Laatutaulu: Poikkeamatietojen analysointi ja toimenpiteet ja tuloksia – teoriasta käytäntöön
Laatutaulun analysointi perustuu poikkeamien (virheiden, vikojen, hukkien) jakamiseen kahteen taloudelliseen luokkaan, nimeltään erityissyyperusteiset ja satunnaissyyperusteiset poikkeamat. Taloudellinen jako tulee tri Walter A. Shewhartin esittämästä ajatuksesta, laatuteoriasta, että ”emme tuhlaa liikaa aikaa ongelmien tarpeettomaan etsimiseen” (1). Tämä taloudellinen jako tapahtuu käytännössä tilastollisella ”mittarilla” ± 3 sigma – kannattaako poikkeaman syytä etsiä vai ei.
Uusi laatuteknologia, Lean Six Sigma, on siirtänyt taloudellista ”rajaa” satunnais-syyperusteisten poikkeamiin suuntaan (2):
- Satunnaisperusteisen ongelman ratkaisun etsimiskustannus on ≈ 10 000 – 1 000 000 € tai enemmän (Lean Six Sigmalla) ja tuotot n. 10 – 30 x panos. Ennen selvitysprojektin alkua tehdään suunnitelmia ja riskilaskelmia mahdollisista parannuskohteista ja arvioiduista taloudellisista hyödyistä ja kustannuksista ja päätetään parannusprojektista. Artikkelissa Suomalainen laatu 2020 on kuvattu yli 2000 projektin tulokset. Lähteessä (2) on kuvattu tarkemmin kansainvälisten ja suomalaisten parannusprojektien tuottoja (sivut 99-104 ja 322-342).
- Erityissyyperusteisen ongelman ratkaisun etsimiskustannus on ≈ 0 – 1000 € ja tuotto tätä suurempi (3 sigma teoria). Tuottoa ei yleensä lasketa!
Satunnaisperäiset (luonnolliset) poikkeamat muodostavat stabiilin, ennustettavan systeemin/prosessin, jonka yksittäistä ratkaisua ei siis kannata ilman taloudellisia perusteita etsiä.
Stabiilisuuden rikkoo erityissyyperusteiset poikkeamat. Näiden erityissyyperusteisten poikkeamien syyt kannattaa ja pitää AINA etsiä ilman tuotos-/panoslaskentaa. Kannattavuuden laskenta ”sisältyy” ±3 sigma rajoihin. Erityissyyperusteiset poikkeamat tuhoavat systeemin ja prosessin ja saattavat sen kaoottiseen tilaan, jolla ei ole ennustettavuutta!
Suuri osa Sinua lähellä olevista poikkeamista on helppo analysoida (jakaa luokkiin) esimerkiksi kehon lämpö. Onko sinulla kuumetta vai ei? Osaat analysoida, jakaa kehon lämmön, normaaliin (satunnaissyy) ja ei-normaaliin (erityissyy) ”ilman” tilastollista työkalua. Heti kun siirrytään tuotteisiin ja palveluihin, vaikeus, analyysivirheet ja kustannukset kasvavat.
Kuinka ”taloudellinen” jako erityissyy- ja satunnaissyyperusteisiin poikkeamiin tapahtuu?
Analysoinnissa käytetään hyväksi luonnossa havaittua harvinaisten tapausten stabiilia jakaumaa, Poisson-jakaumaa ja siihen liittyviä ±3 sigma rajoja. Vertaamalla laatutaulussa esiintyvien päivittäisten, viikoittaisten tai kuukausittain tapahtuvien perättäisten ilmenemismuotojen määriä Poisson-jakaumaan voidaan ilmenemismuodot erottaa toisistaan käyttämällä edellä kerrottua tri Walter A. Shewhartin luomaa tietämyskonseptia, laatuteoriaa (1). Tämä konsepti jakaa poikkeamat taloudellisesti tilastollisella työkalulla. Kysymys on siis laadun taloudellisesta ohjauksesta (Economic Control of Quality…), mutta historiallisten syiden takia tätä kutsutaankin kuitenkin tilastolliseksi prosessin ohjaukseksi (Statisical Process Control), joka pelottaa joitain ihmisiä. Miksi?
Artikkelisarjan toisessa ja kolmannessa osassa on kerrottu, miten laatutauluilla saavutetaan dramaattisia laatutason ja tuottavuuden parannuksia, kun edellä mainittu jako toteutetaan. Artikkeleissa kerrotaan myös, miten laatutaso (ja talous) romahtaa, kun ohjauskortista ja taloudellisesta ohjauksesta (SPC) luovutaan ja uskotaan, että kaikki poikkeamat ovat syntyperältään samanlaisia ja että kaikilla on jokin (juuri)syy, joka voidaan selvittää samalla kustannustasolla. Jos poikkeaman ilmenemismuodon alkuperää ei tunnisteta, ennaltaehkäisy- ja parannustoimenpiteet epäonnistuvat 94 %:n todennäköisyydellä ja onnistuvat vain n. 6 %:n todennäköisyydellä (Deming (8, 9). Tästä seuraa kokonaisuutena virheiden, vikojen, hukkien ja reklamaatioiden kasvu yksittäisistä onnistumisista huolimatta.
Laatutaulun luomisesta ja käyttöönotosta on kerrottu osassa 4. Laatutaulu on keskeinen ennaltaehkäisyn ja parantamisen työkalu, joka pohjautuu tilastolliseen prosessinohjaukseen (SPC, Statistical Process Control tai oikeammin EPC, Economic Process Control) ja jonka juuret loi tri Walter A. Shewhart vuosina 1924 ja 1931. Laatutaulu sopii tapauksiin, joissa prosessista ei saada suoraa mitattua dataa. Tyypillisiä prosesseja ovat tuotanto-, kokoonpano- ja asennuslinjat, palveluprosessit, yritysten hallintoprosessit kuten markkinointi, myynti, laskutus, hankinta, lähetys jne. Kaikki ne prosessit, joita ei ohjata jatkuvilla mitatuilla datoilla. Epäsuora tilastollinen data saadaan henkilöstön havaitsemista ja luokittelemista poikkeamien – virheiden, vikojen ja hukkien – esiintymisdatasta, joka stabiilissa tilanteessa noudattaa Poisson-jakaumaa.
Jatkuville mitatuille datoille (kg, mm, °C) on omat arviointi ja laskentakaavat, joilla SPC-ohjausrajat voidaan määrittää. Taustalla ei ole mitään varsinaista luonnon jakaumaa, vaikka usein mainitaan ”virheellisesti” normaalijakauma. Menetelmä on paljon vaativampi ja monimutkaisempi kuin mitä laatutauluissa käytetään. Mitattujen datojen luokittelu vaatii datan rationaalisen ryhmittelyn ja näytteenoton ja oikeinlasketut/-arvioidut ohjausrajat. Ongelmat liittyvät lähinnä datan autokorrelaatioon ja mittauslaitteiden suorituskykypuutteisiin (resoluutio, stabiilisuus).
Suositeltavia SPC-kirjoja Wheeleriltä: Prof. Donald J. Wheeler: Understanding Variation – the Key to Managing Chaos (2000); Twenty Things You Need to Know (2009); Understanding Statistical Process Control (1992); Advanced Topics in Statistical Process Control – The power of Shewhart´s Charts (1995 ); EMP III – Using Imperfect Data (2006) jne. Katso verkkokauppamme kirjavalikoima!
Mikä on laatutaulu:
Laatutaulu on julkinen isokokoinen taulupari, johon on koottuna valmistusprosessin aikana päivittäin, viikoittain tai kuukausittain havaitut luokitellut poikkeamat. Poikkeamat analysoidaan, diagnostisoidaan ja jaetaan tilastollisesti ohjausrajojen (C-raja) avulla erityissyihin ja satunnaissyihin. Erityissyyperusteisten poikkeamien (ilmenemismuotojen) juurisyyt selvitetään vastuuhenkilön toimesta erityissyytaululla ja tehdään korjaus, ohjaus tai parannustoimenpide. Toimenpide merkitään taululle ja valmistumishetki. Kaikki tämä julkisesti kaikkien koko henkilöstön nähden.
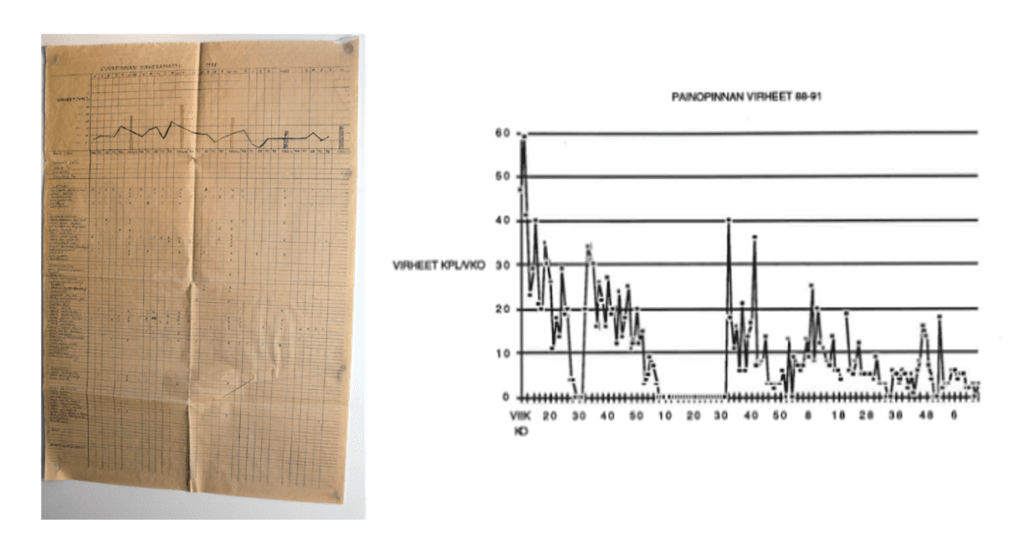
Painopinta on painamista varten tehty ”alusta”, josta tehdään levyt, joilla painokoneessa painetaan kirjojen, lehtien, esitteiden, mainosten ja vastaavien arkit. Painopinnan virhe toistuu jokaisessa valmiissa painotuotteessa. Painopinnan virhe palautuu yritykselle koko erän reklamaationa, josta seuraa ”kotikorjaus” eli kaikki on painettava uudestaan virheettömillä painopinnoilla ja levyillä. Aloitettaessa laatutaulu 1988, painopinnassa oli 50 virhettä/viikko. Vuonna 1993 virheitä oli keskimäärin 1 kpl/viikko (98 % stabilointi, ”parannus”).
Laatuteoria, käytäntö ja kokemukset on koottu myös kirjaamme Laatutaulu – Tehokas menetelmä laadunohjauksen ja parantamiseen, 2024 (10). Laatutauluilla on voitettu Laatupalkinto vuosina 1986, 1990,1991, 2000 (Kemppi Oy, 2 x Stala Oy, Salpausselän kirjapaino Oy). Laatutaulut ja eri versiot ovat käytössä sadoissa yrityksissä ympäri Suomea. Tauluista on tehty myös selainpohjaisia tietokoneversioita erityisesti niissä tapauksissa, joissa syntyy mitattua dataa (multi SPC).
Sisältö:
Johdanto
1. Peruslähtökohdat laatutaululle. Miksi poikkeamadata on analysoitava?
2. Lukujen analysointi
I. Visuaalinen analysointi ”silmällä”
II. Tilastollinen analysointi (C-kortti)
3. Erityissyyperusteisten poikkeaminen toimenpiteet (poisto, korjaus, stabilointi) ja case ”Salpausselän kirjapaino Oy”
4. Satunnaissyyperusteisten poikkeamien toimenpiteet (parantaminen, ennaltaehkäisy) ja case ”Eimo-Muovi Oy, kännykän kuoren mitta”
5. Yhteenveto
Lähteet
Johdanto
Laatutaulun analysoiminen ja johtopäätösten tekeminen tarkoittaa tulevien poikkeamatapausten ennakointia ja parannustoimenpiteitä.
Poikkeaman (virheet, viat, hukat) syntymekanismi on se, joka ratkaisee, mitä voidaan tehdä huomenna tulevalle poikkeamalle – poistaa vai parantaa. Tämä syntymekanismi ei näy poikkeaman ilmenemismuodosta, tavasta, jolla poikkeamaa kuvataan (oire). Asia voidaan kuvata systeemi- ja prosessitasolla. Onko ongelma systeemin ja prosessin ulkopuolinen (voidaan poistaa) vai onko ongelma systeemin ja prosessin sisäinen (voidaan parantaa). Parantamisessa on huomioitava, että parannus vaikuttaa samanaikaisesti kaikkiin systeemin toisiin ominaisuuksiin positiivisesti, neutraalisti tai negatiivisesti. Tämä tekee parannuksesta vaativan.
Tässä ja nyt olevat poikkeamat voidaan joko korjata tai romuttaa ja palvelutuotteissa uusia ja joskus korjata. Näitä toimenpiteitä ei saa sotkea tuleviin tapahtumiin. Korjaus ei myöskään tarkoita, että tulevat tuotteet ja palvelut paranevat tai että korjaukseen liittyy joku ”salainen” tekijä, joka saa muutoksen aikaan huomiseen tilanteeseen.
Reklamaatiot ja asiakasvalitukset: Olen aikaisemmissa artikkeleissa, kursseilla, luennoilla ja Linkedin-keskusteluissa kertonut, että olen lopettanut tai suositellut lopettamaan asiakasvalitusten ja reklamaatioiden selvittämisen lukuisissa yrityksissä. Näissä yrityksissä oli tarkoitus selvittämällä ja tutkimalla ”estää” tulevat valitus- ja reklamaatiotapahtumat (≈ ennaltaehkäisy). En toki ole lopettanut tai suositellut lopettamaan asiakasvalitusten käsittelyä ja korvausten/hyvitysten maksamista. Tämä on eri asia. Asiakas ansaitsee saada aina 100 %:n tuotteen ja palvelun 100 %:n varmuudella sovitussa ajassa!
Perustelut: Asiakasvalituksista ja reklamaatioista johdetut toimenpiteet ovat ulostulo-ohjausta (output)! Tehtävä on liian vaikea, kallis ja vaatii onnistuakseen testin, parivertailun ja kokeen, jolla voidaan huomioida ”kaikki samanaikaiset vaikutukset” (PDSA) (Katso artikkeli: Laatutaulu – Osa 2) – varmistuksen siitä, että ennaltaehkäisy todennäköisesti toimii, eikä aiheuta sivuvaikutuksia muihin ominaisuuksiin. Vertaa lääkkeiden ja rokotteiden testaus. Yrityksissä ei myöskään ole huomioitu asiakasvalitus- ja reklamaatiotutkimusten väärien johtopäätösten, toimenpiteiden ja niiden sivuvaikutusten todennäköisyyttä (> 90 %) ja tämän virheellisen johtopäätöksen seurauksia ja kustannuksia.
Tämän testi, vertailu tai koe on erittäin vaikea toteuttaa etenkin niissä tapauksissa, joissa asiakasvalitus tai reklamaatio tulee kuukausien, vuosien kuluttua mitä ihmeellisimmistä olosuhteista. Testin tai kokeen on oltava monimuuttujakoe ja riittävän laaja, jotta kattaa eri olosuhteet.
Toimenpiteiden ennaltaehkäisyvaikutus jää uskomuksen tasolle ja tutkimus ja toimenpiteet ja sivuvaikutukset todellisiksi yrityksen kuluiksi. Asiakasvalitukset ja reklamaatiot kasvavat ja myös turhat tutkimuskulut kasvavat! Vertaa Demingin arvio (8): 94 % on satunnaisia ja 6 % erityissyyperusteisia.
