. Ongelma on, että 94 % virheistä EI ole löydettävissä syytä! Vuonna 1990 puutuin ”peliin”, kielsin reklamaatioiden tutkimisen ja erityisesti toimenpiteet. Sen sijaan otettiin käyttöön laatutaulut (oikeanpuoleinen kuva) ja SPC-rajat ja vain inputtien erityissyyt tutkittiin ja tehtiin toimenpide välittömästi muovikoneella.
Vasemmanpuoleisessa kuvassa oikeassa laidassa voimakas virheiden nousu. Vuonna 1995 prosessiin tuli uusi kännykän linssejä valmistava kone (poikkesi muista prosesseista), joka erotettiin omaksi käyräksi vuonna 1996 ja luotiin oma laatutaulu. Pääkäyrä palautui trendisuoralle!
Oikeanpuoleisessa kuvassa on täytetty (täysi) laatutaulu. Kun taulu otettiin viikolla 19 käyttöön, siihen oli edellisen taulun perusteella määritetty SPC-rajat eli n. C-raja. Näkyy ensimmäisenä sarakkeena. Kun ilmenemisluokan (virheen nimitys) esiintymistiheys ylittää C-rajan, tutkitaan erityissyy ja tehdään välittömästi toimenpide. Tässä tapauksessa kaikki virheelliset tuotteet hylätään ja romutetaan koneella (ei voi korjata). Talteen otetaan vain erityissyyinformaatio ja siitä johdettu korjaustoimenpide, joka tulee näkymään seuraavien päivien ja viikkojen kuluttua alenevina virhe ja hukkalukuina.
Eimolla oli myös lukuisia toiminnan laadun prosesseja, joissa oli laatutaulut. Esimerkkinä palkkalaskenta (tuntikorttien virheet)
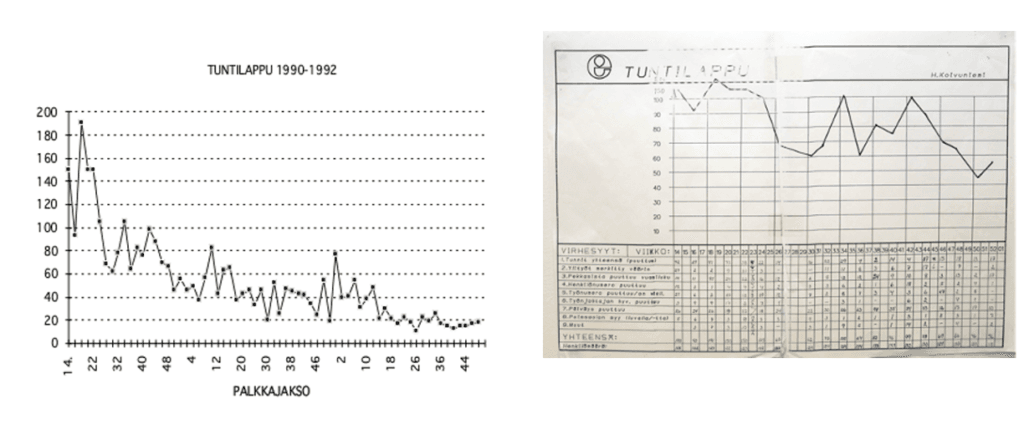
Henkilömäärä (= tuntikorttien määrä) prosessissa on n. 100, joten ennen kehittämistä jokaisessa tuntikortissa oli lähes kaksi virhettä/työntekijä, jotka palkanlaskija Hilkka selvitti ja korjasi viikon ajan. Tuntikortti oli ”palkkauksen” perusta että työaikaseuranta, jonka työntekijä antoi ja allekirjoitti. Jokaisella työllä (töitä saattoi olla yhdellä kortilla kymmeniä) oli oma urakkahinta ja tuntien, määrien oli täsmättävä yrityksen muuhun kirjanpitoon ja työaikalainsäädäntöön. Opastin Hilkkaa, että puutut vain erityissyihin ja selvität ne! Älä stressaa muista, jätä ne rauhaan! Rajat oli merkattu, vaikka kuvassa niitä ei näy.
On itsestään selvää, että prosessi on tehostunut ja tuottavuus noussut.
Hilkka pystyi tekemään viikon työn päivässä, kun virheitä ei ole. Käyrästä voidaan havaita, että puoliutumisaika tämän tyyppisissä prosesseissa on n. 6 kuukautta.
SPC (laatutaulu) oli osa Eimon laadun kehittämistä, joka kesti useita vuosia. Kuvassa keskeiset laatuhankkeet. Huomaa, että tässä tapauksessa kehittäminen aloitettiin laatukoulutuksella ja sen jälkeen tuli laatutaulut (SPC). Tämän jälkeen otettiin käyttöön erilaisia laatutyökaluja mm. Taguchi (teollisuuskokeet), jossa Eimo oli Suomen johtava yritys. Kokeita, joilla ruiskupuristuskoneita ja niissä valmistettuja osia ja tuotteita, optimoitiin, tehtiin satoja, jos ei tuhansia. Jokaiselle uudelle vaativalle tuotteelle ja muotille tehtiin Taguchi-parametrioptimointi, jolla virheprosentti pudotettiin 1/100-1/1000 osaan. Yleensä Six Sigma -tason 0,000034 % alapuolelle. Eimo oli ensimmäinen yritys Suomessa, jossa koulutin henkilöstön suomenkielisellä Six Sigma -aineistolla (Black Beltiksi ja Green Beltiksi) vuonna 2000. Eimo kustansi osin kurssien luomisen. Tästä alkoi meidän QKK julkiset Six Sigma -koulutukset seuraavana vuonna.
