Parannusmenetelmän valinta on ollut kautta aikain keskeistä.
Quality Engineering -lehdessä 1/2014 on erinomainen artikkelisarja, jossa esitellään ”The First Stu Hunter Research Conference” tuloksia. Konferenssi pidettiin 2013 J Stuart Hunterin täyttäessä 90 vuotta. Konferenssin teemana oli ”Stu Hunter’s Contributions to Experimental Design and Quality Engineering”.
Yhtenä teemana tässä konferenssissa oli laadunparannusmenetelmien valintaan liittyvät ongelmat, joita kuvaan tässä artikkelissa.
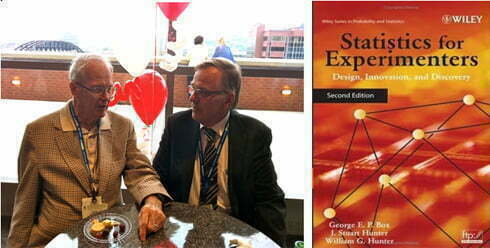
Stu on yksi merkittävimmistä laadun kehittäjistä. Allekirjoittaneella on ollut ilo tuntea hänet ja hänen työnsä vuosien takaa sekä tavata hänet myös henkilökohtaisesti.
Kuinka valita oikea parannusmenetelmä?
Menenkö lääkäriin vai yritänkö hoitaa ”flunssan” kotikonstein? Vai onko minulla sittenkään flunssa vai jokin vakavampi sairaus?
Nämä samat kysymykset voidaan esittää hyvinkin erilaisissa yhteyksissä koskivat ne sitten yksilöä, perhettä, yhteisöä, organisaatiota tai valtiota. Miksi ja miten? On selvitettävä syy ja siihen parannuskeino tai menetelmä tai molemmat. Lääkärit kutsuvat tätä diagnoosiksi.
Juran ja Gryna/1/ esittivät vuonna 1980 kaksivaiheisen prosessin ”Diagnostic Journey” ja ”Remedy Journey” – matka oireesta syyhyn (diagnoosi) ja matka syystä parannukseen (korjaavaan toimenpiteeseen). Mitä ja kuinka?
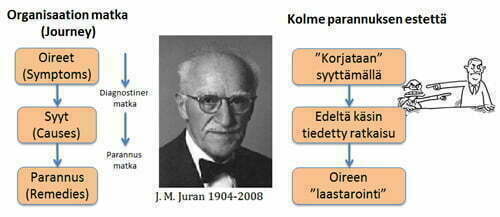
Sen sijaan, että kulkisimme diagnostista tietä kohti parannusta, syyllistymme usein kolmeen parannuksen esteeseen: oireen ”korjaamiseen” syyttämällä muita, esittämään etukäteisratkaisu ennen kuin tiedämme syytä tai käyttämään oireen laastarointia ja sen poispyyhkimistä.
Lean Six Sigma on todettu kaikkein tehokkaimmaksi ongelmanratkaisumenetelmäksi. Se noudattaa yleistä Juranin mallia, joka soveltuu hyvin laajaan kenttään ongelmia, mutta ei kaikkeen. On ongelmia, joihin on syytä soveltaa muita menetelmiä.
Parannuksen valintamatriisi
Professori R. Hoerl ja R. Snee /2,3/ esittävät ongelmanratkaisumenetelmän valintaan kahta dimensiota:
1) tunnetaanko ratkaisu vai ei ja
2) onko ongelmamonimutkainen vai ei.
Näistä kahdesta tekijästä voidaan muodostaa nelikenttä, matriisi.
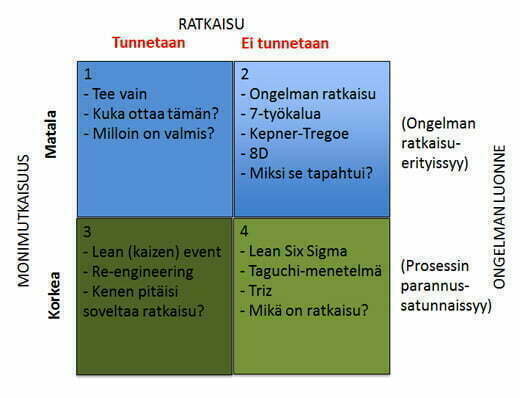
Ongelma, jonka monimutkaisuus on matala, on tyypillisesti eristetty ongelma: ongelman tuntomerkkinä on erityissyy (special cause), joka voidaan havaita SPC/laatutauluyhdistelmällä. Keskeinen kysymys on, mikä meni väärin? Löydämme ”helposti” juurisyyn ja palaamme normaaliin päiväjärjestykseen.
Kun ongelman monimutkaisuustaso on korkea, se koskee yleisesti prosessia, tuotantolinjaa tai koko yritystä (systeemiä) ja on tunnistettavissa SPC:llä satunnaiseksi syyksi (common cause). Ei ole erityissyytä, jonka voi korjata. Asia voidaan myös ilmaista ”yleisenä suorituskyvyn puutteena”, ei erityisenä.