Tuotteiden ja palveluiden tulevaisuuteen sopeuttaminen tai tulevaisuuden olosuhteiden muuttaminen on uskomattoman vaikeaa, vaikka sinulla olisi ”kaikki” tieto. Vaaditaan kykyä ennustaa oikein. (Katso artikkeli: Kausaliteetti-syy on ehto parannukselle)
Yrityksillä on epärealistinen näkemys asiakasvalitusten ja reklamaatioiden tulvaisuuteen sopeutumisesta ja muuttamisesta (vähentämisestä, parantamisesta) pelkkien reklamaatioselvitysten ja niistä johdettujen toimenpiteiden perusteella. Rahaa ja panoksia laitetaan väärään kohtaan – ja vielä vastoin todistettua taloudellisen ohjauksen teoriaa!
Ratkaisu 1: Tämä ulostulosta ”ohjattu” järjestelmä on korvattava laatutauluilla, joka on välitöntä taloudellista sisäänmenoohjausta (input). Asiakasvalitukset ja reklamaatiot ovat pudonneet murto-osaan aikaisemmasta. Joissain poikkeustapauksissa reklamaatioista (ulostulosta) voidaan laatia oma ohjauskortti, (jos valmistuspäivämäärä ja järjestys on tiedossa), joka ohjaa selvittämistä niihin reklamaatioihin ja valituksiin, jotka ovat erityissyyperusteisia.
Täydennetty ratkaisu 2: Yhdistämällä laatutaulut ja riittävän kyvykäs ja stabiili lopputarkastus, saadaan kustannustehokas varmistettu kombinaatio poikkeamien hallintaan siirtymäajan yli, kun siirrytään erottelevasta tarkastuksesta ja valvonnasta ennaltaehkäisevän ja parantavan laatujärjestelmän suuntaan.
Vanha ratkaisu 3: Kolmas tapa puuttua reklamaatioihin on varmistaa lopputarkastuksen/mittauksen stabiilisuus (10) ja sen kyvykkyys havaita tuotepoikkeamat ((2) sivu 158). Tämä on vanha karsiva ”strategia”, jossa sisäisiä ja ulkoisia virhekustannuksia optimoidaan vähät välittämättä asiakastyytyväisyydestä (vanha laadun optimiteoria, jossa sisäiset virhekustannukset = ulkoiset reklamaatiokustannukset muodostavat minimilaatukustannuksen). Vanhanaikainen ja kallis ja tuottaa huonoa laatua asiakkaille. Lopputarkastusta on erittäin vaikea toteuttaa edes kohtuullisella 95 % karsintakyvyllä ja luotettavuudella niin, että tarkastus ei vuoda virheitä ja vikoja ”epätasaisesti” läpi. (Tarkastus poimisi 95 %:sti virheet ja viat pois tuotevirrasta). Toimii vain yksinkertaisilla tuotteilla ja palveluilla.
1. Peruslähtökohdat laatutaululle. Miksi poikkeamadata on analysoitava?
Jos sotketaan tai erehdytään päätöksenteossa poikkeamien, virheiden, hukkien, häiriöiden vikojen syyn luonteesta, ryhmästä, niin tilanne heikkenee aina niin taloudellisesti kuin säätöteknisesti.
Poikkeaman, virheen, hukan, häiriön tai vian ilmenemisen (=output) syy (=input) voi olla joko
- satunnainen; systeemistä ja järjestelmästä itsestään johtuva. Suurin osa poikkeamista, virheistä, hukista, häiriöistä, vioista (>85 – 99,7 %) on satunnaisia ja systeemi-/prosessiperäisiä. Systeemiperäinen poikkeama on syntynyt lukuisten eri tekijöiden ja näiden yhdysvaikutusten samanaikaisesta vaikutuksesta. Yksittäistä syytä ei voi nimetä. (≈Ei juurisyytä)
- erityisestä syystä johtuva poikkeama, virhe, hukka, häiriö, vika. Vain pieni osa poikkeamista (0,3 – 15%) voidaan selittää erityissyyn aiheuttamalla syyllä, joka voidaan löytää. Erityissyy on systeemin ulkopuolinen tekijä ja näin yleensä eristettävissä. (≈Juurisyy).
- itse aiheutettu suunniteltu muutos tai säätö tai luonnollinen ja systemaattinen vaihtelu, syklisyys. Kesä, talvi; päivä, yö jne. Syy ”itsestään” selvä!
Taulukko 1. Virhepäätökset arkielämässä ja niistä seuraavat tulokset.
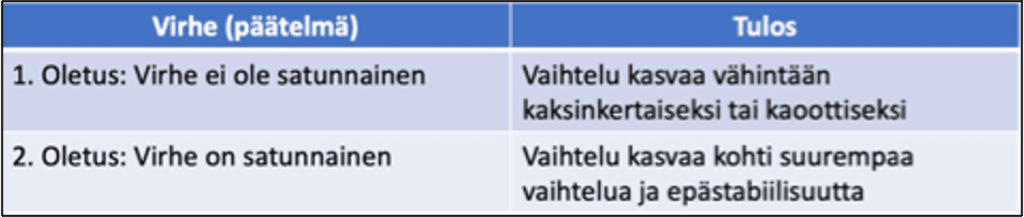
- Yliohjaus tapahtuu, jos oletetaan virheen ilmenemismuodon olevan ei-satunnaisen (on jokin määrätty syy), vaikka todellisuudessa on kysymys satunnaisesta vaihtelusta, ja tehdään toimenpiteitä. Tämä on paljon vakavampi kuin toisin päin.
- Aliohjaus tapahtuu, jos oletetaan virheen ilmenemismuodon olevan satunnaisen, vaikka se onkin erityisestä syystä johtuva, ja ei tehdä toimenpiteitä.
Yliohjaus
Suuri analyysivirhe (yliohjaus) tapahtuu, kun satunnaiset poikkeamat sekoitetaan erityissyyperusteisiin poikkeamiin ja tehdään toimenpide. Poikkeamamäärät kasvavat väärien toimenpiteiden seurauksena tamperointi eli peukalointi (kuva 11 artikkelissa Jatkuvasta tarkastuksesta ja korjauksesta jatkuvaan parantamiseen tai sitten ei?).
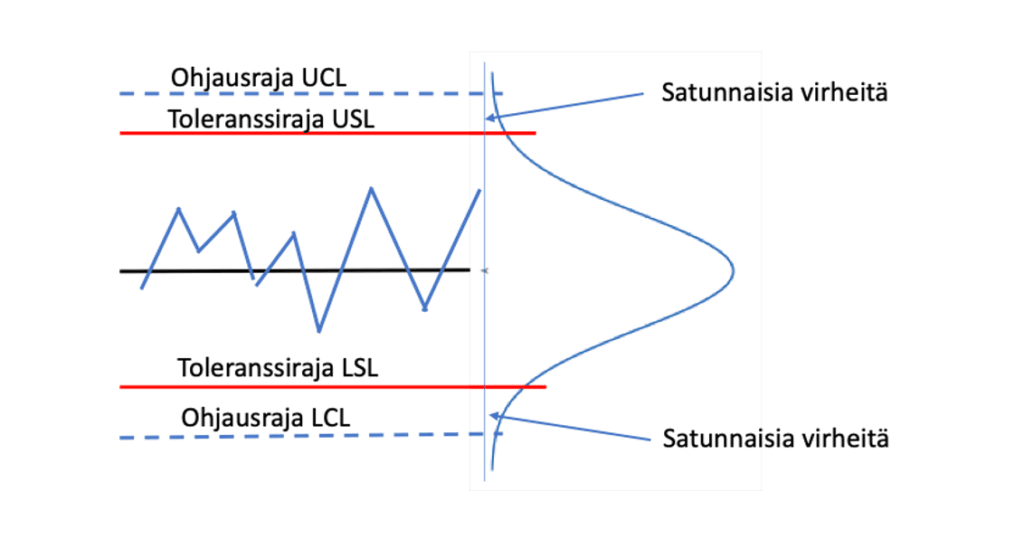
Ongelmaa voidaan pienentää avaamalla speksejä (USL, LSL) kohti ohjausrajoja. Tästä voi olla seurauksena, että tuote tai palvelu ei toimi tai rikotaan asiakaslupaus! Laatutaulumenettelyllä voidaan poistaa ohjausrajan yli menevät stabiilisuutta rikkovat poikkeamat ja valmistella prosessia suorituskyvyn parannukseen. Prosessin suorituskykyparannus siirtää ohjausrajat speksin sisään (Cp>1). Menetelmänä on Lean Six Sigma tai Taguchi-menetelmä, jossa ei haeta syytä, vaan vaikuttavien tekijöiden joukkoa, jolla suorituskyky (kuvan hajontakäyrä) saadaan ”suppuun”. Katso case: Eimo-Muovi Oy, kännykän kuoren mitta.
Aliohjaus
Toinen suuri analyysivirhe tapahtuu, kun erityissyyitä ei voida erottaa todellisista erityissyypoikkeamista (aliohjaus). Aliohjaus tarkoittaa sitä, että poikkeamien havainnointikykyä rajoittaa jotkin tekijät. Aliohjausongelmaa voidaan pienentää ”kiristämällä” tai herkistämällä speksejä (USL, LSL) kohti ohjausrajoja (UCL, LCL). Tästä voi olla seurauksena, että tuote tai palvelu ei toimi, rikotaan asiakaslupaus tai hylky- ja romumäärät ja kustannukset kasvavat. Jotkut johtajat kutsuvat tätä ylilaaduksi. Tehdään parempaa, mitä speksit vaativat! Visuaalisessa tarkastuksessa yleensä valon määrä on ratkaiseva. Työntekijä ei näe poikkeamia. Muita syitä voi olla mittalaitteisiin liittyvät ongelmat – suorituskyvyn puute, liian pieni resoluutio – tai sisäiset normit – kyllä tämä riittää asiakkaalle. Ajan myötä ohjausrajat ryömivät kohti speksirajoja ja yli kohti ääretöntä – ja suorituskyky laskee (entropia vaikutuksesta), jos ei tehdä ohjausrajojen mukaista toimintaa.
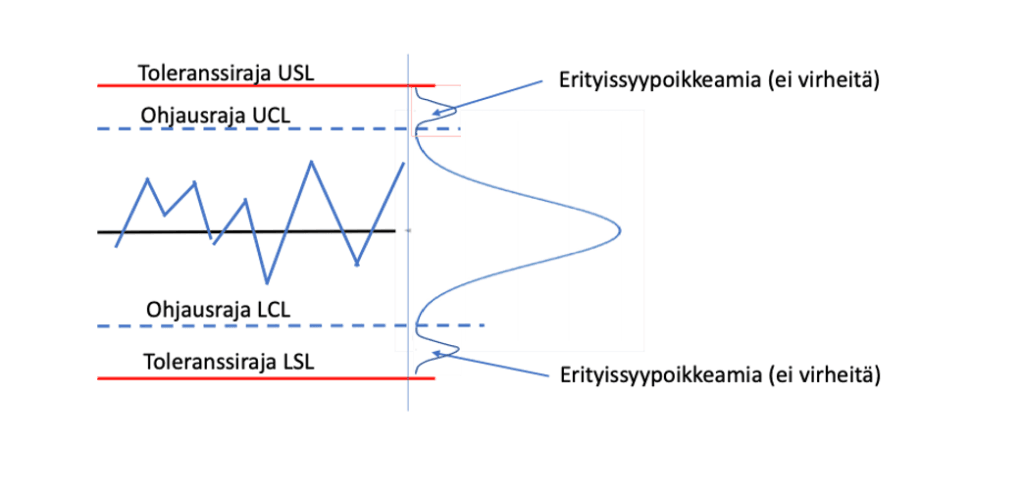
Huom! Laatutauluilla ei tätä analyysivirhettä (aliohjaus) voida yleensä estää, koska laatutauluihin kerättään tyypillisesti ”toleranssirajojen”, hyvä/huono informaatiota.
OSA 3 Stalan yhteydessä mainittiin (kuva 6), kuinka toleranssirajoja siirrettiin sisäänpäin, että reklamaatioita voidaan vähentää samalla tietysti sisäiset hylkymäärät kasvavat.
Erityissyy- ja satunnaissyypoikkeamia EI VOIDA erotella toisistaan itse ilmenemismuodon perusteella! Yleisesti kuitenkin uskotaan, että kaikilla ilmiöillä, tapahtumilla tai ilmenemismuodoilla on yksinkertainen syy, joka on saanut sen aikaan. Maailma on mielummin verkkojen ja vaikutusten kudelma, kuin suoraviivaisten syiden rakenne!
Laatutaulun organisatorinen tehtävä on selkeästi ja perustellusti jakaa vastuu poikkeamien (virhe, hukka, häiriö) pienentämisestä työntekijöiden ja johdon välillä:
- työntekijän ja työnjohdon vastuu – erityissyyilmenemismuodot (oireet) ja niiden analysointi ja poistaminen. Työkaluina ongelmanratkaisumenetelmät (Problem Solving). Kääntäen työntekijät ylläpitävät saavutettua systeemin/prosessin suorituskykyä.
- johdon ja ylemmän esimieskunnan vastuu – satunnaiset, yleiset, yhteiset, systeemisyyilmenemismuodot (oireet). Johto parantaa ja lisää suorituskykyä valitsemalla parannusprojekteja (Improvement, Lean Six Sigma), palkkaamalla lisähenkilöstöä ja investoimalla osaamiseen, koneisiin ja laitteisiin jne.
2. Lukujen analysointi
Laatutaulujen analysoinnissa on oleellista erottaa toisistaan:
- Erityissyyperusteiset ilmenemismuodot
- Satunnaissyy- eli systeemisyyperusteiset ilmenemismuodot
Tämä erottelu on konseptuaalinen. Tri Walter A. Shewhart esitti ”pragmaattisen” taloudellisen konseptin erottelulle, vaihtelulle. ±3 sigma!
Voit tehdä tämän jaottelun mille tahansa luonnonilmiölle tässä ja nyt ilman mitään esivalmisteluja tai muuta tietämyksen perusteella.
”Onko sinulla lämpöä?” Todennäköisesti kehosi on lämmin, joten lämpöä on! Ymmärsit oikein, kysymys koski tietysti erityistä lämpöä yli normaalin eli kuumetta. Puhekielessä ”unohdamme” helposti ympäristön, olemassa olevan tilan. Sanoja säästyy, jos ei joka paikkaan tarvitse ”tunkea” erityistä!
Toimit SPC:n periaatteiden mukaisesti jakamalla kehosi lämmön syntymekanismin mukaisesti kahteen ”taloudelliseen” luokkaan – satunnainen normaali lämpö ja ei-normaali lämpö eli kuume. Teit tämän erottelun konseptuaalisesti. Usein tämä erottelutaso ei ehkä riitä, vaan haet kuumemittarin ja mittaat lämmön. Saat lisää dataa ja lämmölle konkreettisen sisällön, mutta onko lämpö yli normaalin?
Tähän löytänet vastauksen netistä tai lääkäriltä! (Normaalin aamuisen lämmön yläraja on useimmilla välillä 36,5–37,5, mutta tässä esiintyy huomattavaa yksilöllistä vaihtelua. Lähde: https://www.terveyskirjasto.fi/dlk00793 ). Auttoiko? Jos lämpöä on 38 astetta, niin silloin siihen on melko varmasti erityissyyperusteinen syy. Systeemin ulkopuolelta sinuun on ehkä iskenyt virus tai bakteeri tai jotain muuta. Olisi hoivan ja korjauksen tarve!