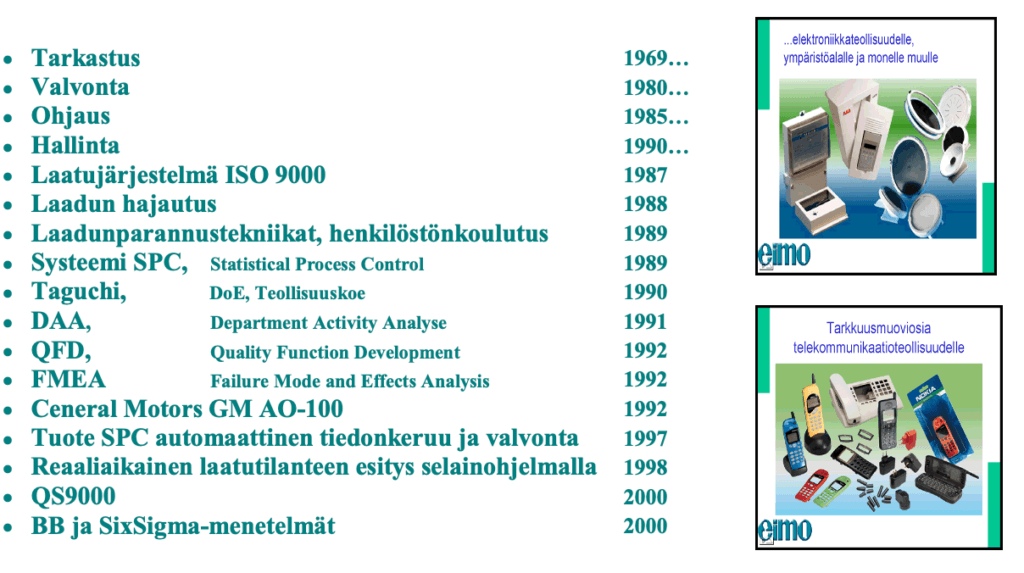
Laatutaulu tietojärjestelmään: DI Ari Pihlajavesi (Aspocomp) siirsi Eimon laatutaulun ja sen ylläpidon tietojärjestelmään 1996-1998 (automaattinen SPC tiedonkeruu ja reaaliaikainen laatutilanteen esitys selainohjelmalla). Tästä hankkeesta sai alkunsa hänen yrityksensä Predisys Inc (1996-). Tuotenimi oli eCoach (kuva 23). Yritys toimii Suomessa ja USA:ssa. Luomani laatutaulu levisi erilaisina versioina lukuisiin suomalaisiin ja ulkomaisiin yrityksiin. Arin vuonna 2023 äkillisen poismenon jälkeen yritystä johtaa hänen veljensä Harri Pihlajavesi. Predisys on palannut lähtökohtaansa ruiskuvalukoneisiin (Injection Molding Process) ja tarjoaa maailmanlaajuisesti tähän sektoriin SPC-ohjelmistoa muiden ohjelmien lisäksi.
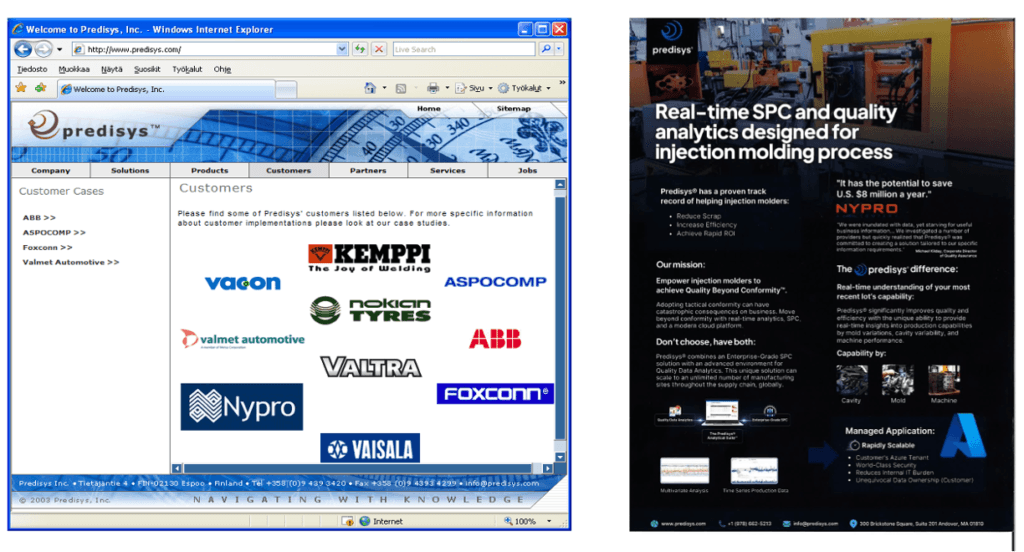
Ohjelmistojen suurin puute on, että ne tarjoavat ratkaisuja suoraan mitattavien (variaabeli) prosessien analysointiin ja virheiden ennaltaehkäisyyn. Näiden prosessien osuus on kuitenkin pieni, ehkä alle 5 %. Suuri osa prosesseista on ei-suoraan mitattavia (attribuutti) prosesseja, joissa on käytettävä luokiteltua dataa (työntekijöiden havainnointiin perustuvaa). Ihmisten havainnointia ja kykyä aistia poikkeamia on vaikea automatisoida (konenäkö?).