Systeemille tyypillistä on, että kaikki on kaikkien kanssa sidoksissa. Muutat mitä tahansa, muutkin tekijät muuttuvat. Yhtä oikeaa ratkaisua on vaikea löytää toisin kuin erityissyyongelmissa.
Tähän sopii parhaiten Lean Six Sigma.
Ongelmanratkaisutavan valinta (nelikenttämatriisi):
Ratkaisu tunnetaan ja monimutkaisuus on matala: Kun meille tulee tarve parantaa, ensimmäinen kysymys, jonka itsellemme asetamme on, tiedämmekö jo ratkaisun ongelmaan. Tämä on jokapäiväistä toimintaa, jossa toimimme aikaisemman kokemuksen mukaan.
Ratkaisun tietäminen ei kuitenkaan tarkoita, että ratkaisu on helppo tai vähäpätöinen. Meidän jokapäiväinen elämämme ja työmme on täynnä näitä tapahtumia. Oleellista on, kuka ottaa ratkaisusta ”kopin” ja milloin ratkaisu on valmis. Aikaansaamisen ongelma! Johtaminen, organisointi ja työtaidot ovat keskiössä!
Ratkaisua ei tunneta ja monimutkaisuus on matala: Kun ratkaisu on tuntematon, me emme tiedä, miksi meillä on ongelma. Avainkysymys on miksi. Miksi tämä ongelma esiintyy tai mikä on juurisyy?
On olemassa lukuisia tiimiperusteisia ongelmanratkaisumenetelmiä – 7 laatutyökalua, Nokia 7, Kepner-Tregoe, 5 Miksi, 5W1H, A3, 8D – muutaman mainitakseni. Keskeinen kysymys on, miksi ongelma tapahtuu? Tiimityö ja ongelmanratkaisutaidot ovat keskiössä enemmin kuin ”raaka” toteutus!
Molemmat matalan monimutkaisuuden ongelmat ovat erittäin tärkeitä organisaation selviytymiselle. Valitettavan usein tunnettu ja tuntematon ratkaisu sekoittuvat toisiinsa ja alkaa syyllisen etsintä ja väittely ratkaisusta, jonka kompromissina on ongelman laastarointi ratkaisun sijaan. Selvät pelisäännöt ja ratkaisuja hakeva mielenlaatu ovat tärkeitä, jotta parannusta estävät voimat eivät pääse vallalle.
Kun ongelman monimutkaisuus kasvaa, sovellutuksen ja ratkaisun hakeminen tulee yhä vaikeammaksi. Kahden aikaisemman menetelmän Win-Win muuttuu helposti Win-Lose – tilanteeksi, jossa parannus johtaakin huonompaan. Käsittelemme systeemiä.
Kuinka tiedämme, että meillä on monimutkainen ongelma?
Ratkaisu tunnetaan ja monimutkaisuus on korkea: Monet Lean -ongelmat ovat erittäin monimutkaisia, mutta ratkaisu on tunnettu. Jos esimerkiksi keskeneräinen varasto (WIP) on suuri ja estää nopean läpimenon, niin ratkaisu on tunnettu – alennetaan keskeneräistä varastoa! Mutta, kuten useat varmaan tuntevat Littlen lain, joka sitoo läpimenon TH (kpl/h), keskeneräisen tuotannon WIP (kpl) ja jaksoajan CT (h) toisiinsa: TH=WIP/CT. Varastoa WIP pienennettäessä yrityksen tuotanto romahtaa ja kapasiteetin käyttöaste laskee! Leanista tai vaikka Kanbanista luovutaan. Win-Lose.
Lähes kaikki Lean -työkalut ovat ratkaisuja, jotka ovat monimutkaisin sidoksin liittyneet toisiinsa, jotka toimivat vain tietyissä hyvin rajatuissa olosuhteissa. Niinpä yleensä ”lohdutetaankin” leania soveltavia, että Lean -työkalu nostaa ongelmat esille? Jos ei tarkoin tiedä ja tunne olosuhdetta ja menetelmän sopivuutta, voi tulos olla katastrofi. Tätä kuvaa Lean -projektien onnistumisprosentti 3-5%. Tarvitaan vahvaa Lean-koulutusta. Toyotalla Senseiksi pääsy kestää vuosia.
Tähän samaan ryhmään kuuluu erilaiset dietit, joissa painoa yritetään pudottaa erilaisilla ratkaisuilla! Yleensä ratkaisun seurauksena paino nousee?!
Ole huolellinen soveltaessasi ”ratkaisua” systeemiin. Varmista, että se todella toimii. Tarvitset lukuisia mittareita. Puhutaan 50+ mittaristosta.
Ratkaisua ei tunneta ja monimutkaisuus on korkea: Kun ongelma on monimutkainen ja ratkaisu on tuntematon, on ensin haettava diagnostisella prosessilla (matkalla) juurisyyt ja syiden ja syyrakenteen löytymisen jälkeen tähän ratkaisu.
Tätä useampivaiheista prosessia sanotaan perättäiseksi eli sequentiaaliseksi ratkaisumenetelmäksi, josta Stu Hunterin konferenssissa monet argumentoivat.