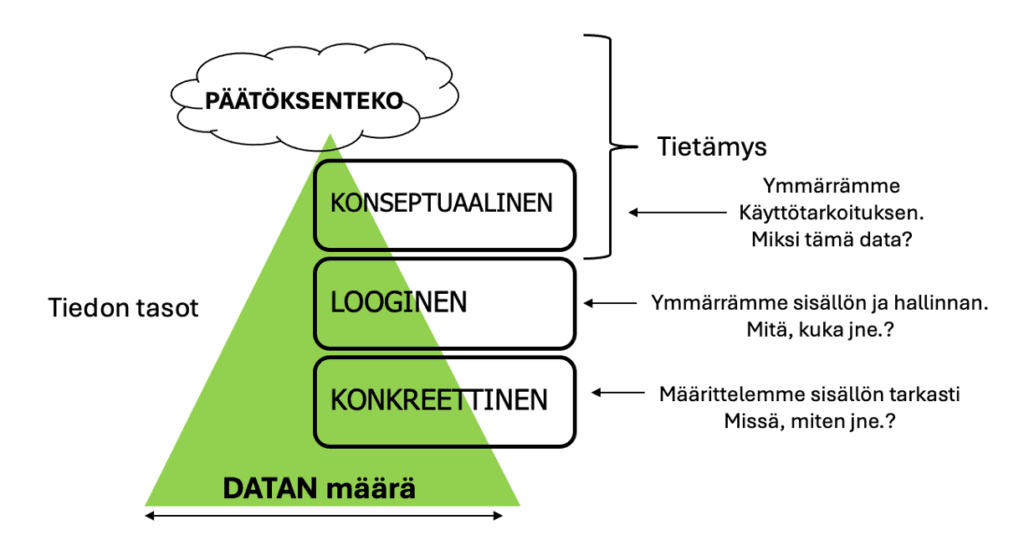
Tri Walter A. Shewhart tutki tätä ilmiötä (onko satunnainen vai ei) yli 7 vuotta sen jälkeen, kun hän ensimmäisen kerran esitti teorian vuonna 1924. Hän julkaisi kirjan Economic Control of Quality of Manufactured Products vuonna 1931.
Hän antoi ”yleistävän ja tarkentavan” ohjeen. Aseta raja noin ±3 sigmaan! Shewhart toteaa kirjassaan (1) s. 276-277:
”Siksi meidän on käytettävä rajoja siten, että niiden käytön myötä emme tuhlaa liikaa aikaa ongelmien tarpeettomaan etsimiseen.”
”Menetelmän käytölle on asettava vaihtelurajat … niin, että kun havainto löydetään näiden rajojen ulkopuolelta, määritettävän syyn (erityissyy) etsiminen kannattaa.”
”… valitsemme yleensä symmetrisen alueen, jolle on tunnusomaista rajat
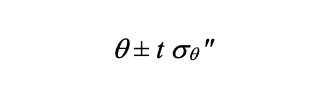
”Kokemus osoittaa, että t = 3 näyttää olevan hyväksyttävä taloudellinen arvo.”
”Hence we must use limits such that through their use we will not waste too much time looking unnecessarily for trouble.”
”The method of attack is to establish limits of variability.. . such that, when [an observation] is found outside these limits, looking for an assignable cause is worth while.”
”.. .we usually choose a symmetrical range characterized by limits
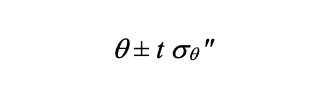
”Experience indicates that t = 3 seems to be an acceptable economic value.”’
Kolmen sigman rajat (±3 σ) eivät siis ole todennäköisyysrajoja, (vaikka hyvin monessa SPC-kirjassa näin virheellisesti väitetään) vaan taloudelliset, ekonomiset rajat (Economic Control of…) kuten kirjan nimikin sen kertoo. Kokemus on osoittanut rajat oikeaksi nyt jo 100 vuotta. Oikea nimitys SPC:lle olisi siis ”Taloudellinen Prosessin Ohjaus” TSP, mutta historiallisista syistä käytetään SPC-nimitystä.
Shewhartin jälkeen sadat tiedemiehet ovat eri tavoin yrittäneet ”murtaa” taloudellista 3 sigma rajaa mallintamalla, simuloimalla ja käytännön kokeilla. Samaa murtamista tehdään kaikille tiedeteorioille!
- Ensimmäiset murtoyritykset tapahtuivat vuonna 1952 (Girshick, Rubin).
- Vakavammin otettava yritys tapahtui, kun prof. A.J. Duncan laati ekonomistisen mallin vuonna 1956, jolla simuloitiin prosessin kokonaishävikki kustannusta E(L). Mallissa on yli 10 muuttuvaa taloudellista parametriä.
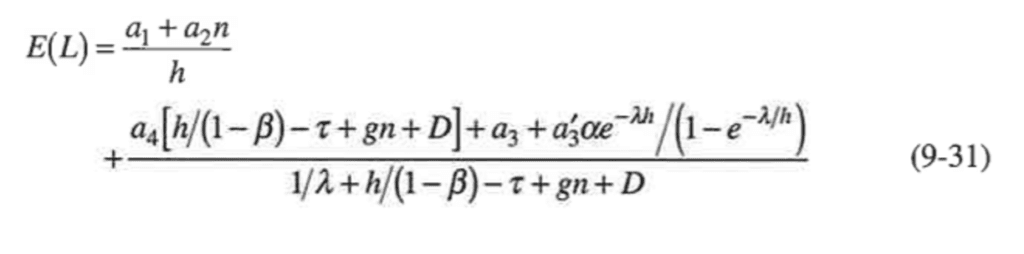
Malli ei kuitenkaan tuonut käytännössä uutta rajaa tai uutta teoreettista mallia.
Lähteet:
1. J. Duncan: “The Economic Design of – Control Charts Used to Maintain Current Control of a Process,” Journal of American Statistics Association 51, 1956, pp. 228-242)
2. Mohamed E. Seliaman, Salih O. Duffuaa: The Principle of Mathematical Induction Applied to the Generalized Model for the Economic Design of x -Control Charts; Journal of Applied Sciences, 2012, 2, 236-240
- 1980-luvulla suoritettiin lukuisia tieteellisiä tutkimuksia erilaisille prosesseille ja systeemeille (JQT, vol 26; Ho, Case). Varsinaista uutta universaalia tulosta ei löydetty.
- Vuonna 1991 prof. D.C. Montgomery laajensi A.J. Duncanin mallia ((12) sivut 413 – 443, (13) sivut 457- 466). Hän testasi tietokoneohjelmalla ohjauskortin suunnitteluparametrejä ottaen yhä lisää taloudellisia parametreja. Nyt löytyi erilaisilla parametrikombinaatioilla pieniä osaoptimeja. Prof. Ervin Sanigan mukaan mallilla voidaan saada 0,4 – 8,2 % parempia tuloksia, kun ohjausrajat poikkeavat 3 sigmasta olettaen, että käytettävät parametrit ovat oikeat. Kuitenkin optimointi vaatii sopivan ohjelman ja lukuisia reunaehtoja. Tieteellinen laatuyhteisö ei ole hyväksynyt mallia (teoriaa). 3 sigmaa pätee!
Vuonna 1993 W.E. Deming toteaakin kirjassaan The New Economics sivulla 180
”Shewhartin ohjauskortit toimivat hyvin laajalla käyttöalueella. Kukaan ei ole vielä takonut parannusta”.
“The Shewhart control charts do a good job under wide range of conditions. No one has yet wrought improvement.”
Tämän jälkeen en ole havainnut (löytänyt) varteenotettavia ”murto”yrityksiä. Matemaattista mallia on parannettu. Ilmeisesti 80 vuoden tieteellinen keskustelu 3-sigma taloudellisesta mallin/teorian oikeellisuudesta on päättynyt tai ainakin merkittävästi hiljentynyt Demingin kirjauksen jälkeen. MOT.
3-sigma rajoja voidaan perustella myös säätötekniikan – PID-säätimien – avulla. Deming esitti kirjoissa ja kursseilla ns. suppilokoetta (https://www.youtube.com/watch?v=05q0UC9HZeU) ja punaisten helmien koetta (https://www.youtube.com/watch?v=ckBfbvOXDvU ), jolla hän matematiikan lisäksi perusteli SPC:tä. Keskeiset tulokset säätöteknisestä tutkimuksesta ja todistamisesta kirjassamme (2) sivulla 184 – 190. Säätöteknistä todistamista käytetään yleensä koulutustilaisuuksissamme. Helpompi ymmärtää ja hyväksyä!
Kuinka taloudellista luokittelukonseptia voi käyttää laatutauluissa?
Erottelu erityissyy- ja satunnaissyyperusteisiin luokkiin voi tapahtua kahdella tavalla:
- ”Silmällä, aisteilla” (visuaalinen, aistivarainen ei matemaattinen analysointi) käyttäen hyväksi tietämystä 3 sigmasta
- Tilastollisesti (tieteellisesti, matemaattisesti)
I. Visuaalinen analysointi ”silmällä”
Laatutaulun analysointi ei ole vaikeaa!
Ihmisellä on luontainen taipumus analysoida oikein, kun tapahtumat liittyvät lähelle meitä itseämme, esimerkiksi ruumiinlämpö. Maistaessamme tai haistaessamme ruokaa, onko se hyvää tai huonoa, päätös osuu todennäköisesti luontaisesti ja ”taloudellisesti” oikeaan. Et tarvitse siihen ohjauskorttia. Teet ehkä loogisen päätelmän tai luet ehkä ”parasta ennen” tai ”viimeisen käyttöpäivän” vahvistaaksesi tietämystäsi.
Päättelemme oikein terveydentilamme oman tuntemuksen, kipujen jne. perusteella. Lääkäri sen sijaan ei tunne sinun kipujasi. Hän tarvitsee mitatut tilastolliset rajat tulkitakseen oikein sairauden. ”Labran” viitearvot, laaja ja pitkä koulutus, kokemus ja tietämys yhdistetään, jotta tulos olisi pätevä.
Kun analysoimme meistä vähän kauempana olevia tuntemattomia ilmiöitä – työtämme, palvelua, osakokoonpanoa, työstöä, materiaalia – luontainen kykymme erottaa erityissyy satunnaissyystä pettää, koska hyvä ja huono on määritelty ja opeteltu esimerkiksi suunnitelmista, piirustuksista, työohjeista, yrityksen sisäisistä normeista. Asia ei ole meille kovin tuttu tai se ei ole esiintynyt lukuisia kertoja. Työ syntyy prosessissa, joka määrittää luonnolliset rajat. Missä ovat prosessin luonnolliset vaihtelun rajat?
Tällöin meidän on yritettävä käyttää historiallista oletusta, että ”mikään ei muutu” ja arvioitava tästä taloudellisen puuttumisen kynnys – kannattaako tutkia ja puuttua poikkeamaan vai ei – Economic Control.
Katsomme, missä on tapahtunut erityisen suurta muutosta ominaisuudessa tai virhemäärän kasvua (hyppäys) edellisiin päiviin tai viikkoihin (jaksoihin) verrattuna. Useasti tätä sotkee erilaiset tuotteet ja palvelut. Tietämystason tieto (ja data) ei riitä. Tarvitaan konkreettista tietoa ja enemmän dataa. Tätä sanotaan aikasarja-analyysiksi.
Voit ajatella piirtäväsi silmälaseihin ”erityissyyrajat LCL ja UCL” ja tarkastella laatutaulua näiden rajojen läpi ja tunnistaa taloudellisesti merkittävät muutokset.
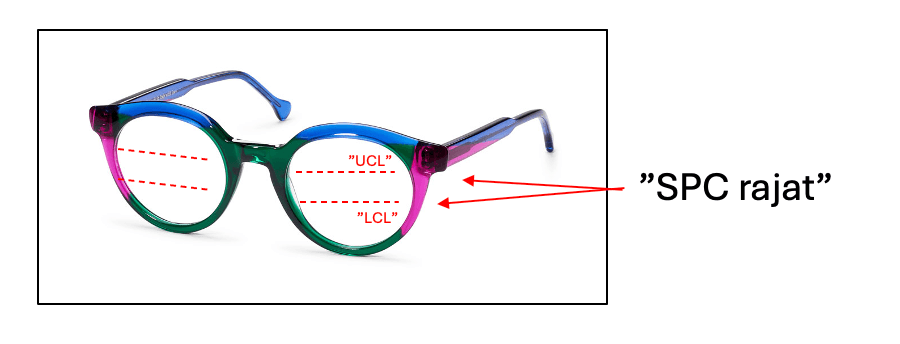
Mitä sana merkittävä tarkoittaa: jos samaa poikkeamaa, virheen ilmenemismuotoa, esiintyy keskimäärin c=4 kpl/jakso, silloin merkittävä poikkeama on suurempi kuin 10 kpl/jakso (4±3√4 = 4+3*2=10). Tämä päätelmä tuli Poisson-jakaumasta, joka on ns. yksiparametrijakauma, jossa hajonnan eli sigman suuruus on neliöjuuri keskiarvosta. Kun tämä neliöjuuri kerrotaan 3:lla, saat ohjausrajat keskiarvon ympärillä. Arvioit ensin ilmenemismuodon poikkeaman keskiarvon C ja katsot 3 sigma rajat – taulukossa punaiset arvot. Todella helppo laskukaava ja myös helppo muistaa!
Taulukko 2. Poisson-jakaumaan perustuvat SPC-rajat .

Harjoittelemalla opit pian ilman laskentaa näkemään datasta erityissyyn omaavat ilmenemismuodot ja analyysikohteet. Näin toimin Kemppi Oy:llä toimisessani laatupäällikkönä vuosina 1981-85 ja näin edelleen, kun näen TV:tä tai lehdistä tapahtuma-aikasarjoja, joissa annettaan ymmärtää, että on tapahtunut muutos. Olisko? Pieni laskutoimitus – ja päätös!
Oletuksena on tietysti, että tapahtumat, tuotantomäärät jne. ovat likimain samansuuruiset ja perusoletus muuttumattomuudesta pitää paikkansa!
Huom! Silmälasimenetelmä on vanhaa ”pomottamista”. 1960-70-luvulla kokenut harmaatakkinen työnjohto (pomo) kiersi jatkuvasti työntekijöiden parissa ja puuttui ja vaati korjaamaan ”erityissyyt”. Stabiloi prosessia. Joskus toimi, joskus ei. Nythän tätä ei enää hyväksytä! On mielivaltaa vaatia pienempää poikkemaa ilman perusteita, vai onko?
Tutki päivittäin laatutaulua täyttäessäsi uudet yllättävät poikkeaman/virheen esiintymismuodon määrät, jotka poikkeavat merkittävästi aikaisemmasta keskiarvosta. Yleensä työn helpottamiseksi C-raja merkitään taulun vasempaan laitaan ja pidetään samana koko taulun ajan (kuukausi). Nyt työntekijät tietävät rajat. Ei ole mielivaltaa. Vaihdettaessa taulua uuteen, rajat määritetään vanahan täytetyn taulun datan perusteella.
Yleensä yliarvioimme merkittävän muutoksen ja tulkitsemme liian pienet muutokset erityisiksi muutoksiksi. Lisää valtavasti huolta, työtä ja hukkaa ja kustannuksia!
Uudet, yllättävät virheet ovat useimmiten erityissyistä johtuvia – on tapahtunut muutos aiempaan jostakin (näkyvästä ja nimettävästä) syystä.
Katso kuvaa 6 levytyöstökeskuksen häiriö-/hukkalaatutaulua. Kun häiriöt materiaalikulussa vähenevät, läpimenoaika on pudonnut linjalla 30 päivästä 1-2 päivään ja samalla tuotteiden toimitusvarmuus on noussut 65 %:sta 99 %:iin.