Itseohjautuvat autot ovat sensoreineen ja ohjelmistoineen, jos onnistuvat, esimerkki laatutaulujen ”tehtävästä”. Estää etukäteen poikkeamat (virheet, viat ja hukka). Tässä tapauksessa ojaanajot, kolarit, onnettomuudet. Taulut sinänsä voidaan helposti tehdä sähköisiksi, kunhan saadaan attribuuttidataa. Rajojen laskentaan ei ole ”vielä” automaattista algoritmia aivan kuten ei itseohjautuvaan autoon ole ”vielä” varmaa algoritmia. Kuski istuu vielä varalla!
Laatutaulun käyttöönoton yhteydessä, jos se on oikein laadittu ja sen käyttö on oikeaa ja tehdään toimenpiteitä, havaitaan usein selkeä laadunparannuksen hyppäys. Hyppäys tapahtuu erityisesti silloin, kun käytetään SPC-rajoihin perustuvaa taulua.
Eimolla työntekijät halusivat pitää myös fyysisiä tauluja reaaliaikaisen selainpohjaisen laatutaulun rinnalla, koska taulu sisälsi myös havaintoihin perustuvaa dataa mittausdatan lisäksi. Työpisteessä (muovikoneella) merkattiin kaikki hylätyt kappaleet ilmenemismuodon perusteella tauluun ja analysoitiin nopeasti mahdollinen erityissyy. (Paine, syöttö, lämpötila, materiaaliongelma jne.)
SPC automaatiojärjestelmään 2000 – 2004: Toinen esimerkki koskee Metso Automaation kehittämää järjestelmää Rauman sellutehtaalle (Metsä Botnia, Metsä Fiber), jossa painopiste on enemmän yksittäisten inputtien ja ohjausparametrien ominaisuuksien ohjaamisesta SPC-korttien kautta.
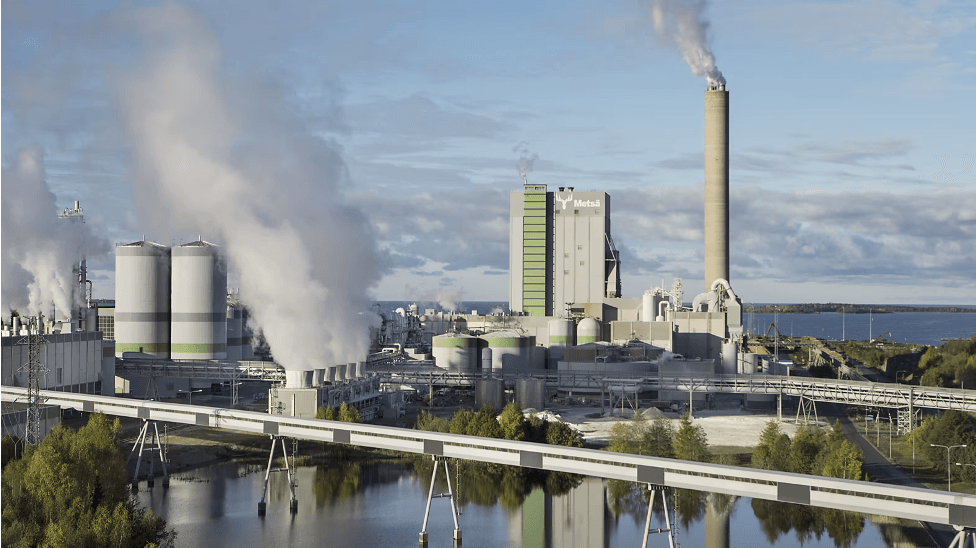
Tätä tehtiin yhdessä Jukka Rantamäen Botnia ja Markku Rintala Metso automaatio kanssa. Kysymys oli ylätason softan suunnittelusta ja toteutuksesta nimeltä DNA(spc). Vastaavia softia oli olemassa, mutta Metsä Botnia halusi soveltaa/muokata olemassa olevaa DNA-järjestelmään SPC:n soveltuvaksi. Valvomon käyttöliittymissä näkyi speksirajat, joilla prosessia aikaisemmin ohjattiin.
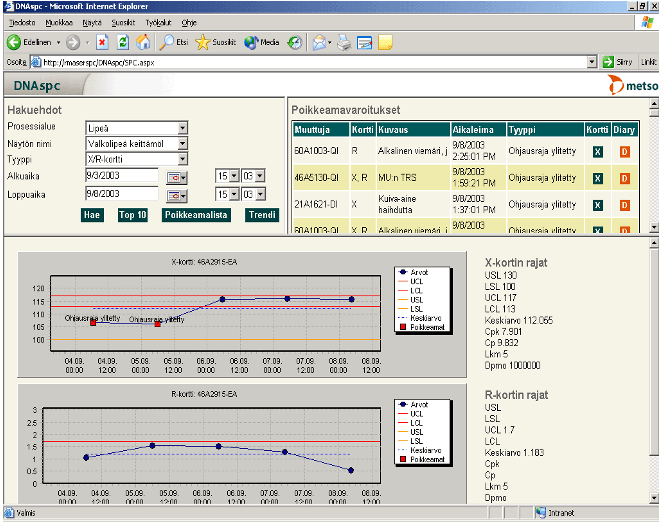
”Taulut” siirtyivät valvomon näyttöihin ja saivat enemmän käyrämuotoa. Oleellista oli, että valvomon ohjaimien (säätimien) ohjausrajat oli aikaisemmin perustuneet speksirajoihin ja toleranssirajoihin, jotka eivät huomioi prosessin vaihtelua, vaan perustuvat tuotteen, tässä sellun, spekseihin.