Parhaiten tämä toteutuu Lean Six Sigmassa, jossa viiden vaiheen ja parinkymmenen työkalun voimin haetaan ratkaisu satojen parametrien joukosta ja pyritään välttämään ei-ratkaisu, jotta todella saadaan win-win eikä win-lose. Tässä onnistutaan nykyisin n. 80-90 % tapauksia. Kiitos informaatio-/tilastotekniikan ja Minitabin.
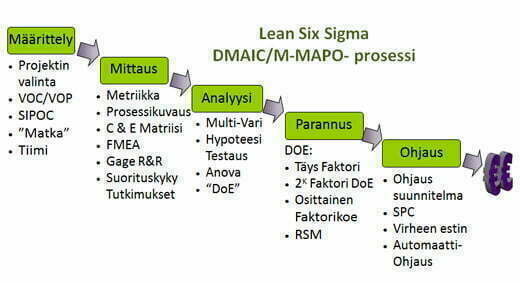
Edellä esitetty ongelmaratkaisun valintamatriisi ei suinkaan ole täydellinen, vaan antaa viitteen siitä, mitä on otettava huomioon valittaessa lähestymistapaa.
Tärkeää on hahmottaa, onko ratkaisua olemassa vai ei ja onko ongelman monimutkaisuus korkea vai matala. Monimutkaisuuteen saa ”vinkin” selvittämällä (SPC/laatutaulu), onko kyse erityissyystä vai onko kyseessä satunnainen koko systeemiä koskeva ongelma. Lääketieteessä jako on akuutti sairaus ja krooninen sairaus. Lähes sama sisältö kuin insinööritieteissä erityissyy ja satunnaissyy.
Toinen mahdollisuus on tarkastella menetelmiä ja niiden soveltuvuutta kohteen, riskin, hyödyn ja vaikeusasteen mukaisesti. Taulukko (2) on J. M. Juranin ja J. A. DeFeon klassisessa laatukäsikirjassa Juran’s Quality Handbook(2010).

Yhteenveto
Parannuksen tarve on aina läsnä kaikkialla – kotona, yrityksissä ja yhteisöissä ja tulee jatkumaan ikuisesti. Elämme dynaamisessa maailmassa, jossa termodynamiikan toinen laki ja entropia vallitsee. Maailma muuttuu jatkuvasti ja epäjärjestys lisääntyy systeemissä. Järjestystä on aina nostettava, parannettava tuomalla systeemiin järjestystä ja ”energiaa”.
Tämä muutos tuottaa tarpeen parantaa. Osaan kohteista tunnemme ratkaisun ja osa ratkaisuista on tuntemattomia, jolloin ne on ”kaivettava” esiin.
Ongelmat, kuten sairaudetkin, ovat osin eristettyjä, akuutteja, joihin ratkaisu on ”helposti” löydettävissä ilman sivuvaikutuksia (win-win), kun taas osa on organisaation tai yksilön ”elintapa”sairauksia koskien koko systeemiä. Systeemin parannuksessa vaarana on sivuvaikutukset (win-lose), jotka voivat olla hyvinkin yllättäviä.
Systeemien, laajojen kokonaisuuksien ratkaisemisessa tarvitaan moninaisia keinoja ja menetelmien yhdistelmiä, kuten Lean Six Sigma. Kun systeemiongelma (syyt) löydetään ja saadaan ratkaistu, myös palkkio on sen mukainen (25/1-100/1). Koesuunnittelu, experiment, on systeemiparannuksen keskiössä.
Tutkimustyö tuo yhä lisää ymmärrystä laajojen prosessien hallitsemisesta yhdessä tietotekniikan kanssa, joka mahdollistaa informaation tehokkaaan keräämisen, yhdistämisen, analysoinnin ja jakamisen.
Lähteet:
1. J. M. Juran ja F. M. Gryna : Quality Planning and Analysis, 2nd ed. 1980
2. Roger W Horel: Discussion of ”Statistical Engineering and Variation”; Quality Engineering, vol 26, 1/2014
3. Roger W. Hoerl ja Ronald D. Snee: One Size Does Not Fit All – Identifying the right improvement metodology, Quality Progress, May 2013
4. J. M. Juran, J. A. DeFeo: Jurans´Quality Handbook – The complete Guide to Performance Excellence, sixth edition (2010)
Tilaa uutiskirje
Liity postituslistalle ja saat uusimmat artikkelit suoraan sähköpostiisi.
Tämä lomake on suojattu Google reCAPTCHA:lla. Lue tietosuojaseloste ja käyttöehdot.
Liittymällä postituslistalle hyväksyt Quality Knowhow Karjalainen Oy:n tietosuojaselosteen ja Quality Knowhow Karjalainen Oy voi lähettää sinulle ajankohtaisia artikkeleita, videoita sekä tietoa ja tarjouksia kursseista, kirjoista sekä ohjelmistoista.
Tämä lomake on suojattu Google reCAPTCHA:lla. Lue tietosuojaseloste ja käyttöehdot.