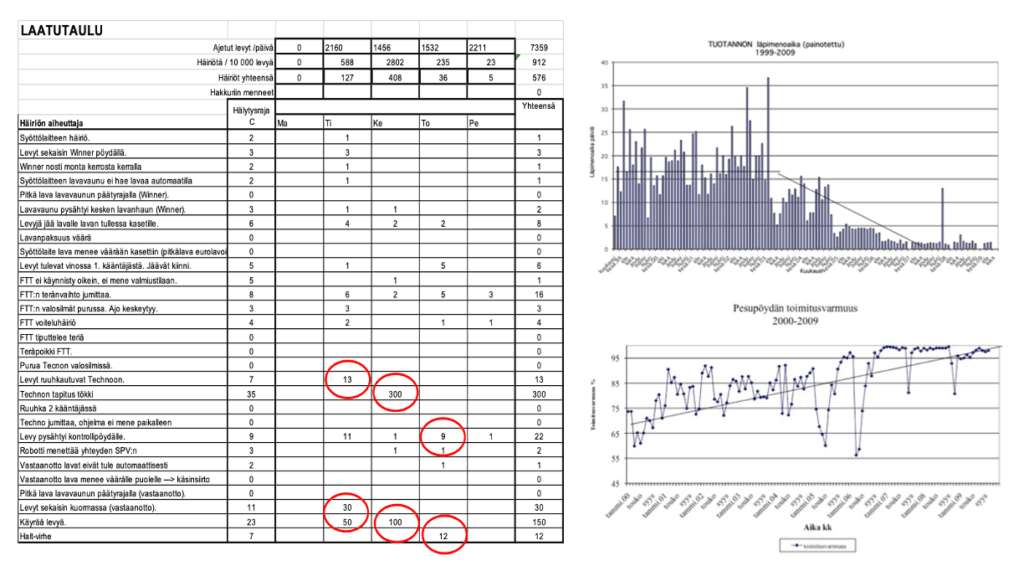
Työnjohdon (tai ko. prosessin “vetäjän”, omistajan) tehtävänä on yhdessä työntekijöiden kanssa tutkia ja selvittää erityissyymuutoksen takana oleva syy ja poistaa poikkeaman aiheuttaja. Kokemus on opettanut, että uuden koneen, laiteryhmän tai prosessin ylösajossa laatutaulu on erityisen hyödyllinen!
Ehkä mieltä kaivertaa, osasinko erotella erityissyyt ja satunnaissyyt oikeisiin luokkiin silmämääräisesti. Oliko silmämääräinen erottelu liian epämääräinen? Jos epäilet, niin tee tilastollinen analyysi varmistaaksesi analyysin. Erityisesti on kiinnitettävä huomiota kunkin virheen ilmenemismuodon esiintymisen historialliseen keskiarvoon, joka määrittää myös ohjausrajat keskiarvon molemmilla puolilla. Onko keskiarvo oikein määritetty? Älä mieti laskentaa, vaan prosessia. Erityissyyt voivat vääristää laskentaa.
II. Tilastollinen analysointi (C-kortti)
Ohjausrajojen määrittäminen ”uuteen” laatutauluun tapahtuu edellisen taulun (esim. edellisen 4 viikon/20 päivän) tietojen pohjalta. Tämä menettely pienentää poikkeamien/virheiden keskiarvon virhettä suhteessa 1/√n . Jos lasket keskiarvon 4:stä luvusta, virhe puolittuu. Jos lasket keskiarvon 25 luvusta, virhe on 1/5-osa.
Matemaattinen erottelu tapahtuu seuraavasti:
- Sinun on seurattava ja kerättävä virhe-/poikkeamadataa jonkin aikaa, ennen kuin voit määrittää rajan laatutauluun. Minimissä viikko (5 datapistettä), mutta mielummin kuukausi (20 datapistettä/ilmenemismuoto).
- Laske laatutaulun täytyttyä jokaisen virheen yhteissumma taulun oikeaan marginaaliin.
- Jaa jokainen virheen yhteissumma sillä päivien lukumäärällä, jolloin kyseistä virhettä on voinut syntyä – tuotetta tai palvelua on tehty. Vaikka tauluun ei ehkä ole virhettä merkattu eli virhe jonain päivänä on 0, tämä huomioidaan. Jako-osamäärä C’ on keskimääräinen päivävirhe, jakson virhe. Aikajaksot voivat olla vuoro, päivä, viikko, kuukausi jne.
- Laske erityissyyrajat ”todellisesta” keskiarvosta C’±3√C’. Korjaa edellistä kohdan 3 keskiarvoa lähemmäksi todellista keskiarvoa. Todelliseen keskiarvoon C’ lasketaan (joskus arvioidaan) vain ne päivät, jolloin ei ole erityissyyesiintymää. Esimerkki 9±3 √9 = 9±9= 0 – 18 kpl. Laskettu raja on ns. induktiivinen raja (ohjausraja, hälytysraja, luonnollinen raja, C-raja, raja huomiselle), joka tulee siis historiadatasta toisin kuin spesifikaatiot, toleranssit, jotka päätetään (deduktiivinen raja). Ohjausrajojen määrityksessä käytetään siis harkintaa ja tietämystä. Laskenta on aputyökalu.
- Vaihdettaessa uusi puhdas laatutaulun jo täytetyn taulun tilalle merkitään tässä yhteydessä ylempi C= C’+3√C’ raja laatutauluun täytetyn taulun tulosten perusteella. (ns. C-raja lasketaan jokaiselle merkittävälle virheen ilmenemistyypille erikseen => joka riville). Jos on pitkä historia laatutauluista, rajoja ei aina nosteta tai lasketa, vaikka laskenta näin osoittaisi, jos selvästi ei ole muutosta systeemissä. Rajat ovat harkintaa ja ”matematiikkaa” (ja tietysti sisältävät myös määritysvirheen!)
- Päivittäin laatutauluja täytettäessä merkitään ympyrällä kaikki ne virheet, joiden lukumäärä ylittää kunkin virheen ohjaus-/valvontarajan ja ryhdytään toimenpiteisiin virheen poistamiseksi / ennaltaehkäisemiseksi.
Apuna voi käyttää erityissyytaulua, johon tulee syyn analyysi ja toimenpide.
Kuva 7. Laatutaulun C-rajan laskenta. - C-rajan määrittämiseen voi käyttää myös Minitab tilasto-ohjelmaa, joka antaa vähän tarkemmat arvot, jos ei halua laskea neliöjuurta. Minitab Assistantin puolella ohjelma rajaa myös ulos erityissyyt, jotka ”vääristävät” tulosta. (Tarkkuus tässä ei ole ensisijainen syy, vaan helppous.)
Täydennystä ja tarkennusta C-rajojen laskentaan:
Harvinaisten tapausten jakauma noudattaa Poisson-jakaumaa. Poisson-jakauma on yksiparametrijakauma, jossa virheiden keskiarvon neliö on myös vaihtelun keskihajonta (s=σ=sigma). Täydellistä Poisson-jakaumaa, joka on toispuolinen, ei luonnossa ole, mutta tämä jakauma ja erityisesti siitä poikkeama antaa signaalin erityissyyperusteisen ilmenemismuodon olemassaolosta (Laatuteoria). Poisson-jakaumalle on olemassa erityisehdot, joihin tässä ei puututa. Konseptuaalinen ajattelu on etusijalla.
CLU,L ´= C±3√C´
jossa C’ = virheellisten tapahtumien keskiarvo
C-kortin käytön ongelmia (14,15)
- Tarkastettaessa tuotteita tuote hylätään yleensä ensimmäisestä vakavasta viasta ja tällöin saattaa virheiden etsiminen pysähtyä tähän. C-korttia varten olisi kuitenkin kaikki virheet/poikkeamat etsittävä. Liittyy Poisson-jakauman reunaehtoihin.
- Toinen ongelma on, että Poisson-jakauma on erittäin vino, kun keskiarvo on pieni (<20). Tästä seuraa, että etenkin pienillä näytemäärillä virhehälytyksiä tulee liikaa. Jos C on 1/näyte (vuorossa, päivässä), ylittyy raja n. 3-4 %:ssa kun C = 7 – 12/näyte ylittyy raja n. 0,5 %:ssä. Pienillä virhemäärillä on vaarana yliohjaus ja siitä seurauksena virheiden kasvu.
- Kolmas ongelma on, että alle 10 kpl/näyte tapauksissa ei parannusta voida havaita, koska alaraja LCL on 0. Vaarana on aliohjaus.
- Poisson- jakauman vinouden voi huomioida niin, että pienillä C-arvoilla käytetään 3s: sijasta 0,005 Aor:aa ja 0,995 Yor:aa. Kun virheiden määrä C on yli 20, voidaan käyttää neliöjuurta. Näin, jos ollaan tarkkoja, mutta älä ole!
Taulukko 3. Poisson-jakauma pienillä (<20) virhemäärillä. Jakauman rajojen laskennassa on käytetty todennäköisyyttä 99,5% (14).
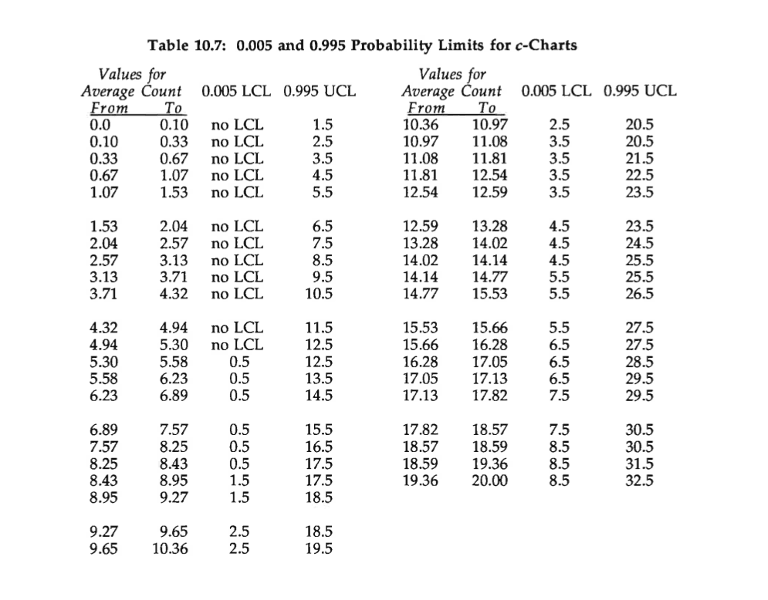
Esimerkki C-rajojen laskennasta
Taulukkoon on merkitty päivittäiset näytteet virheistä 22 päivän ajalta. 1. päivänä oli 10 virhettä, 2. päivänä 1 virhe, 3. päivänä 32 virhettä jne.
Taulukko 4. Erään ominaisuuden virhemäärät kuukauden ajalta (22 työpäivää).

Lasketaan kerättyjen virhetietojen pohjalta kolmen sigman raja (C-raja, UCL=Upper Control Limit ja LCL=Lower Control Limit) virheiden ilmenemismuodolle. Nämä virheet kuvaavat yhtä ilmenemismuotoa/riviä laatutaulussa. Rivejä taulussa voi olla jopa 30-50. Laskenta tapahtuu laskemalla virheiden summa 296 oikeaan laitaan ja jakamalla summa päivillä 22 kpl, saadaan virheiden keskiarvo C’=13,5/päivä.
Poisson-jakauma on yksiparametrijakauma, jossa sigma σ tai s on neliöjuuri keskiarvosta √ 13,5 = s = 3,67.
Kertomalla tämä neliöjuuri 3:lla saadaan keskiarvon ympärillä oleva vaihteluväli. UCL ja LCL eli C arvoiksi saadaan 25 ja 2 pyöristettynä ylöspäin ja alaspäin.
Lasketun tiedon pohjalta tiedät, milloin on mahdollista löytää poikkeaman, virheen, hukan, häiriön ilmenemismuodon takaa erityisen syyn, joka on aiheuttanut taloudellisesti merkittävän muutoksen (jäljen). Etsimällä jäljen, löydät syyn.
Lasketaan ja piirretään rajat esimerkille. C-kortti.
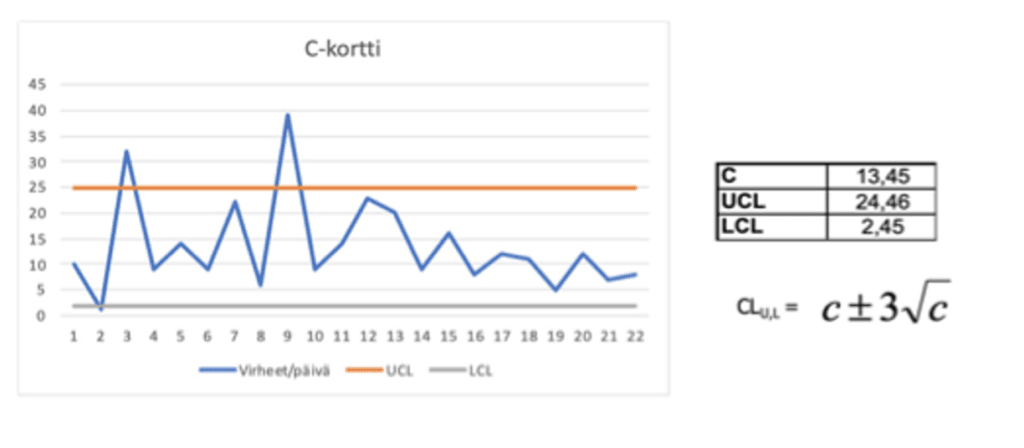
Taulukon ja käyrän mukaan päivinä 3 ja 9 on virheitä ”epätavallista” enemmän.
Virheen ilmenemismuodon takaa voi löytyä erityissyyperusteinen syy. Huom. esimerkki on auttamatta ”myöhässä”, jos laadit rajat 23:na päivänä ja yrität löytää syyt 3:lle ja 9:lle päiville syyt!
Koska rajoja laskettaessa ei saisi olla erityissyytä, ne olisi poistettava ja laskettava uudet rajat UCL´=22 ja LCL=1 (Korjattu keskiarvo). Jos käytetään näitä rajoja, edelleen päivän 12 virhemäärä 23 olisi poistettava ja laskettava uusi raja.
Suositukseni on, että vain suuret poikkeamat (virhemäärät) huomioidaan laskennassa. Tässä tapauksessa en poistaisi päivien 3 ja 9 arvoja laskennasta ja pitäytyisin kuvan rajoihin.
Jos sen sijaan virheitä olisi ollut 50-100, pisteet olisi vinouttaneet liikaa rajoja. Viime kädessä rajojen määritys tapahtuu harkinnan ja laskennan tuloksena siitä, mitkä ovat luonnolliset rajat.
Laskenta antaa mallin, jota sovitetaan rajoihin. Jokaisessa mallissa on aina virhettä ja harkinnan varaa. Laatutaulua ei kuitenkaan yleensä käytetä taaksepäin analyysissä, kuten edellisessä esimerkissä, vaan lasketaan raja huomiselle ja tuleville päiville eteenpäin. Yleinen laatutaulun käyttövirhe on, että rajat luodaan jälkikäteen, kun ne pitää luoda etukäteen. Luo edellisen laatutaulun avulla rajat uuteen tyhjään tauluun. Rajat hälyttävät merkittävistä muutoksista VÄLITTÖMÄSTI.
Tässä menettelyssä oletetaan, että systeemi pysyy stabiilina ja synnyttää keskimäärin saman verran virheitä (systeemin/prosessin suorituskyky) ja aina silloin tällöin voi systeemiin/prosessiin tulla epätavallinen poikkeama yhteen tai useampaan virheen ilmenemismuotoon.
