Hävikki (loss) ja hukka (waste) ovat kaksi tuttua termiä, mutta ovatko. Sanoja käytetään useissa yhteyksissä. Laadun ja tuottavuuden kehittämisen yhteydessä sana hävikki juontaa juurensa Tohtori G. Taguchiin. Hän kehitti hävikkifunktion, joka kuvaa hävikin syntymistä poikkeaman neliönä. Tällä kertaa en keskity tämän perusteluun. Lyhyesti sanottuna hävikki syntyy poikkeamasta. Tämä voi olla mikä tahansa poikkeama sovitusta suunnitellusta tavoitteesta, joka tulee saavuttaa.
Hukka-sanalla viitataan menetettyyn aikaan, joka voi näkyä myös ajan toisena muotona varastona (tai voidaan myös kutsua termillä bufferi). Leanin yhteydessä tämä hukka luokiteltiin seitsemään eri muotoon. Kaikilla näillä muodoilla on yhteys hävikkiin. Systeemissä ei ole selvää syytä ja seurausta, mutta usein hukka on seurausta hävikistä. Tämä artikkeli käsittelee tätä aihetta.
Hävikin ja hukan käsittely prosessissa
Ajatellaan, että meillä on yksinkertainen tilanne – prosessi – missä työ suoritetaan kahdessa vaiheessa ja näiden välissä voi olla varasto tai odotus. Työn suorittaminen tuottaa asiakkaalle arvoa tuotteen tai palvelun muodossa.

Avuksi tarvitaan apulaitteita/-koneita, jotka muodostavat asiakkaan kannalta monia tärkeitä ominaisuuksia. Laatutieteessä näitä ominaisuuksia kutsutaan ominaispiirteiksi (characteristic), joista asiakas on valmis maksamaan enemmän kuin niiden tuottaminen maksaa. Asiakas ja tuottajat saavat siis ominaispiirteistä arvoa (value).
Jos prosessin jommassa kummassa tai molemmissa vaiheissa tapahtuu jokin ongelma – poikkeama sovitusta – alkaa syntymään hävikkiä ja hukkaa:
- Kone tai laite ei tuota ominaispiirrettä oikein -> laatu laskee
- Ei ole saatavilla materiaaleja, raaka-aineita -> keskimääräinen valmistumisnopeus laskee
- Kone rikkoutuu -> tuotetta ei valmistu ja valmistumisnopeus hidastuu
- Työntekijä ei tee ominaispiirrettä oikein -> laatu laskee
- Samaa työtä ei voi jatkaa koko ajan, tulee työn vaihto -> nopeus laskee
- Koneita laitteita tulee huoltaa -> keskimääräinen valmistumisnopeus laskee

Tätä listaa voisi jatkaa vaikka kuinka pitkälle. Kaikki nämä aiheuttavat hävikkiä työnsuorittamisen vaiheessa ja nämä voidaan luokitella kuudeksi isoksi hävikiksi (Six Big Loses). Nämä kaikki hävikit kasvattavat keskimääräistä ominaispiirteen muodostamisaikaa. Tuotteen tai palvelun muodostumiseen kuluvaa aikaa ideaalitilassa kutsutaan raa’aksi prosessiajaksi (raw process time) tai prosessointiajaksi (natural process time). Kun jokin kuudesta hävikistä kasvattaa tätä aikaa, syntyy teholliseksi ajaksi (effective process time) kutsuttu aika. Tämä tehollisen ajan kasvu sekoitetaan usein jaksoaikaan, joka toki kasvaa, mutta on eri kuin tehollinen aika.
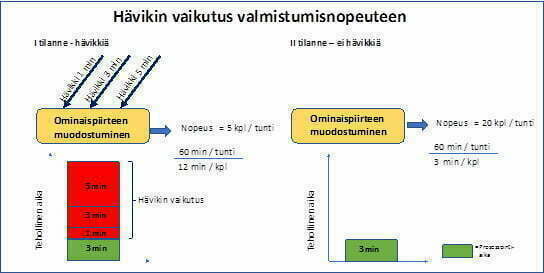

Samalla, kun ominaispiirteen luomiseen tulee ongelmia, prosessivaiheen eteen kertyy työtä tai jäljelle jäävät työt jäävät odottamaan työn alle pääsyä. Jos nämä kaksi prosessivaihetta on kytketty toisiinsa, pysähtyy toinen vaihe aina kun toiseen tulee ongelma (ellei varastoa ole välissä syntyy odotushukka ja päinvastoin).
Hävikki tapahtuu prosessissa ja se aiheuttaa hukkaa. Toiminnan kehittämisessä on marssijärjestyksen oltava selvä. Jos ei ole, ammutaan haulikolla ympäriinsä ja toivotaan, että saadaan aikaan tulosta.
Usein tavoitteena on tuottaa parempaa tuotetta tai palvelua asiakkaalle paremmalla teholla. Tämän vuoksi tehollisen ajan analyysi hävikkilähteiden suhteen on tärkeää ja samalla saadaan selvitettyä, mikä aiheuttaa hukkaa tai lisähukan tarvetta.

Opettelemalla tärkeitä ja kaikkien opittavissa olevia menetelmiä nostat omaa ja organisaation kykyä kehittää toimintaan. Luin jouluvapailla kirjan tunnetun lääkärin ja luennoitsija Hans Roslingin Faktojen maailma. Siinä hän korostaa, että älä koskaan tarkastele yksittäistä lukua tai asiaa. Vertaa lukua AINA johonkin, jaa se jollakin ja muista 80/20 -periaate (Pareto). Sama koskee kehitystä – haluat varmasti tulosta etkä tekemistä – ymmärrä mihin pienoiset resurssit pitäisi laittaa.
Osaaminen ja uusien kysymysten esittäminen analyysiä varten on tärkeää ennen toteutusta, toteuta vasta tämän jälkeen.
Lähteet:
- Taguchi, G., Chowdhury, S. & Wu, Y. 2005. Taguchi´s Quality Engineering Handbook. Wiley
- Antti Piirainen: Vaihtelu, 2014, Quality Knowhow Karjalainen Oy
- W. J. Hopp, M. L. 2008. Spearman, Factory Physics, Third Edition
Tilaa uutiskirje
Liity postituslistalle ja saat uusimmat artikkelit suoraan sähköpostiisi.
Tämä lomake on suojattu Google reCAPTCHA:lla. Lue tietosuojaseloste ja käyttöehdot.
Liittymällä postituslistalle hyväksyt Quality Knowhow Karjalainen Oy:n tietosuojaselosteen ja Quality Knowhow Karjalainen Oy voi lähettää sinulle ajankohtaisia artikkeleita, videoita sekä tietoa ja tarjouksia kursseista, kirjoista sekä ohjelmistoista.
Tämä lomake on suojattu Google reCAPTCHA:lla. Lue tietosuojaseloste ja käyttöehdot.