Tämä on tyypillinen yrityksissä tehty virhe. Siirretään tarkastus ja speksirajat (Inspection limits), jotka koskevat ”mennyttä” tulevaisuutta ohjaaviksi ohjausrajoiksi (Control Limits). Speksirajat ovat siis ”subjektiivisia” rajoja, jotka ovat tavoitteita, jotka asettavat vaatimuksen prosessin suorituskyvylle. Menneisyyden rajat ovat eri asia kuin tulevaisuutta ohjaavat ja stabiloivat ohjausrajat. Näiden perusteella ei saa ohjata prosessia, kuten ensimmäisessä artikkelissa on kuvattu. Jos ohjauksen tekee subjektiivisten rajojen mukaan, epästabiilisuus ja vaihtelu kasvaa niissä tapauksissa, joissa speksirajat ja SPC-rajat poikkeavat toisistaan. Säätö (adjust) ja ohjaus (control) sekoitetaan usein toisiinsa. Säädöllä muutetaan keskiarvoa ja ohjauksella vaikutetaan vaihteluun.
Laatutaulun sijaan voidaan puhua Metsä Botnialla multiSPC:stä tai variaaabeli SPC:stä. Kortteja oli paljon rinnakkain. Sellun valmistuksessa mittarit ovat jatkuvia (mm. lämpötila, paine, pH). Nämä vastaavat pitkälti laatutaulussa olevia virheiden ilmenemismuotoja, joissa lukumäärän sijaan on mitatut tulokset eli variaabelimuuttujat. (Lukumäärä on attribuutti muuttuja). Koska mittarit ovat jatkuvia, niihin voidaan soveltaa jatkuvien muuttujien SPC-teoriaa.
Tulokset laatutaulusta (multiSPC)
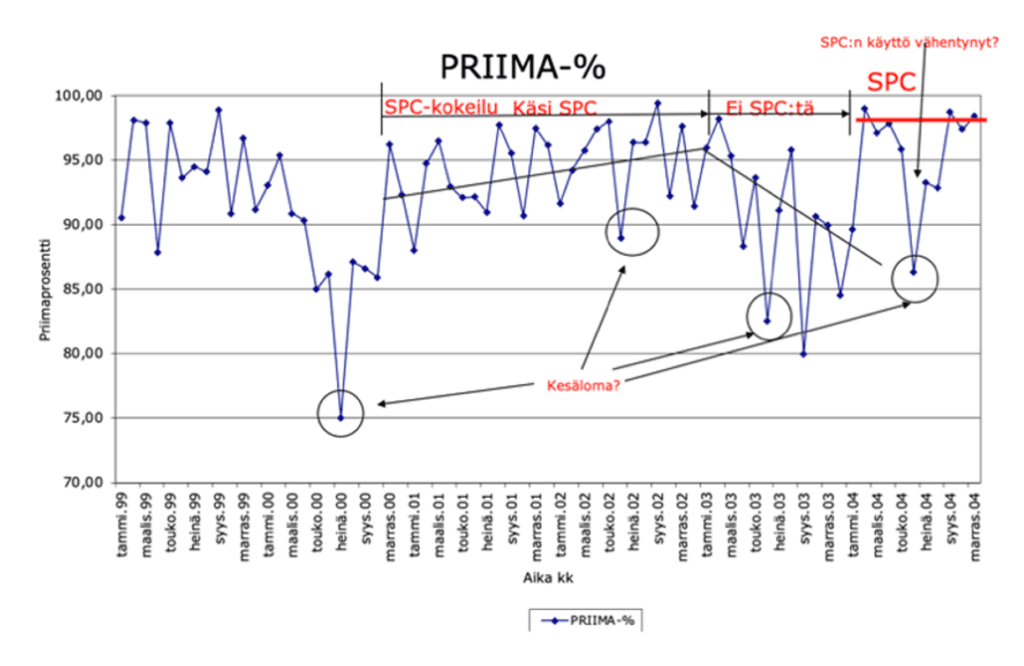
Kuvasta 26 nähdään ennen SPC:tä vallinnut kuukausitason priiman osuus. (Priimalle oli tarkat numeeriset speksit, joita yritettiin ohjata speksirajoilla.) Sellutehdas käynnistyi vuonna 1996. Priiman osuus oli laskussa. Miksi?
Luontaisesti ammatti-ihminen ei osaa erotella datasta erityissyytä ja satunnaissyytä toisistaan ja tapahtuu yliohjaus eli tampering (peukalointi). Priiman laskuun syy oli siis tamperointi.
Käsin tehty SPC-laskenta ja tulkinta (syyskuu 2000-tammikuu 2003) ennen kuin Metso Automaation DNA-järjestelmää paransi tilannetta. Tammikuussa 2003 käsin tehdyistä rajoista luovuttiin, kun henkilöstö kuuli automaation valmistelusta. Välittömästi laatu alkoi laskea. Palattiin vanhaan ”ammattikäytäntöön”!