C-kortti ja lukujen matemaattinen analysointi Minitab-ohjelmalla
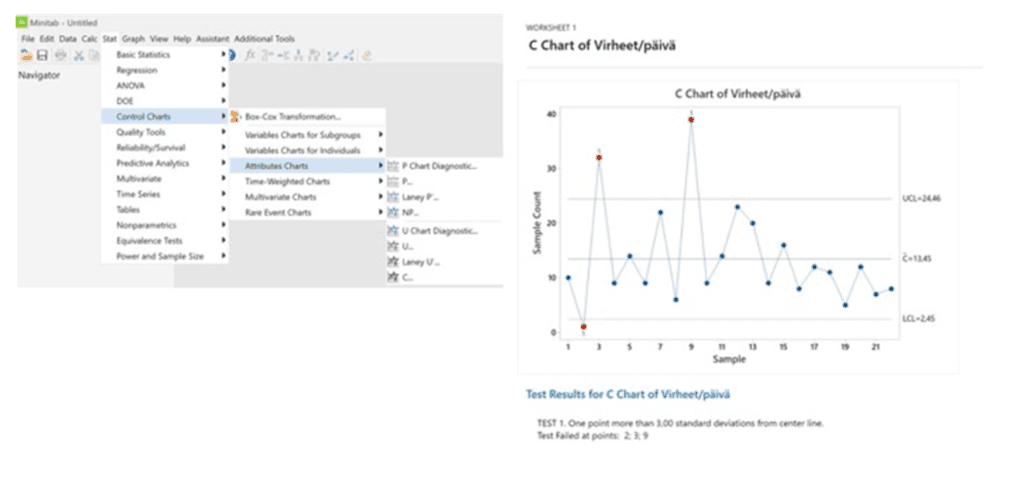
On huomattava, että ohjausrajoja pitäisi käyttää eteenpäin eli jatkaa rajoja tuleville päiville. Minitab laskee vain menneiden päivien virheiden perusteella rajat. Nämä lasketut rajat olisi piirrettävä eteenpäin huomenna, ensi viikolla syntyville tuotteille ja palveluille. Voit käyttää Minitabia myös niin, että tuot datan joka päivä Minitabiin ja päivität (update) analyysin päivittäin. Näin tekee on-line ohjelmat. Saat C-kortin rajat myös tulevaisuuteen, jos tulevien datojen kohdalle merkitset * ilman arvoja.
SPC:n ja laatutaulun ”tehoton” käyttötapa on jälkikäteen laskea rajat ja analysoida tulosta. Jälkikäteen syitä on vaikea selvittää ja feedback myöhästyy!
3. Erityissyyperusteisten poikkeaminen toimenpiteet (Problem Solving, Stabilointi)
Ongelmanratkaisu- ja parannusmenetelmät muodostavat laajan kirjon erilaisia laatutekniikoita ja menetelmiä (>350). Paras opas ja ASQ Best Seller on Nancy R. Tague: The Quality Toolbox, 3rd Edition. (ASQ, American Society for Quality).
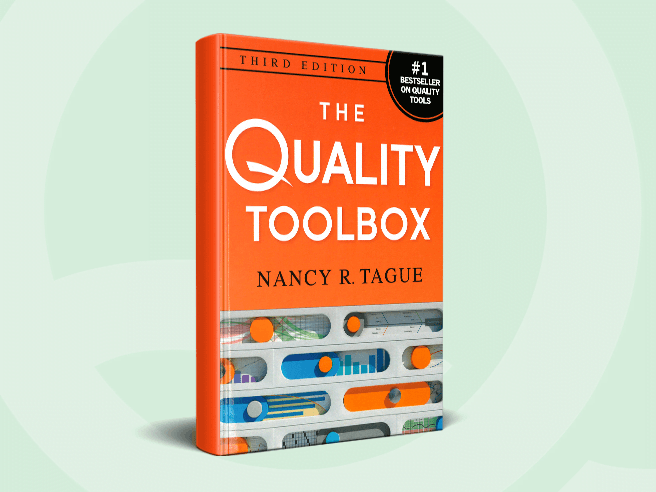
Suuri osa (>90 %) ongelmien ratkaisuun johtaneista analyyseistä ja toimenpiteistä ei tarvitse mitään erityistä osaamista tai menetelmiä. Erityissyyperusteisen poikkeaman juurisyy löytyy selkeänä muutoksena, jos poikkeamasta ei ole kulunut kuin hetki aikaa, ja myös korjaus, joskus parannus, on ilmeinen.
On kuitenkin joukko ongelmia (<10 %), jotka eivät tahdo selvitä (ei löydy juurisyytä) ja vaikuttavaa inputtia ja tähän toimenpidettä. Ongelmat palaavat yhä uudelleen laatutaululle erityissyynä. Tällöin on syytä tutkia ongelmaa (inputteja) syvemmin.
Yleensä ei ole vaikea luetella kymmeniä, jopa satoja inputteja ja mahdollisia syitä. Ongelma on löytää näiden syiden (input) joukosta juuri se tärkein juurisyy, vaikuttavin ja se, johon voidaan kohdistaa helposti ja edullisesti toimenpide.
Tutkinta- ja analyysikeinoina on ns. 7 laatutyökalua + menettely
- Pareto-diagrammi,
- Syy-seuraus -diagrammi,
- Pylväsdiagrammi,
- Hajontadiagrammi,
- Keskiarvo ja hajonta,
- Aineiston erittely,
- Valvonta/ohjauskortit
joilla voi ongelman juurisyytä (input) yrittää kaivaa esiin. Työkalut yksin ei riitä, vaan on edettävä työkalujen käytössä loogisesti tietyn hyväksi havaitun järjestelmän mukaan.
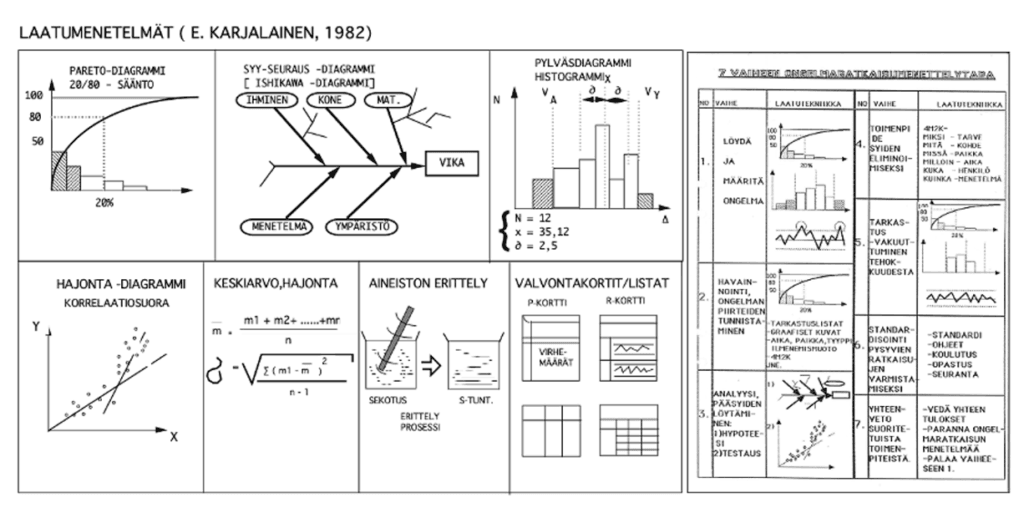
Kuvassa on esitettynä graafisessa muodossa tilastolliset 7 työkalut ja työkaluihin liittyvä 7 kohtainen menettelytapa (QC story), joita opetettiin 1980-luvulla ja opetetaan edelleen 2020-luvulla.
Näiden rinnalle on noussut autoteollisuudessa käytetty 8D ja Leanista ja Toyotasta tunnettu A3-nimellä tunnettu ratkaisumenettely. Pohjimmiltaan ne ovat yksi ja sama asia. Tieteellisiä paremmuusvertailuja ei ole tehty.
Ratkaisuprosessi (menettely) on yleensä jaettu 7-8 perättäiseen vaiheeseen. Noudattaa usein PDSA-ympyrää.
- Löydä, määritä ongelma,
- Havainnoi, kerää dataa ongelman piirteiden selvittämiseksi,
- Analysoi pääsyitä: hypoteesi ja testaus,
- Löydä toimenpide syyn eliminoimiseksi,
- Tarkasta, vakuutu, toimenpiteen tehokkuudesta,
- Standardoi syiden ratkaisujen varmentamiseksi,
- Yhteenveto suoritetuista toimenpiteistä.
Viimeisin ongelmaratkaisun trendi on korostaa juurisyytä ja sen hakemista.
Juurisyy on alkujaan kehitetty Toyotalla. ”Menetelmästä voidaan kiittää Sakichi Toyodaa, joka kehitti ”5 Whys, 1 How”. Vuonna 1888 Sakichi löysi menetelmän tarkkaillessaan automaattisia kutomakoneita (looms). Hän perusti Toyoda Automatic Loom Works Co. Ltd vuonna 1926” patentista saaduilla rahoilla. Artikkeleissamme olemme käsitelleet tätä juurisyy ongelmanratkaisusektoria monelta suunnalta.
- Artikkeli: Juurisyyanalyysi ja sen kehittyminen (5.1.2023)
- Artikkeli: Juurisyyn löytämisen strategioita (23.1.2023)
- Artikkeli: Juurisyyanalyysi vai pinnallinen syyanalyysi? (16.2.2023)
- Artikkeli: Pimeän näytön juurisyyanalyysi (RCA) (9.3.2023)
- Artikkeli: Juurisyyanalyysin monet kasvot (30.3.2023)
- Artikkeli: Juurisyyanalyysi (RCA) ja Shainin Systeemi™ (15.6.2023)
Vuonna 2023 lisäsimme koulutusohjelmistoomme erilaisia juurisyyanalyysikursseja täydentämään ”vanhoja” hyväksi havaittuja ongelmanratkaisukursseja.
Perusväittämä, joka minulle esitettiin 1980-luvulla, oli, että laatutekniikkaa ja laatutauluja voi käyttää vain suuryrityksissä, joista saadaan paljon dataa. Laatu-tekniikka, saati tilastollinen SPC, ei sovellu pienyritykseen (PK-yritys), joka tekee yksittäisiä tilaustuotteita. Halusin näyttää, että väittämä ei pidä paikkansa!
Jokainen voi arvioida seuraavan casen avulla, oliko väittämä perusteltu.
Case 1: Salpausselän Kirjapainossa käytettiin laatutauluja laajasti niin tuotannossa kuin uuden 6-väripainokoneen ylösajossa.
Keskeiset tiedot yrityksestä.
- Perustettu vuonna 1952
- Ajautui likviditeettikriisiin vuonna 1992 ja jätti konkurssihakemuksen
- Toiminta jatkui ”Kirjapaino Oy” nimisenä
- Mainospainotuotteita, etikettejä, kirjoja, luetteloita ja lomakkeistoja valmistava tilauskirjapaino
- Työllisti noin 30 henkilöä
- Runsaan 4 miljoonan euron liikevaihto
- Fuusioitui toisen graafisen alan yrityksen kanssa vuonna 2006
Laadunparannustyö käynnistyi laatutaulujen avulla stabiloimalla vuonna 1988.
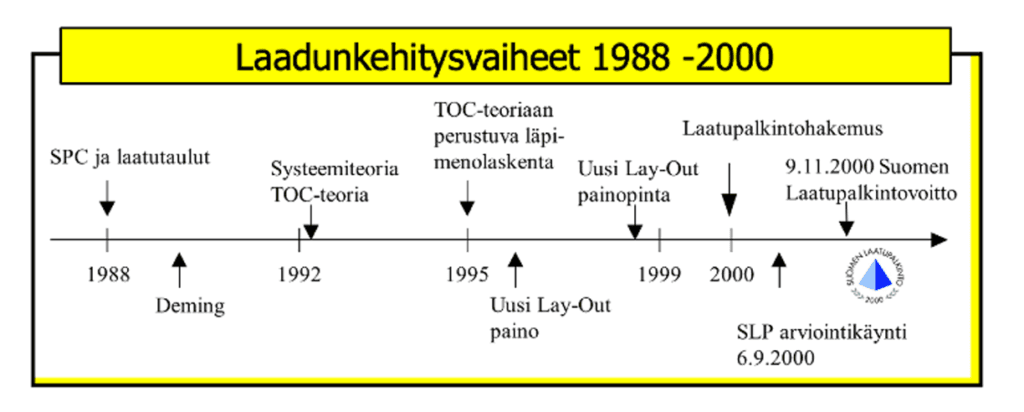
Parannustyö tapahtui kahdessa vaiheessa:
I. 1988 – 91 tuotelaadun kehittäminen, joka on kaiken ydin (yrityksen tarkoitus)
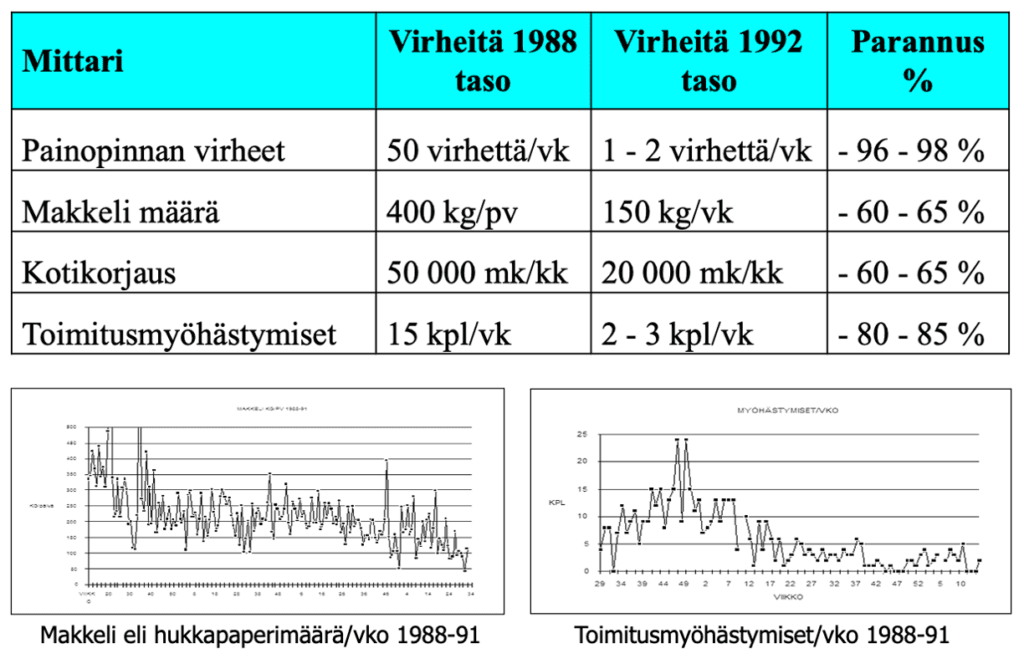
II. 1992 likviditeettikonkurssin jälkeen otettiin käyttöön systeemiteoriaan perustuva superputkistrategia (= prosessi) ja kokonaisvaltainen laadunkehittäminen (TQM)
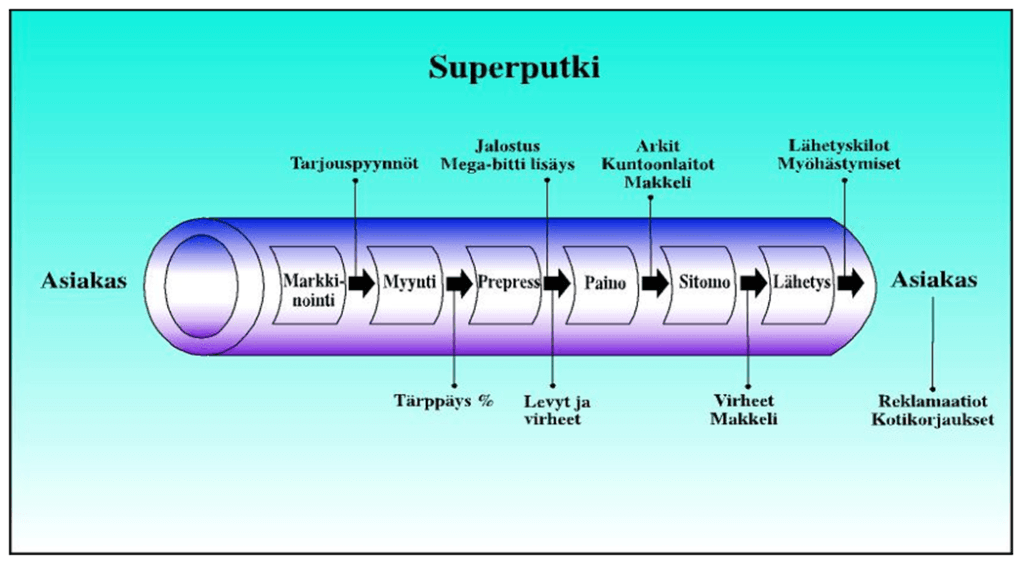
- Johtamis- ja toimintatavat muutettiin systeemi- ja TOC-teorian mukaisiksi
- Toiminta-ajatus: tuottaa taloudellisesti kannattavia ja asiakaslähtöisesti laadukkaita painotuotteita ja -palveluja kilpailukykyiseen hintaan nopealla toimitusajalla
- Organisaatio oli matala ja hyvin avoin kokonaisuuden muodostava tiimi, jonka toimintaa ohjattiin aamupalaverilla.
- Organisaation toiminnan ja tuotannon laatua seurataan organisaation käyttäytymistä kuvaavilla laatutauluilla ja käyrillä (SPC)
- läpimenoaika, läpimeno, liikevaihto, tuotantomäärät, hukan määrä, myöhästymiset, kotikorjaukset
- TOC-teoriaan ja systeemiteoriaan perustuva superputki menettely otettiin käyttöön. Laadunparannus laajennettiin koskemaan johtamista ja koko yritystoimintaa. (johtamistavan muutos)
- Luotiin uusia kehitysmittareita ja toiminta prosessoitiin.
- Organisaatio muutettiin matalaksi ja henkilöstölle jaettiin enemmän vastuuta. Tuotannon lay-out päivitettiin.
- Otettiin käyttöön aamupalaverikäytäntö, jonka avulla tiedonkulkua parannettiin huomattavasti. (EEK:n tuoma ”malli” Japanista!)
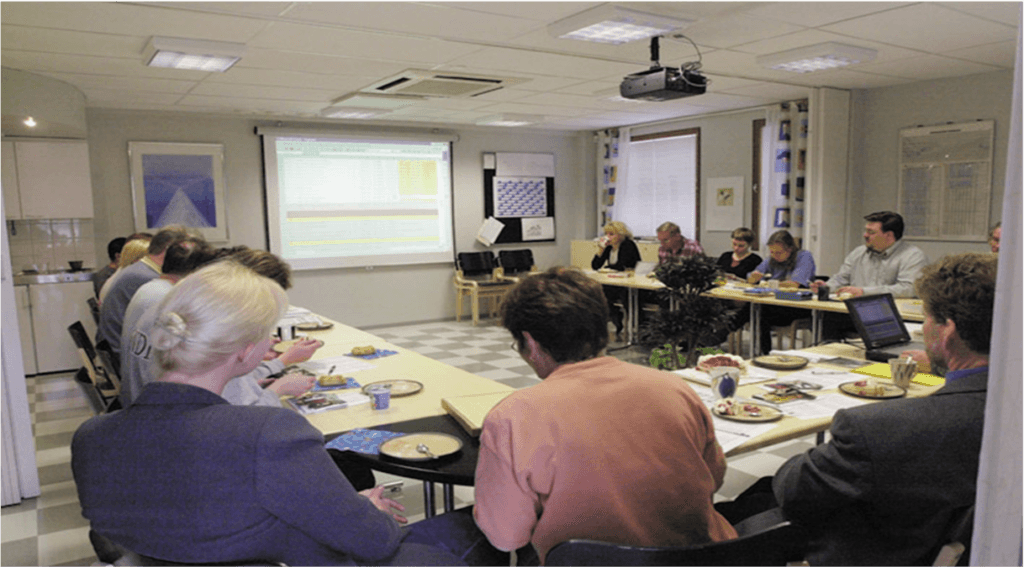
Salpausselän Kirjapainon yksityiskohtainen tarina on kerrottu kirjassamme:
Tanja Karjalainen, Eero E. Karjalainen: Laatujohtamisoppien (TQM) soveltaminen PK-yritykseen – SPC, systeemiteoria, TOC teoria (2000) (17).
Kirjassa on esitetty yksityiskohtaisesti kaikkien laatutaulujen aikaansaamat parannukset ja laatupalkintohakemus ja perustelut.
Taulukoissa on esitetty yhteenveto laadun kehityskohteista numeroin ja samalla laatutaulujen vaikutus yrityksen tuloksiin.
Taulukko 5. Keskeiset Salpausselän kirjapainon laatumittarit ja niiden kehittyminen 1988-1999.(17)
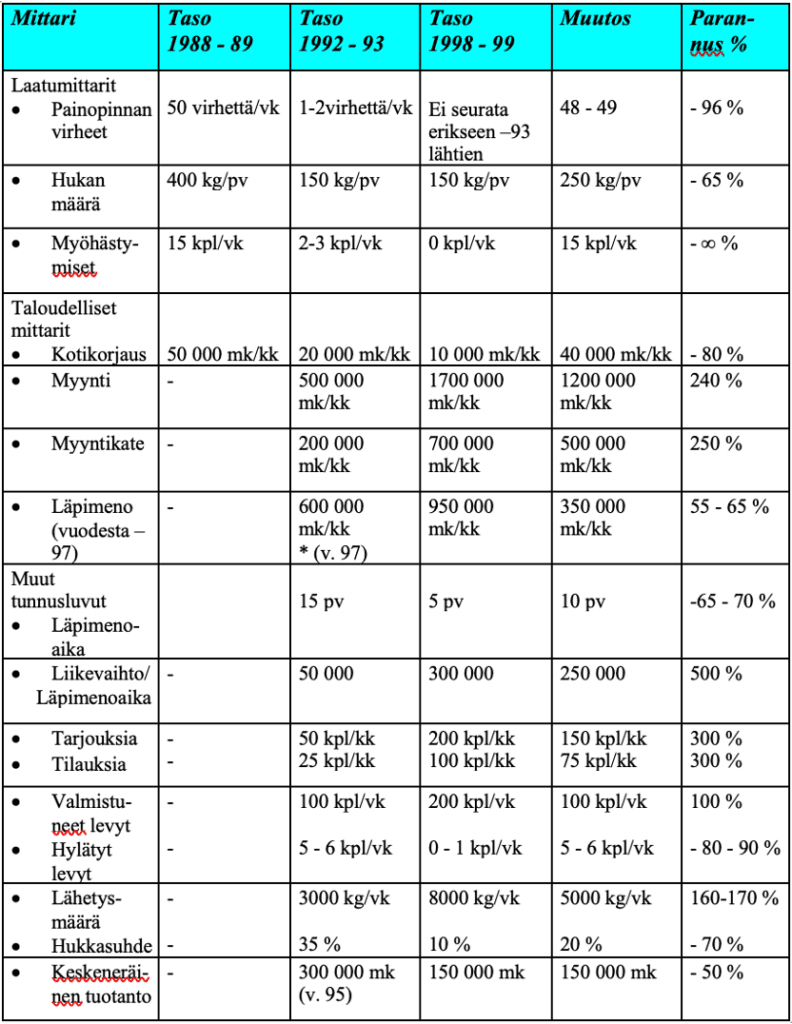
4. Satunnaissyyperusteisten poikkeamien toimenpiteet (parantaminen)
Suuri osa palvelu- ja teollisuusyritysten prosesseista on epästabiilissa, kaoottisessa tilanteessa. Tämä ei kuitenkaan tarkoita, että ne eivät toimisi tai että niiden avulla ei voitaisi tuottaa palveluja ja tuotteita.
Yritykset voivat tuottaa tuotteita ja palveluja, mutta ne ovat paljon tehottomammassa tilanteessa kuin ne voisivat olla. Jatkuvaa säätämistä. Suomalaisten yritysten heikko tuottavuus johtuu pääosin valtavasta määrästä poikkeamia, jota ei havaita eikä johto osaa arvioida oikeaa suuruusluokkaa (n. 3000 kpl/työntekijä/vuosi). Myöskään aloitettujen korjaus ja parannustoimenpiteiden onnistumisen toteutumisesta ei ole varmuutta. Yleensä ei ole seurantakäyriä! Tämä johtuu ensisijassa taloudellisen ohjauksen (SPC) puuttumisesta. Paljon turhautumista ja laatukustannuksia (15-35 % liikevaihdosta).
Satunnaissyyperusteisten ongelmien ratkaisussa tarvitaan huomattavasti enemmän tieto-taitoa, prosessidatan tilastollista analysointia ja kykyä optimoida lukuisten tekijöiden joukosta optimaalinen tulos.
Prosessitietojen tilastollinen analyysi olettaa yleensä, että tiedot saadaan stabiilista prosessista.Tilastolliset työkalut eivät toimi epästabiililla datalla!
Tästä syystä parannusmenetelmät ja niihin liittyvät laatutyökalut vaativat stabiilin prosessin.Stabiilisuus unohtuu, vaikka se on kirjoitettu ja esitetty lähes kaikkien menetelmien käyttöohjeiden etusivulla.
ÄLÄ KOSKE suorituskyvyn parannustyökaluihin ja menetelmiin, jos et ole varmistunut stabiilista tilasta!
Sama sääntö on terveydenhoidossa. Jos olet saanut virus- tai bakteeritartunnan (flunssan, koronan), älä kohota suorituskykyäsi rasittamalla itseäsi, lähtemällä lenkille tai punttisalille. Seuraukset voivat olla kohtalokkaat.
Stabiiliin tilaan pääsemiseksi on vain Yksi keino, ohjauskortit (laatutaulu) kuten prof. Donald J. Wheeler sanoo ”Ainoa tie ulos!”. Katso osa 4 kuva 3.
1980-90-luvuilla prosessin parantaminen tapahtui ensi sijassa koesuunnittelun (DoE, Taguchi) menetelmien avustamana. Prof. Genichi Taguchi esitteli oman menetelmänsä länsimaille (Ford) vuosina 1982-83. Tämä oli shokki laatukentässä ja sai ”laadunparannuksen” liikkeelle. Jotain uutta tarkastuksen rinnalle. (18, 19).
Laajennettu parannusmenetelmä Lean Six Sigma DMAIC yleistyi 2000-luvulla. Six Sigma on osin rakennettu Genichi Taguchin ideoiden pohjalta. (2)
Ennen Six Sigmaa käytettiin tehokasta 14 askeleen menettelyä (Taguchi), kuva 16, jonka keskiössä on monimuuttujakoe eli koesuunnittelu (DOE) ja testaus kuten Deming opetti laatuympyrällä.
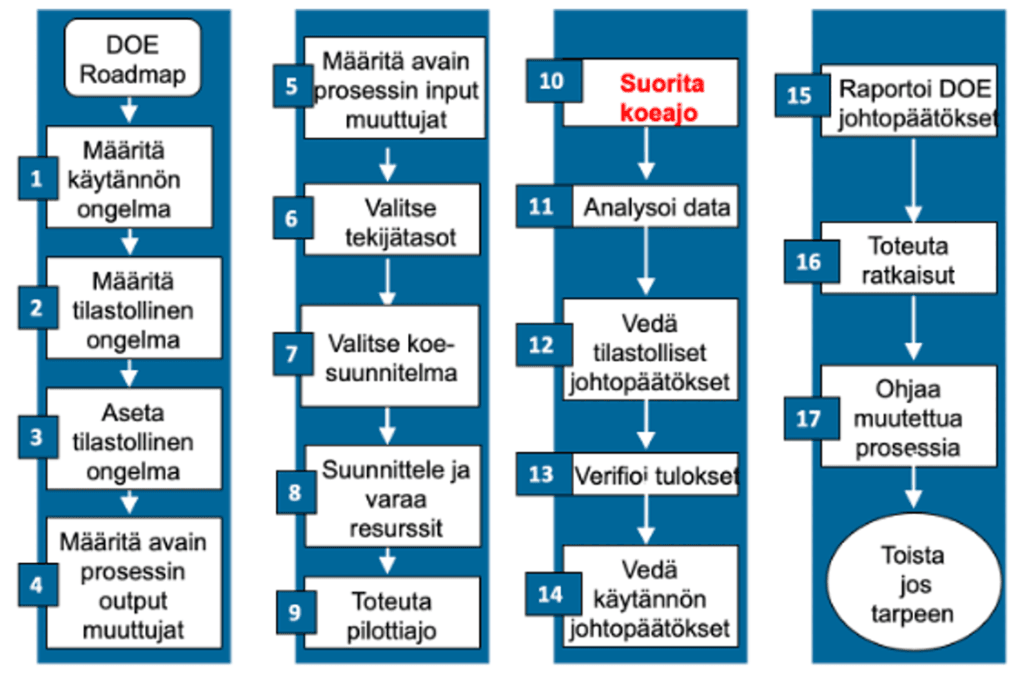
Tämän menettelyn suurimmaksi ongelmaksi muodostui, kuinka voidaan tehokkaasti löytää ja priorisoida keskeiset vaikuttavat kausaalitekijät (inputit): Kohdat 5-6 kuvassa.
Tämä ratkaistiin niin sanotulla loogisella suodattimella (kuva 17), josta ajan myötä kehittyi Lean Six Sigma (2).
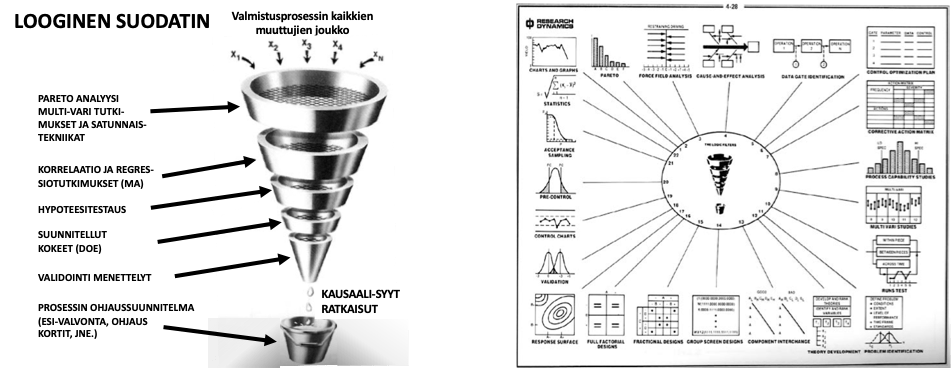
Six Sigmassa kolmella vaiheella DMA, määrittely (Define), mittaus (Measure) ja analyysi (Analysis) voidaan poissulkutekniikalla valita tekijäehdokkaat, joiden yhteisvaikutuksella ehkä saadaan aikaan parannus. Suppilo kuvaa poissuljettuja tekijöitä.
Yksi keskeisistä laatuperiaatteista on: eliminoi ensin vaihtelu ja säädä vasta sitten keskiarvoa; vaihtelua ei voi kompensoida toisin kuin keskiarvoa, jota voi kompensoida (säätää).
Poista laatutauluilla erityissyyt (vaihtelu) ja paranna vasta sitten Lean ja Six Sigmalla!
Kuvassa 18 on esitettynä samaan tuotteeseen ja tuoteryhmään kohdistettuna erityissyyn ratkaisu (laatutaulu) ja satunnaissyyn eli systeemisyyn ratkaisu käyttämällä hyväksi koesuunnittelutekniikkaa. (18, 19).