Tammikuussa 2004 annettiin SPC n ja DNA:n koulutus ja käyttö alkoi. Laatu hyppäsi ”ylös” ja paremmaksi kuin koskaan. Kesälomien jälkeen ei katsottu tarvittavan SPC:tä ja laatu romahti, kunnes syyskuussa toteutettiin ”virkistys”-koulutus ja järjestelmä otettiin käyttöön ja laatu parani huipputasolle. Näin vaikeaa asian (säätö- ja ohjaustekniikan) ymmärtäminen ja hyväksyminen on!
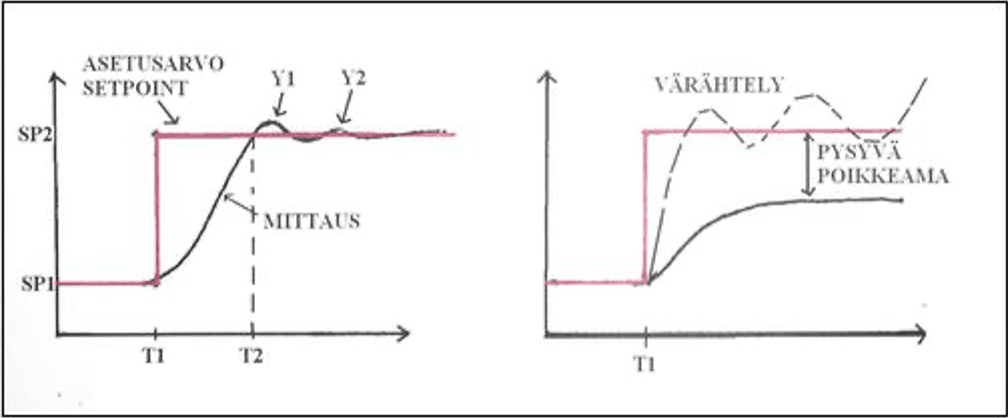
VI. Kehitysvaihe 2010- Lahden Autokori Oy
Kuudennessa kehitysvaiheessa on pyritty ratkaisemaan erityissyihin liittyvää analyysi ja vastuuongelmaa.
Lahdessa on pitkät perinteet linja-autojen korivalmistuksessa. Lahden autokori on perustettu vuonna 1956. Korit rakennettiin Scanian alustalle. Tehdas oli Lahden Villähteellä. Yritys oli Saarion perheen yritys. Yrityksen laatupäällikkönä toimi Jisvi Hyyrynen. Vuonna 2007 valmistui uusi tehdas Lahden Jokimaalle, jossa työskenteli n. 200 henkilöä. Vuonna 2013 tehdas siirtyi Scanian omistukseen ja tuotanto siirrettiin Scanian Puolan tehtaille vuonna 2020.
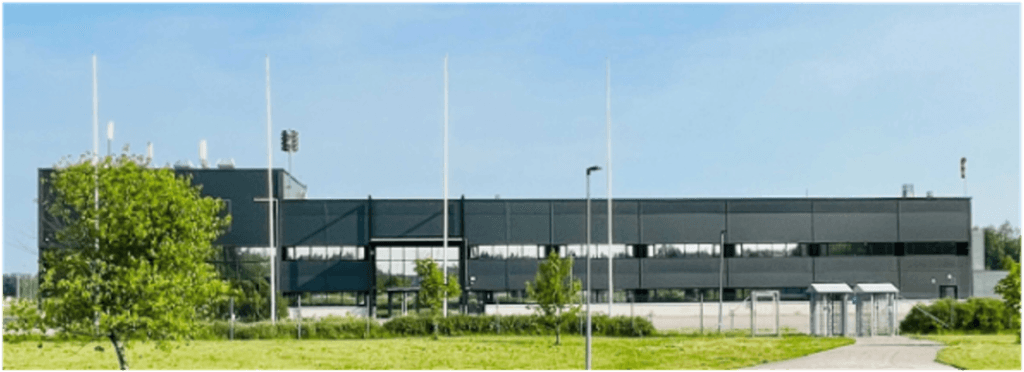
Uuden tehtaan ylösajon ongelmana oli liian hidas tuotantonopeus. Yhtenä keskeisenä syynä hitaaseen tuotantonopeuteen toimitusjohtaja Seppo Saario totesi liian suuret asennusvirhemäärät ja niiden korjaustyö, siis alhainen tuottavuus.
Laatutaulut olivat Lahden alueella tunnettuja ja tunsin entuudestaan Sepon, joten oli luonnollista kokeilla laatutaulujen sopivuutta linja-auton korien valmistuksessa. Keskusteluissa tuli ilmi, että korjausvastuu ja ennaltaehkäisevät toimenpiteet olivat erityinen paino- ja kipupiste kuten autoteollisuudessa yleensäkin. Korjata osattiin, mutta parantaa ei osattu! Virhemäärä pysyi vakiona.
Ongelma: SPC muuntuu helposti vain virheiden ja ilmenemismuotojen kirjaamiseksi. Analyysi unohtuu tai vastuu selvittämisestä ja toimenpiteistä on epäselvä. Jos vastuut ja oikeat vaikuttavat toimenpiteet puuttuvat, ei voi odottaa tuloksia!
Lahden Autokorissa kokeiltiin erityistä laajennettua laatutaulua, jossa on SPC, ohje sen käyttämisestä, 5 x Miksi -tekniikka (juurisyyanalyysi) ja vastuutaulukko, johon kirjataan toimenpide, vastuuhenkilö ja toimenpiteen suorittamispäivämäärä. Lahden Autokori valmisti Scanian alustalle linja-autoja.