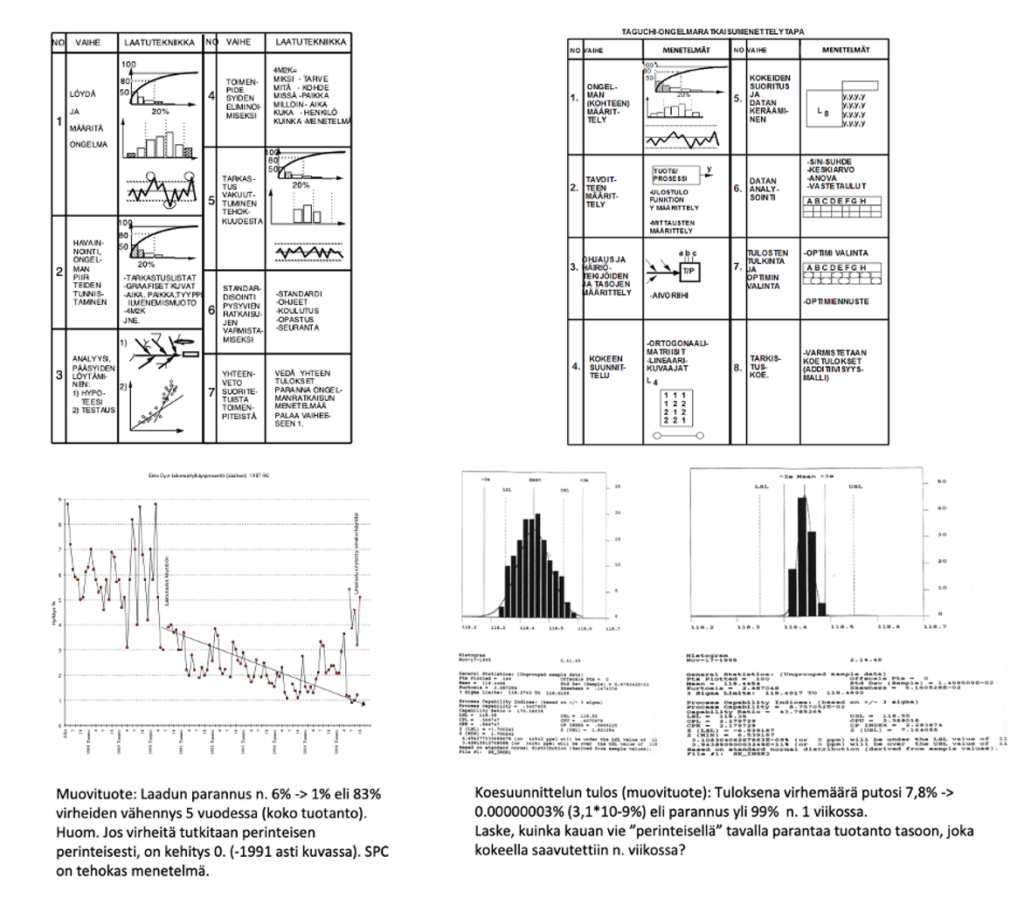
Koesuunnittelutekniikan (≈ Lean Six Sigma) on arvioitu olevan noin 200 x tehokkaamman perinteisiin menetelmiin verrattuna, mutta voidaan soveltaa vain stabiiliin prosessiin ja tuotteisiin.
Case 2. Eimo-Muovi Oy. Systeemitason parannus. Kuvan 18 yksityiskohtainen ”dia”esitys.
Esimerkki: Eimo Oy Laatu Juhani Ranivaara Taguchi- kokeet L12
Matkapuhelin käyttölaitteen kuori
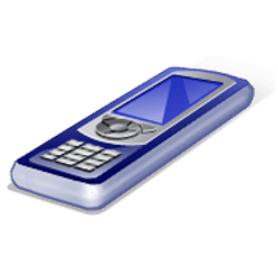
Tavoite: Hallita ja ohjata ruiskuvaluprosessia siten, että tuotteen pituusmitan vaihtelua voidaan pienentää ja samalla pitää mitan keskiarvo tavoitearvossa.
Kokeen suunnittelu: Valitaan muovikoneelle asetusarvot (tekijät), joilla voidaan vaikuttaa ja säätää tuotteen pituudesta mitattua Cp ja Cpk -lukuja. Koe päätettiin toteuttaa L12-matriisilla.
Esimerkin kohde on Nokian kännykän kuoren kokonaispituus 118,45 ±0,1 mm. Jos tämän pituuden vaihtelu (poikkeamat) saadaan pienemmäksi σ <0,057 mm, niin kaikkien muidenkin mittojen vaihtelu minimoituu. Tavoite σ <0,015
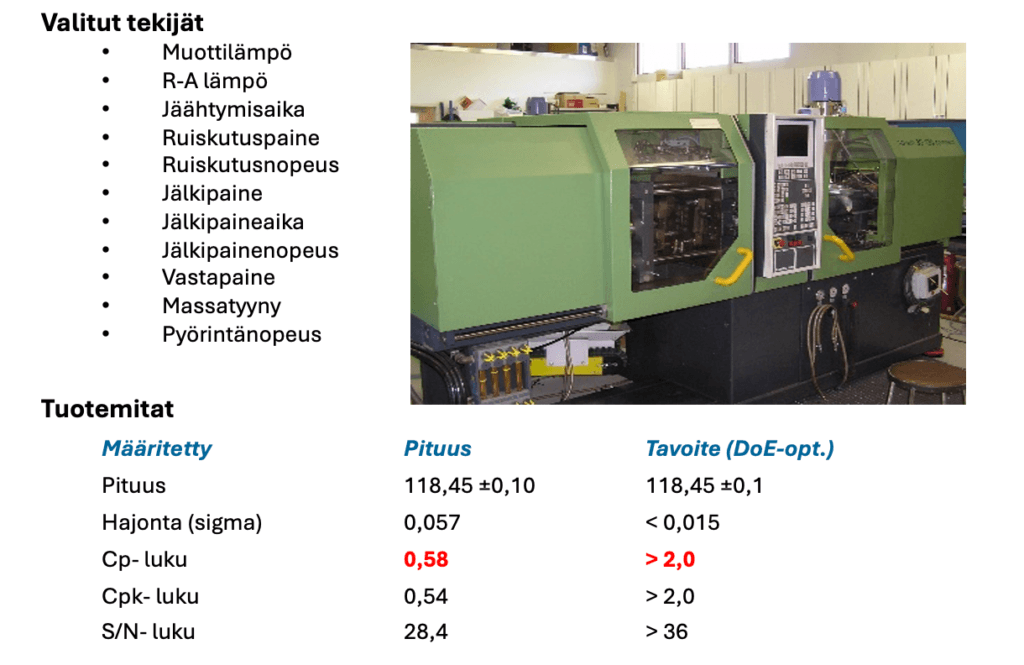
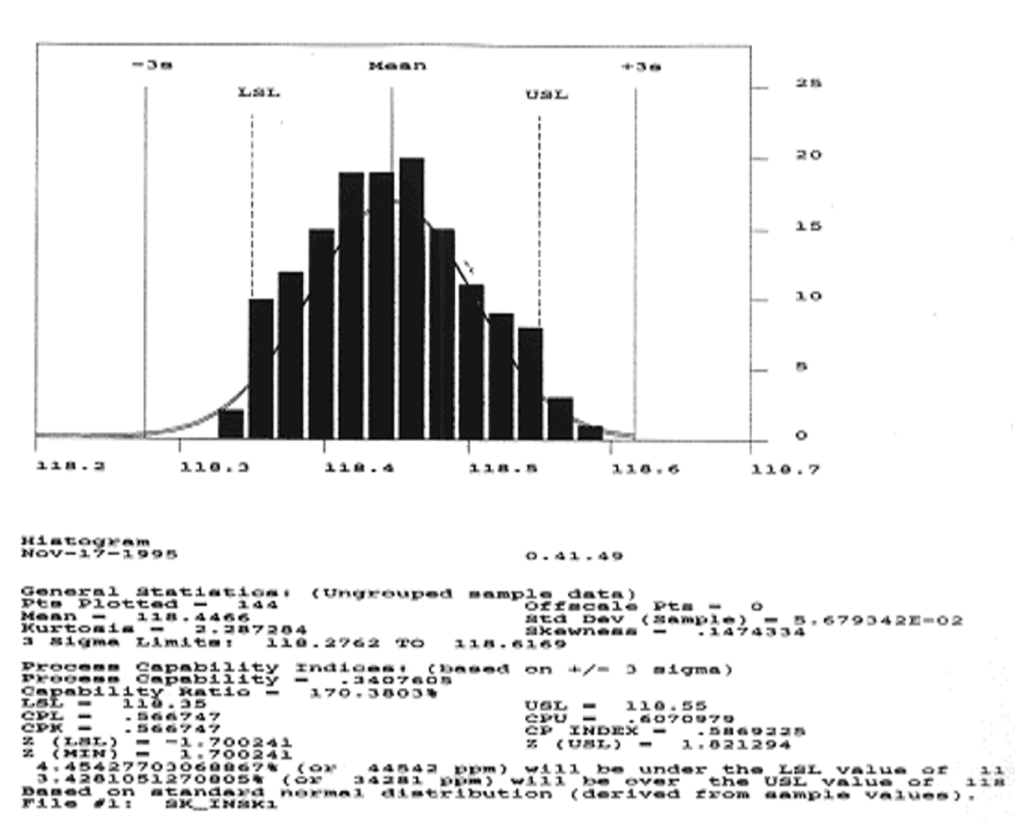
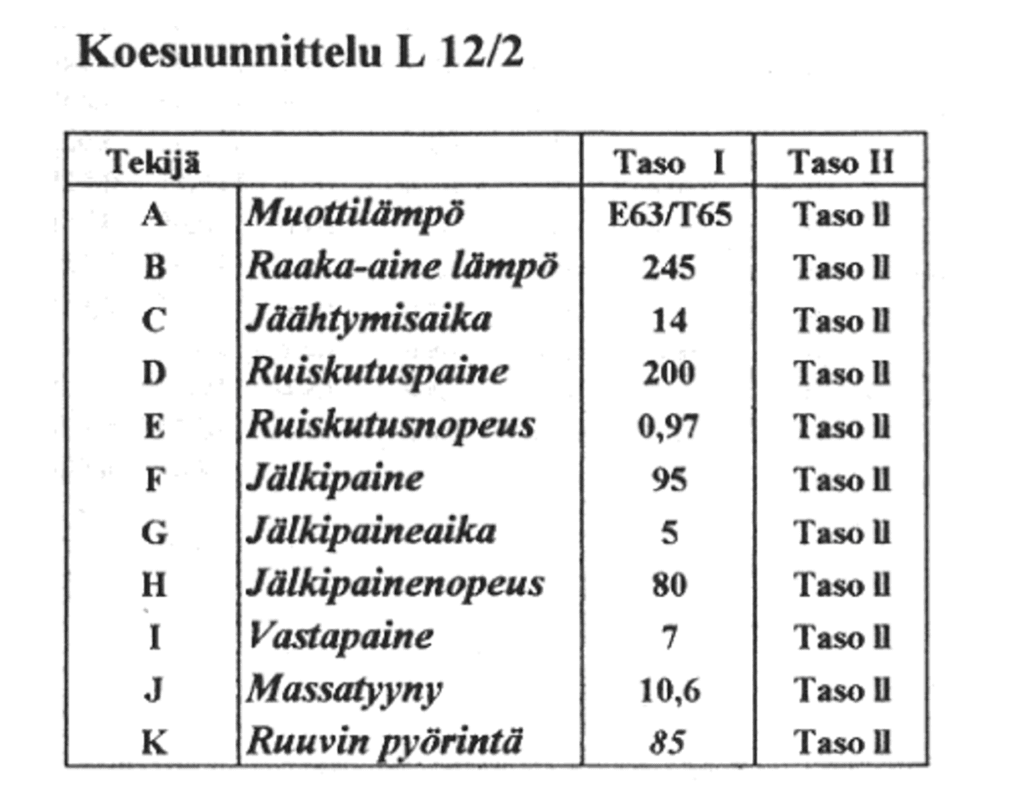
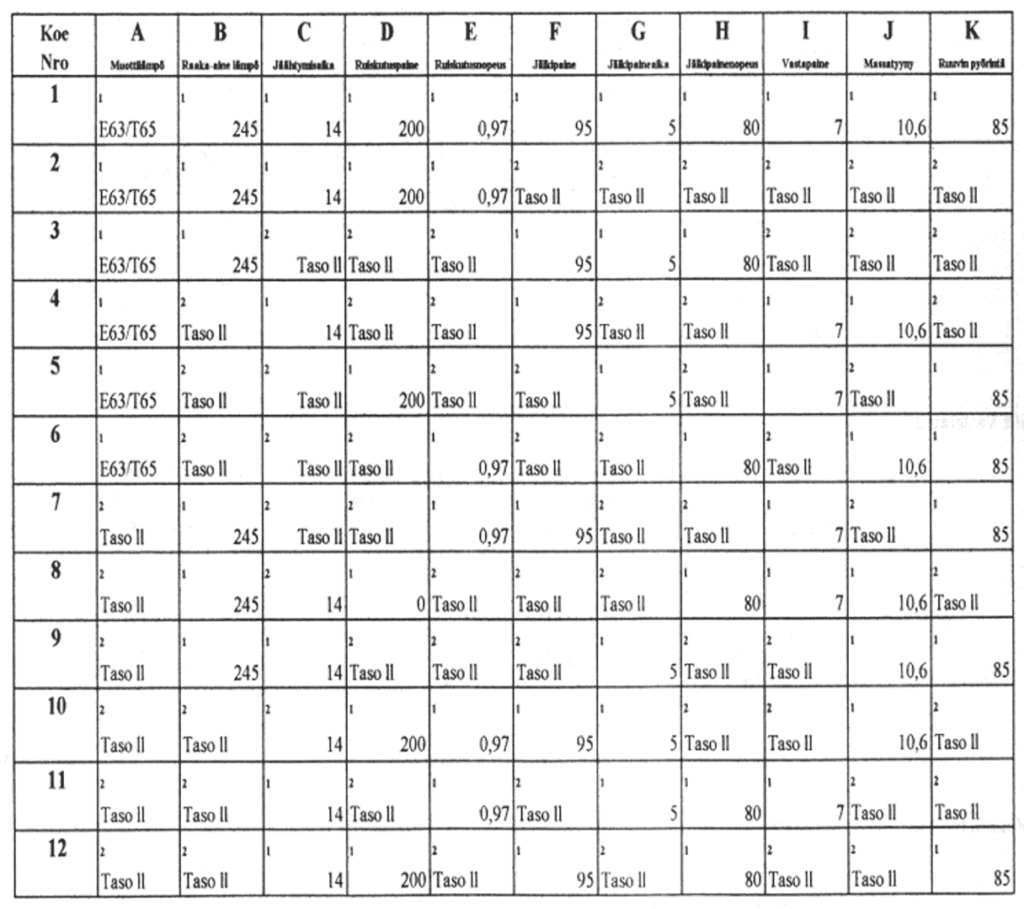
L12 -ortogonaalimatriisissa on 12 ajoa (riviä) 11 sarakkeessa A, B … J, K, jotka edustavat tekijämuutosta. Jokaisen rivin asetusarvoilla on ajettu 120 kännykän kuorta ja otettu näistä joka 10. eli 12 kpl näyte. Matriisiin on kirjoitettu ajoarvot kullekin riville. Ortogonaalimatriisi on symmetrinen 11 ulotteinen kohtisuora matemaattinen avaruus, joka mahdollistaa 12 koeajolla testata 2048 parannusyhdistelmää. (Katso artikkeli: Lean Six Sigma, suorituskyky ja monimuuttujakokeet)
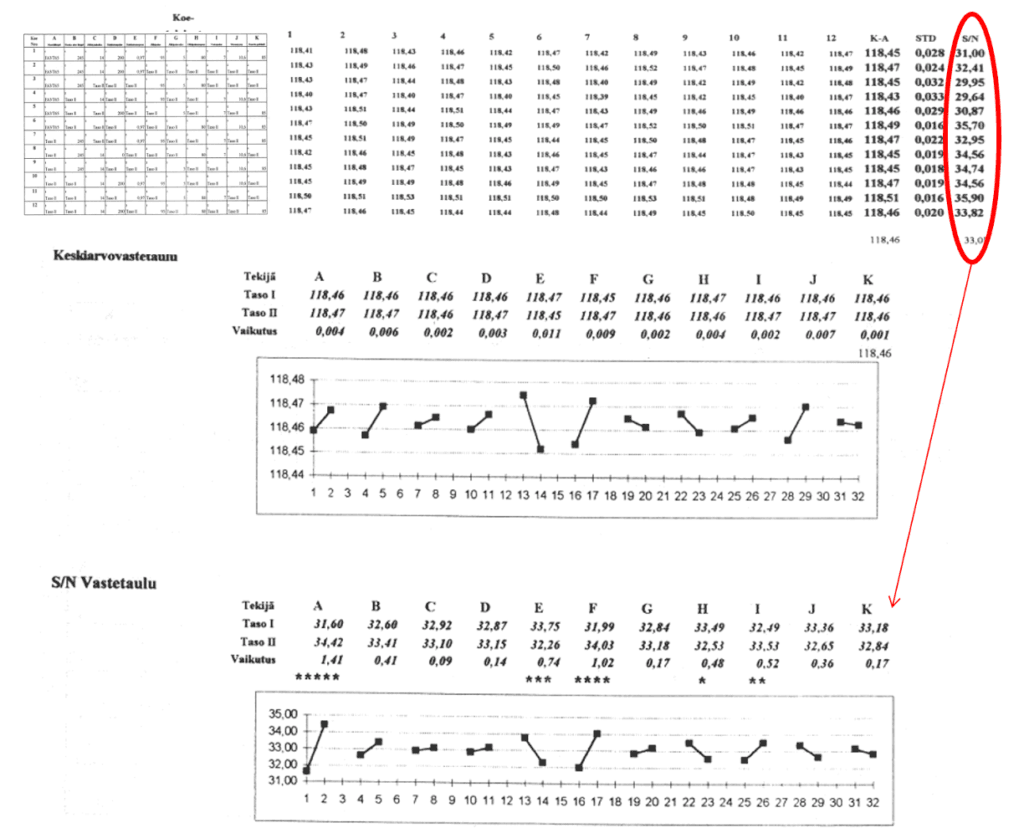
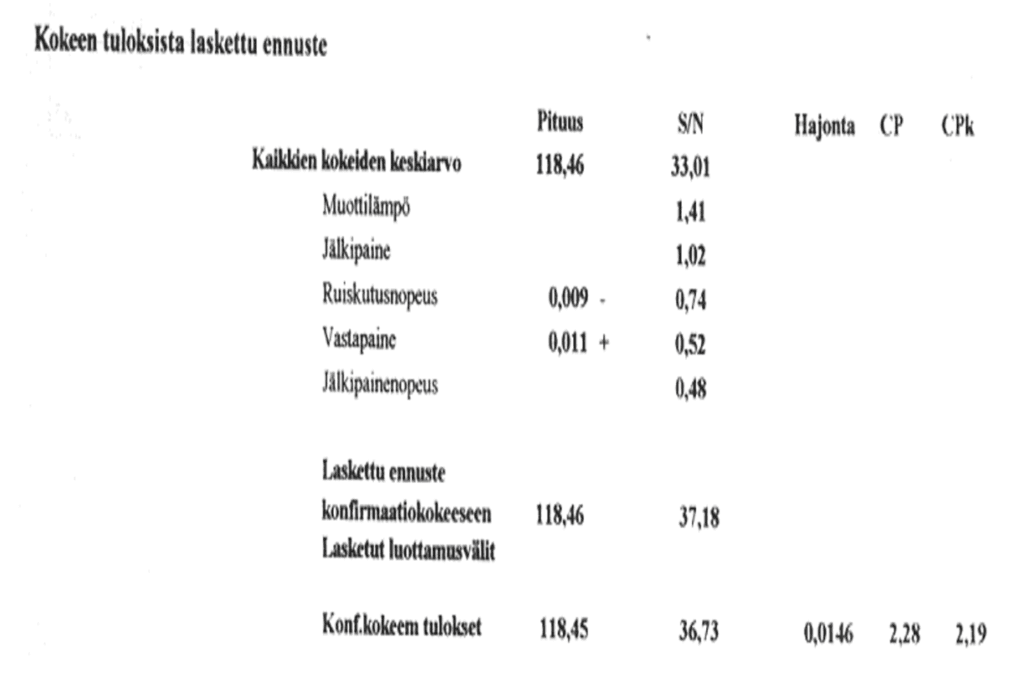
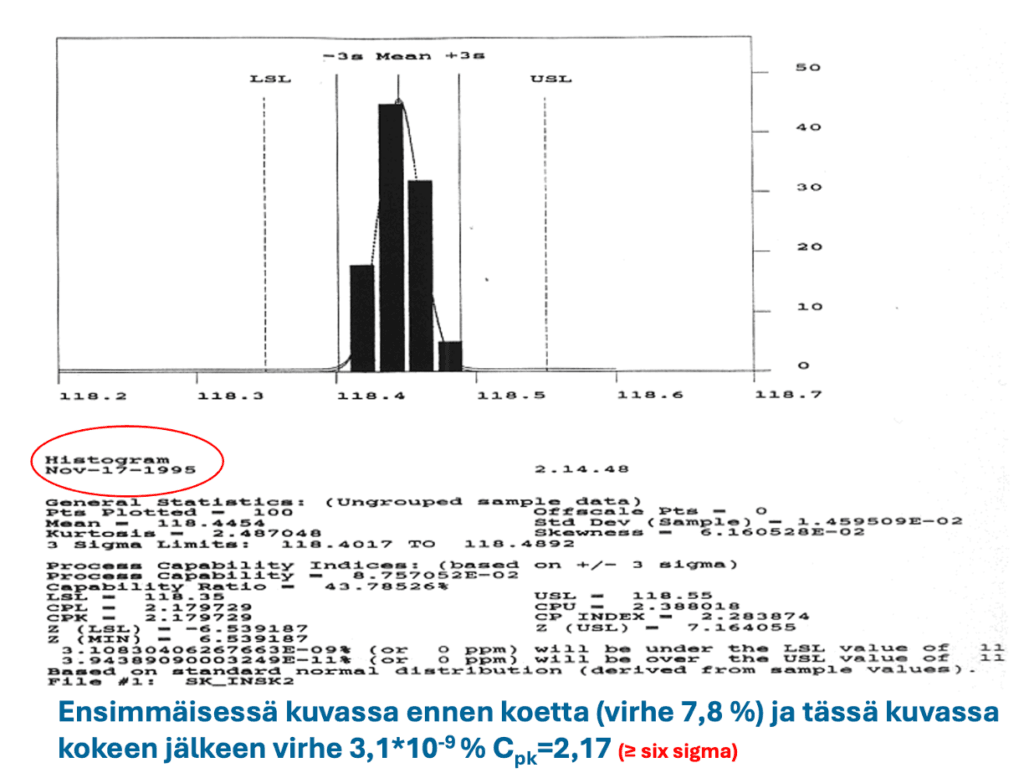
Esimerkin arvoja ei voi löytää ja selvittää juurisyyanalyysien avulla tai normaaleilla ongelmanratkaisumenetelmillä, koska ne eivät kata keskinäisvaikutusten ja epälineaaristen vaikutusten mahdollisuutta. Vain monimuuttujakokeilla voidaan optimoida poikkeamat.
Erityissyyperusteisissa ongelmissa voimme esittää kysymyksen viisi kertaa Miksi, Miksi, Miksi, Miksi, Miksi, kuinka (5 Miksi, 1 Kuinka). Oleellista on, että haemme yleensä yhtä syytä, juurisyytä tai joskus kutsuttu myös taustasyyksi. Tässä menetelmässä on lukuisia heikkouksia, jotka jo Sakichi Toyoda havaitsi. Siksi juurisyyanalyysistä on kehitetty lukuisia erilaisia versioista eri sovellutuskohteisiin, joilla puutteet on yritetty kiertää!
Satunnaissyyperusteisessa eli systeemin sisäisessä ongelmassa (suorituskyvyssä) joudumme käyttämään ”loogista suodatinta” (kuva 18), jossa loogisen päättelyn (deduktio) ja tilastollisten analyysien ja ei-tilastollisten kriteerien avulla valitsemme/priorisoimme joukon tekijöitä (5-19), joiden vaikutuksia testataan samanaikaisesti (induktio). Tämä siksi, että syy on satunnaisten tekijöiden yhteisvaikutus.
Systeemiteoriassa on usein päädytty viiden tekijän samanaikaiseen yhteisvaikutukseen, jotta muutos, transformaatio, tapahtuisi.
7. Yhteenveto laatutaulun analysoinnista ja toimenpiteistä
Laatutaulu ”puhdistaa” erityissyyt muutamassa kuukaudessa ja stabiloi prosessin. Laatutaulu ja siihen liittyvä menettely ei ole ennaltaehkäisy. Entropia ja kaaos painaa systeemiin ja prosessiin jatkuvasti erityissyitä, mutta ehkä vähemmän. Poista ja korjaa ne välittömästi. Pidä laatutaulua (SPC) tästä ikuisuuteen!
Erityissyiden vähennyttyä satunnaissyiden vaikutus tulee vallitsevaksi ja tarvitaan laatutaulujen rinnalle Lean ja Lean Six Sigma tai vastaava menetelmä systeemin ja prosessin suorituskyvyn parantamiseen. Tätä kutsutaan ”jatkuvaksi parantamiseksi”, joka vähentää merkittävästi ja pysyvästi poikkeamia.
Laatutaulua voidaan analysoida lukuisilla eri tavoilla. Helpoin tapa on tarkastella ja etsiä taloudellisesti merkittäviä muutoksia ”silmällä”. Ohjausrajat on helppo oppia, kun ymmärtää SPC:n konseptin. Pelkkä tietämys riittää. Tämän tietämyksen siirtäminen koko organisaatioon voi olla vaikeaa, jos viestit ovat vain sanallisia. Laatutaulu ja siihen liitetty menettely auttaa hyväksyttävässä viestinnässä. Voidaan turvautua tilastolliseen analyysiin ja tauluihin merkittyihin C- rajoihin ja erityissyytauluun. Taulu korvaa/poistaa mielivaltaisen pomottamisen.
Laatutaulun vasempaan laitaan voi laskea Poisson-jakauman perusteella jokaiselle poikkeaman (virheen, vian, hukan) muodolle induktiivisen yläohjausrajan C, joka perustuu aikaisempiin havaintoihin (5-20 päivää). Tämä raja ilmaisee taloudellisesti merkittävän muutoksen alarajan. Jos raja ylittyy, on järkevää yrittää etsiä juurisyytä. Yleensä tämä muutos löytyy helposti ja myös korjaus/parannustoimi muutoksen estämiseksi.