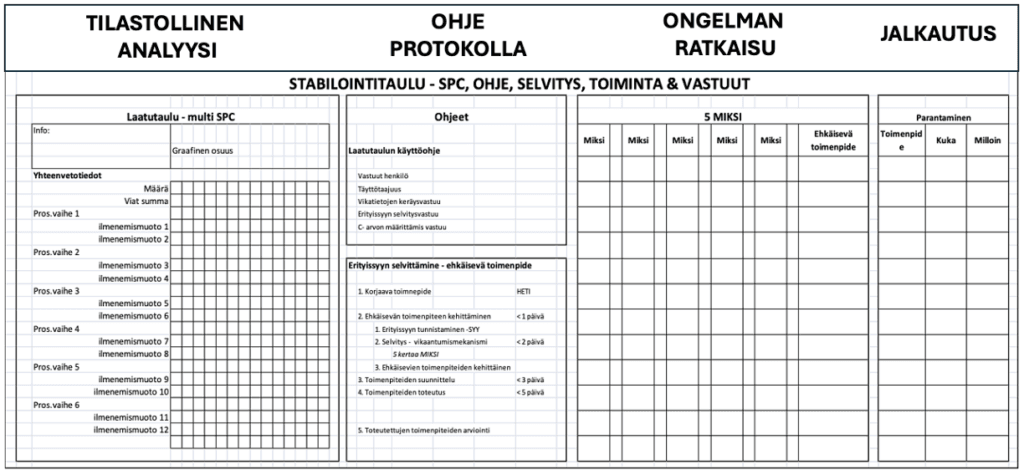
Taulut oli sijoitettu keskelle kokoonpanolinjaa.
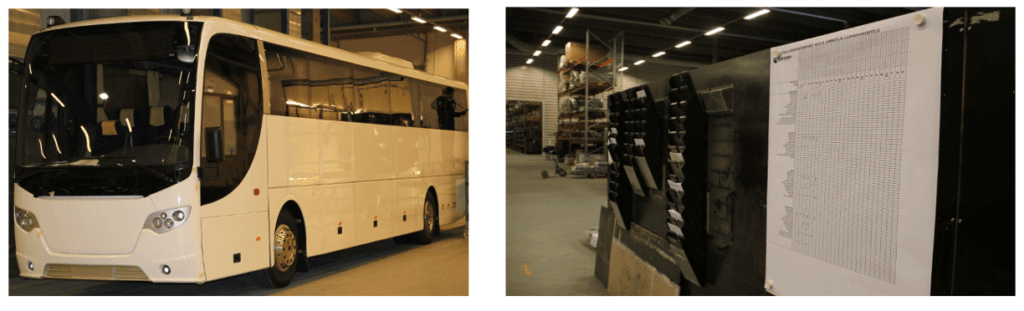
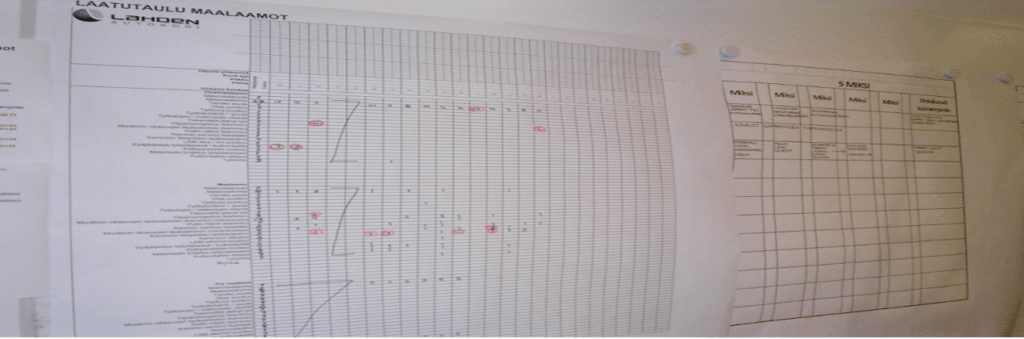
b) Tulokset laatutaulusta
Laatutaululla saavutettu kehitys vuosina 2011-2012. Virhemäärä pudonnut lähes 80 % vuodessa. Kokonaisvirhemäärä, josta lähdetiin oli n. 1200 virhettä/viikko tai enemmän linjalta, jossa valmistui 5-10 linja-auton koria viikossa. Kysymys on siis löydetyistä ja kirjatuista virheistä. Vuositasolla virheitä oli aloitettaessa n. 60 000 kpl/vuosi/100 työntekijää.
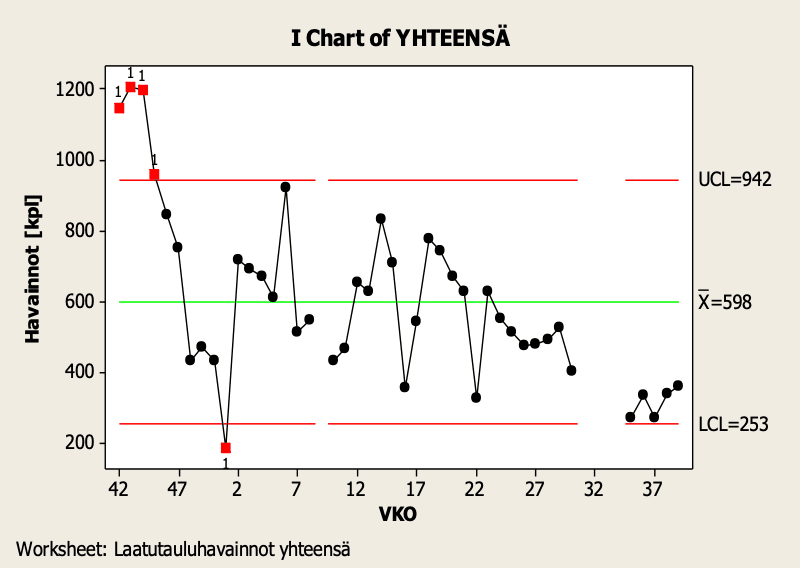
Lahden Autokorilla laatutaulua opastettaessa ja käytettäessä korostettiin ja ohjeistettiin seuraavilla säännöillä:
Laatutaulujen virhedatan keräämisessä on erityisesti korostettava seuraavaa:
- Kaikki havaitut virheet merkitään “tukkimiehen” kirjanpitoa hyväksikäyttäen tai normaalein numeroin keräilylomakkeille, joista linjavastaavat kirjaavat tiedot laatutaululle joka päivä.
- On tärkeää, että virhe tulee merkittyä oikeaan prosessivaiheeseen, vaikka henkilö työskentelisi muissa vaiheissa.
- Jokainen merkitsemättä jäänyt virhe merkitsee menetettyä mahdollisuutta parantaa työsuoritusta, menetelmää, materiaalia, laitteita ja / tai ympäristöä.
- Mikäli listalta ei löydy sopivaa virhenimikettä, kirjoitetaan ko. virheellisyys tyhjään tilaan oikean prosessivaiheen kohdalle (etenkin taulun käyttöönoton alkuvaiheessa tätä on syytä korostaa).
- SPC on laadun perustyökalu tutkittaessa vaihtelua ja käytettäessä tilastollista signaalia monitoroimaan ja parantamaan suoritusarvoa. (menetelmää, ammattitaitoa)
- Laatutaululla parannetaan systeemiä ja prosessia. Tarkoituksena ei ole etsitä syyllisiä.
- Vaihtelun tunnistaminen ja pienentäminen vaatii tilastollisia menetelmiä la laatuteorian. Pelkkä virhe- ja vikatietojen kerääminen ei auta. Niistä täytyy johtaa oikea-aikaisia toimenpiteitä ja ottaa ne käyttöön prosessissa.
- Laatutaulusta saadun informaation pitää johtaa välittömiin toimiin erityissyiden poistamiseksi. Mikäli tämä protokolla ei toimi ja jos virheraportointi ei johda konkreettisiin parannustoimiin, niin se johtaa työtekijöiden kyllästymiseen laatutaulujen ylläpidossa.
- Protokolla sisältää: Vastuuhenkilön, käyttötaajuuden, vikatietojen keräysvastuun, erityissyyn selvitysvastuun ja C-arvon (hälytysraja SPC-kortissa) määrittämisvastuun.
2. Yhteenveto kehitysvaiheista
Laatutaulua kehitettäessä lähdettiin liikkeelle 1970-luvun lopussa yksinkertaisesta visuaalisesta taulusta, johon prosessissa olevien virheiden ilmenemismuodot (huom. ei syitä) on kirjattu taulukkomuotoon esiintymistaajuuden/lukumäärän mukaisesti vuoro, päivä ja kuukausitasolla (eri raportit).
Nämä prosessissa olevat ilmenemismuodot ovat tuotteen tai palvelun ”inputteja”, joita on ohjattava. Laatutauluja voi verrata yrityksen kirjanpitoon. Kirjanpidossa ei tyydytä vain tulojen ja menojen kuukausi ja vuosisummiin, vaan kaikki tulot ja menot tiliöidään eli luokitellaan. Laatutaulussa muodostetaan eri virheiden, vikojen ja hukkien ilmenemismuodoista rivit (tilit), joita analysoidaan kutakin erikseen tilastollisesti. Data saadaan työntekijöiden keräämistä listoista päivittäin.
Jaksotustekijä vuoro/päivä/viikko/kuukausi muodostaa kappalemääristä taajuuden.
Muutokset, joita on viimeisten 40 vuoden aikana tehty laatutauluihin, ovat perustuneet haluun parantaa laatua ja vähentää virheitä ja hukkaa mahdollisimman tehokkaasti ja nopeasti minimiresurssein.
Erilaisia yritelmiä ja muutoksia on tehty kymmeniä eri organisaatioissa ja näistä on siivilöitynyt vuosien kuluessa ehkä 10-100 kertaa tehokkaampi menetelmä lähtötasoon verrattuna.
Ensimmäinen suuri muutos oli, kun raportointia laajennettiin johto- ja päällikkötasolta työntekijätasolle ja raportin kokoa samalla kasvatettiin A4:stä A0:aan. Myös laadussa siirryttiin valvonnasta ohjaukseen ja informaation kulkusuunta muutettiin työntekijästä johtajaan, valvottavasta valvojaan.
1990-luvun taitteessa raportointi muutettiin SPC-pohjaiseksi käyttämällä Poisson-jakaumaa ja etukäteen induktiivisesti määritettyjä ohjausrajoja deduktiivisesti määriteltyjen toleranssirajojen ja speksien sijaan.
Kempin aikana käytettiin ohjausrajoja (SPC), mutta niitä ei merkitty eikä myöskään yleisesti koulutettu ja selitetty työntekijöille. Pelkona oli mystiset numerot ja numerologia. Julkisissa tauluissakin oli ”kestämistä”!