Ohjausrajan alapuolelle (sisäpuolelle) jäävät virheet/poikkeamat edustavat satunnaissyyperusteisia. Käytettäessä laatutaulua pitkään, osa näistä satunnaissyistä ”kuoriutuu” erityissyyksi ja lopulta jää jäljelle systeemin/prosessin omasta huojunnasta johtuvat poikkeamat eli prosessin suorituskyky.
Suorituskykyä voidaan parantaa käyttämällä erityistä kausaalitekniikkaa, Six Sigmaa, Taguchi jne, joilla seulotaan kokeellisesti suuresta tekijäjoukosta vaikuttavat kausaalitekijät ja tehdään näihin sopivat muutokset. Saadaan aikaan radikaali laadun ja suorituskyvyn parannus (improvement). Katso kännykän kuoren mitan vaihtelun minimointi.
Loppusanat: Laadun ohjaus (stabilointi) ja parantaminen on kohtuullisen helppoa, jos opettelee laadun – stabiloinnin ja parantamisen – perusteet ja teoriat riittävän hyvin ja noudattaa niitä. Jos tulosta ei tule, olet eksyksissä. Jotain on väärin!
Keskeisin ongelma on, että yrityksessä ja tunnusluvuissa tapahtuvat muutokset ovat liian hitaita, jotta kokemusperusteisesti työssä oppimalla voisi löytää ”parhaita käytäntöjä” tai saada parannusta ja tulosta aikaan. Olen artikkelisarjassa näyttänyt 5 – 25 vuoden aikasarjoja, joilla voidaan osoittaa, toimiiko jokin käytäntö vai ei. Muista ylläpitää seurantakäyriä, jotta voit varmistua kestävästä parannuksesta.
Laadusta ja sen tekemisestä on paljon virheellisiä uskomuksia ja käytäntöjä niin johtajilla kuin työntekijöillä. Nämä ovat syntyneet yhden tai kahden tapahtuman yleistyksistä tai jonkun kertomana ”tarinana” ja laatutekniikan perusteiden osaamattomuudesta. Laatutekniikka perustuu tieteeseen, Quality Science. Paljon väärää tietoa ja uskomuksia on liikkeellä!
Turvaudu tieteellisesti todistettuihin ja hyväksyttyihin laatuteorioihin ja tekniikoihin. Varmista, kuka opettaa, mistä on oppinut (kirjat, lähteet) ja mitä konkreettista näyttöä on osaamisesta! Hanki laaturaamattu.
Hyviä tieteellisiä lähteitä ovat julkaisut: ASQ:n julkaisut: Technometrics, Journal of Quality Technology (JQT), Quality Engineering, Quality Progress. ASQ:n jäsenenä pääset näiden julkaisujen vuosikertoihin yli 50 vuoden ajalta ja voit tutustua varmistettuun laatutekniikkaan. Jäsenmaksu $ 31/vuosi. Keskeiset ja uusimmat laatukirjat löydät myös verkkokaupastamme.
Lähteet:
- Walter A. Shewhart: Economic Control of Quality of Manufactured Product, 1931
- Eero E. Karjalainen, Tanja Karjalainen: Lean Six Sigma 2.0 ja laatuteknologia, 2020
- Artikkeli: Tilastollinen ymmärrys ja käyttö (Osa 0), 2024
- Artikkeli: Laatutaulu – Osa 1: virheet ja hukka (Osa 1), 2024
- Artikkeli: Laatutaulu – Osa 2: kehitysvaiheet I-II (Osa 2), 2024
- Artikkeli: Laatutaulu – Osa 3: kehitysvaiheet III-VI (Osa 3), 2025
- Artikkeli: Laatutaulu – Osa 4: luominen, tiedon keruu ja käyttöönotto (Osa 4), 2025
- W. Edwards Deming: Out of the Crisis, 1982
- W. Edwards Deming: The New Economics for Industry, Government, Education, 1993
- Eero E. Karjalainen, Tanja Karjalainen: Laatutaulu – Tehokas menetelmä laadunohjaukseen ja parannukseen, 2024
- Artikkeli: Jatkuvasta tarkastuksesta ja korjauksesta jatkuvaan parantamiseen tai sitten ei?, 2021
- Douglas C. Montgomery: Introduction to Statistical Quality Control, 2nd Edition (1991)
- Douglas C. Montgomery: Introduction to Statistical Quality Control, 5th Edition (2005)
- Donald Wheeler: Understanding Statistical Process Control, 1992
- Donald J. Wheeler: Advanced Topics in Statistical Process Control, 1995
- Nancy R. Tague: The Quality Toolbox, 3rd Edition, 2023
- Tanja Karjalainen, Eero E. Karjalainen: Laatujohtamisoppien (TQM) soveltaminen PK-yritykseen – SPC, systeemiteoria, TOC teoria, 2000
- Eero E. Karjalainen: Tuotteen ja prosessin optimointi koesuunnittelulla – Taguchi- menetelmä, 1989
- Eero E. Karjalainen: Teollinen koesuunnittelu – Esimerkkejä Suomessa toteutetusta kokeellisesta tuotteen ja prosessin suunnittelusta Taguchi- menetelmällä, 1992
Tutustu kurssitarjontaamme!
Tilaa uutiskirje
Liity postituslistalle ja saat uusimmat artikkelit suoraan sähköpostiisi.
Tämä lomake on suojattu Google reCAPTCHA:lla. Lue tietosuojaseloste ja käyttöehdot.
Liittymällä postituslistalle hyväksyt Quality Knowhow Karjalainen Oy:n tietosuojaselosteen ja Quality Knowhow Karjalainen Oy voi lähettää sinulle ajankohtaisia artikkeleita, videoita sekä tietoa ja tarjouksia kursseista, kirjoista sekä ohjelmistoista.
Tämä lomake on suojattu Google reCAPTCHA:lla. Lue tietosuojaseloste ja käyttöehdot.