Laatutaulujen myötä siirryttiin tarkastuksesta ja valvonnasta (reaktiivinen) ohjaukseen ja ennaltaehkäisyyn (proaktiivinen).
Tämä konseptivaihto ja SPC-laajennus tarkoitti systeemitason lähestymistapaa, jossa virheet ja hukat, poikkeamat toleranssien/speksien ulkopuolella, jaettiin niiden ilmenemismuotojen esiintymisen taajuuden mukaan erityissyyperusteisiin ja satunnaissyyperusteisiin ilmiöihin.
Erityisen vaikea tässä konseptivaihdossa oli reklamaatioiden (output) käsittely. Yksittäisen reklamaation perusteella ei voi tehdä muuta kuin korjaavan toimenpiteen itse tuotteeseen tai palveluun, mutta ei ohjaus- ja parannustoimenpidettä.
Ohjauksen ja parantamisen ”laatuteorian” loi tri Walter A. Shewhart vuonna 1924. Tällä muutoksella (teorialla) estetään yliohjaus ja saadaan yleensä voimakas hyppäyksellinen laatutason parannus (breakthrough) kuten esimerkeistä ilmenee.
Tapahtuu aito systeemin laatutason parannus. Jos tätä jakoa ei tehdä erityissyiden ja satunnaissyiden välillä, virheiden määrä pysyy toimenpiteistä huolimatta samana tai jopa kasvaa.
Ohjauksen ja parannuksen laatuteoria SPC toi todellisen (ei näennäisen) parannuksen yrityksiin! Laajemmin kysymys on ohjaus- ja säätötekniikan soveltamisesta systeemi- ja prosessitasolla.
Menetelmän käyttö toi mukanaan myös ”laadun parannuksen väsymyksen” (Quality improvement fatigue). Hyväksi havaittua menetelmää ei jakseta noudattaa ja palataan siihen vanhaan. Syynä on usein henkilöstön vaihtuminen. Uusille henkilöille ei opeteta laadunparannuksen keskeisiä menetelmiä ja tässä tapauksessa laatutaulua – mihin perustuu, kuinka toimii ja millaisia tuloksia on saatu.
1990-2000-luvulla tuli yleisesti käyttöön erilaisia selainpohjaisia ohjelmistoja helpottamaan rajojen laskentaa ja esittämistä. Taulut siirtyivät osin tietokoneille. Oli hyviä ja huonoja kokemuksia! Ohjelmistojen käytöstä tulee itsetarkoitus ja toimenpiteet unohtuvat. Toisaalta Six Sigma (ja Minitab-ohjelmisto) mahdollisti tehokkaan satunnaissyiden eli systeemisyiden selvittämisen (DMAIC). Aikaisemmin 1960-70 -luvulla ei ollut keinoa parantaa systeemiä!
2010-luvulla on pyritty tehostamaan analyysi- ja selvitystoimintaa, josta esimerkkinä Lahden Autokorin laatutaulut.
Laatutaulu ”puhdistaa” erityissyyt muutamassa kuukaudessa ja stabiloi prosessin, jonka jälkeen satunnaissyiden osuus tulee vallitsevaksi ja tarvitaan laatutaulujen rinnalle Lean Six Sigma tai vastaava menetelmä systeemin ja prosessin suorituskyvyn parantamiseen.
Lähteet:
- Artikkeli: Tilastollinen ymmärrys ja käyttö, 2024
- Artikkeli: Laatutaulu: virheet ja hukka – teoriasta käytäntöön: Osa 1, 2024
- Artikkeli: Laatutaulu: kehitysvaiheet I-II – teoriasta käytäntöön: Osa 2, 2024
- Artikkeli: Jatkuvasta tarkastuksesta ja korjauksesta jatkuvaan parantamiseen tai sitten ei?, 2021
- Michael Greif: The Visual Factory, 1991
- Armand V. Feigenbaum: Total Quality Management, 3rd Edition, 1991 (1951)
- Eero E. Karjalainen, Tanja karjalainen: Laatutaulu – Tehokas menetelmä laadunohjaukseen ja paranukseen, 2024
- Artikkeli: Asiakaslähtöinen tuotekehitys (QFD), 2015
- https://qkk.fi/wp-content/uploads/2024/12/leanjalsstalo.png
- Wikipedia: Laatupiiri – Quality circle, https://en.wikipedia.org/wiki/Quality_circle
- SFS standardi 4360 Laatutekniikka, x- R valvontakortit (1981)
- https://qkk.fi/tuote/spc-2nd/
- Taina Savolainen: Development of Quality-Oriented Management Ideology. 1997
- Kalevi Laalo – Reino Rajamäki: Murros työelämässä, 2008
- EEK:n muistiinpanot ja projektipöytäkirjat (Stala, Eimo, Halton, Metsä Botnia, Lahden Autokori)
Tutustu kurssitarjontaamme!
Tilaa uutiskirje
Liity postituslistalle ja saat uusimmat artikkelit suoraan sähköpostiisi.
Tämä lomake on suojattu Google reCAPTCHA:lla. Lue tietosuojaseloste ja käyttöehdot.
Liittymällä postituslistalle hyväksyt Quality Knowhow Karjalainen Oy:n tietosuojaselosteen ja Quality Knowhow Karjalainen Oy voi lähettää sinulle ajankohtaisia artikkeleita, videoita sekä tietoa ja tarjouksia kursseista, kirjoista sekä ohjelmistoista.
Tämä lomake on suojattu Google reCAPTCHA:lla. Lue tietosuojaseloste ja käyttöehdot.